Flowserve 132000 LinedFlow Linear Lined Globe Control Valve IOM User Manual
Page 4
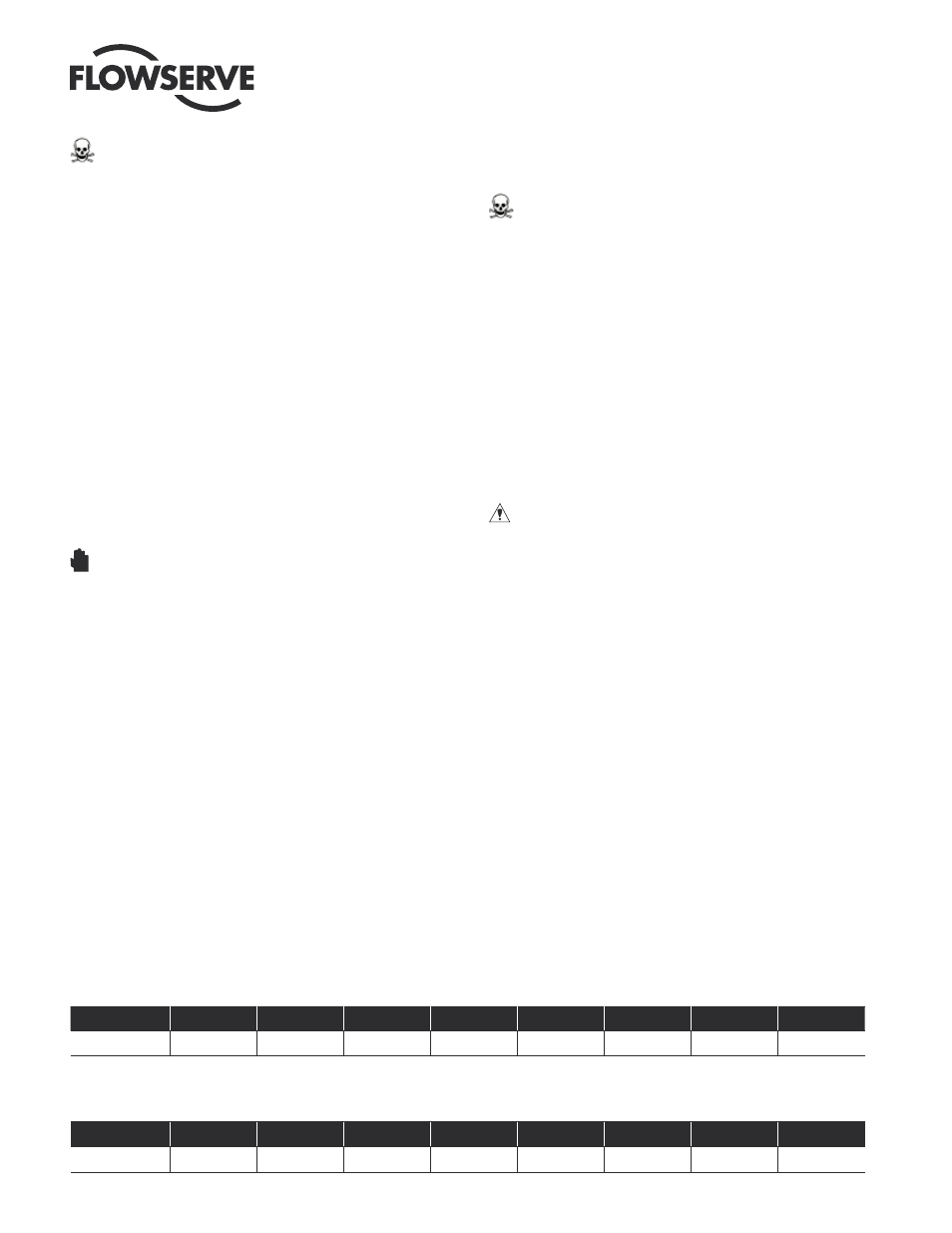
®
User Instructions LinedFlow - KMENIM3202-02 01/12
4
DaNgER: Do not install valves whose approved pressure
and temperature range is not sufficient for the operating
conditions. The limits for use are marked on the valves.
Moreover, use only valves suitable for the operating medium
in question.
Failure to observe these precautions can pose a danger for
the user and cause damage to the piping system.
5.2
The actuator must correspond to the intended connections
and control data.
5.3
The connection flanges must be inline with the valve
connections and parallel. connection flanges which are not
parallel can damage the plastic liner during installation!
5.4
Before installing, thoroughly clean the valve and the pipeline
to remove any contamination, particularly hard foreign parti-
cles.
5.5
In particular, it is necessary to ensure that the sealing sur-
faces on the flange connection are free of all contamination
when installing.
5.6
When inserting the valve into a pipeline already installed, the
distance between the ends of the pipeline must be sufficient
to prevent damage to any of the sealing surfaces.
WaRNINg:
Tighten all flange connections to the torques
specified in Tables 1a or 1b. When using torque wrenches,
ensure that these torques are reached, however not excee-
ded.
The values in the table apply for flanges according to
EN1092, PN10/16 for a maximum operating pressure of
10 bar. Values for other flanges can be obtained from the
manufacturer.
5.7
Valves are to be installed in the appropriate flow direction.
The flow direction is indicated by an arrow on the valve.
5.8
Observe the appropriate instructions for connecting the
actuator to the valve. Control valves are equipped with a
positioner. The connections for air supply and signals are
marked clearly (see also applicable operating instructions for
the positioner). The maximum air supply is specified on the
name plate. If the air supply exceeds the pressure specified
on the rating plate, a pressure reduction station is required.
If no instrument air is available, install an air filter in the air
supply line if required.
5.9
After completion of installation, perform a function test with
the control signals: The valve should open and close properly
corresponding to the control commands. Always eliminate
any recognizable malfunctions before startup. See also
applicable sections in maintenance regulations for this valve
series.
DaNgER:
Improperly executed control commands can pose
a danger for life and limb and damage to the piping system
and/or the valve.
6
PRESSURE TESTINg PIPINg SEcTION
The valve has already been pressure-tested by the manuf-
acturer. When pressure testing a section of the pipeline with
valves installed, observe the following:
6.1
First thoroughly flush newly installed piping systems to
remove all foreign objects.
6.2
Valve opened: The test pressure should not exceed the
value of 1.5 x PN (according to nameplate):
6.3
Valve closed: The test pressure should not exceed the value
1.1 x PN (according to nameplate).
If a leak occurs on the valve, observe Section 8 “Trouble-
shooting”.
caUTION: If the flange connection with plastic liner leaks:
First retighten flange connection to torque specified in Table
1a or 1b in Section 5.6 (installation).
If the flange connection is still leaks:
Loosen flange connection. Check the flange connection to
ensure that it is smooth and parallel.
Check the sealing surfaces on both flanges: When the inner
lining is damaged, replace valve and/or counterflange.
STOP!
Table 1a: Tightening Torques for Flange connections, Flanges EN1092 (DIN)
DN [mm]
15
20
25
40
50
80
100
150
M
A
[Nm]
10
18
25
50
65
65
65
140
Table 1b: Tightening Torques for Flange connections, Flanges EN1759 (aNSI)
NW [inch]
½"
¾"
1"
1½"
2"
3"
4"
6"
M
A
[Nm]
8
11
15
26
60
100
76
100