Worcester controls – Flowserve Factory Mutual Approved Oil or Gas Safety Shutoff Valve User Manual
Page 10
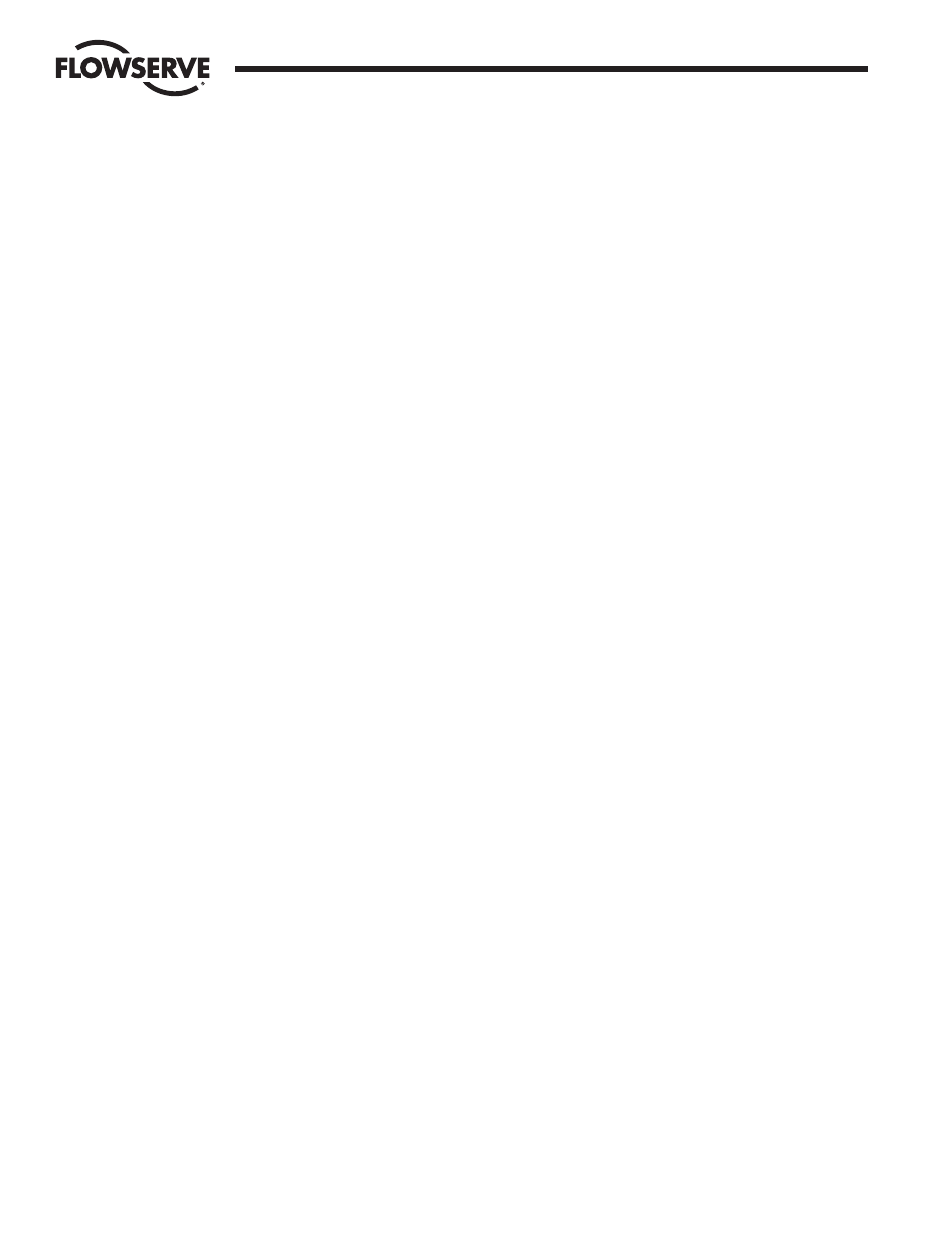
10
Factory Mutual Approved Oil or Gas Safety Shutoff Valves
WCAIM2054
d. To ensure proper meshing of teeth, move the shaft 15 to
20 degrees counterclockwise (CCW) from its normal
position when the piston assemblies are located at the
body ends. (See Figure 2.)
NOTE: The “normal position” of the shaft on the 10–20
sizes is when the top flats are parallel to the main axis of
the actuator body. On the 25–42 sizes, the teeth of the
shaft will be on the left side of the actuator when viewed
from the ends of actuator (see Figure 1).
e. With the piston assemblies in the body, gently push each
piston into the body. Turn the top shaft extension
clockwise (CW). Do not allow the pistons to “cock”.
At the proper point of engagement between the shaft and
piston assemblies, both piston assemblies will move
toward the center of the body when turning the top shaft
extension of the actuator clockwise (CW).
f. Once the center gear and pistons are properly engaged,
ensure that smooth movement and 90° operation can
occur without moving the pistons out of the actuator
body. This is important!
g. Install O-ring (15A) into and replace the actuator end
caps, (5A and 5B), noting that the “foolproof” pin
between the body and end cap mates properly. See steps
j through o below for spring installation, before replacing
end caps.
NOTE: When installing the end cap O-rings, use a small
amount of general-purpose lubricant, such as Vaseline, to
hold them in place for ease of assembly and to avoid
having them fall and get pinched.
On Rev. R1 and earlier actuators, be sure O-ring is
installed in groove on end cap.
h. Replace the stainless steel washer over the top shaft
extension.
i.
VERY IMPORATNT: Install the NEW shaft clip (15F) into its
mating groove on the top shaft extension. (The removed
shaft clip is not to be reused.) Place the numbered side
up on the shaft clip and be certain the clip is fully seated
in its groove. See note on page 8 for installation of spring
ring shaft clip (which new rebuilding kits will contain).
j. Replace springs in end cap. Ensure that the springs are
replaced in their identical position in the end cap from
where they were removed.
IMPORTANT: When less that the standard number of
springs is used in each end cap, these springs should be
positioned according to the air supply figures listed below.
Sizes 10–35 Rev. R2 through R6 and Sizes 40 and 42 Rev.
R3 through R6
60 psi – 8 springs – 4 per end cap.
Remove center spring.
Sizes 10–40 Rev. R1
60 psi – 18 springs – 9 per end cap. Remove the required
number of springs starting in the center. Remaining
springs should be as evenly spaced as possible.
k. If the actuator is being repaired due to a failed spring,
replace all the springs in the actuator, as well as any other
parts that may have been damaged.
l. When replacing the springs, place the springs in the end
cap pocket after thoroughly lubricating each spring. Be
generous!
m. With the springs pointing up and the end cap on a solid
surface, place the actuator body over the springs and the
proper end cap. (Each end cap can only be mounted to
one end of the actuator body.)
n. Force the body down and begin by engaging two end cap
screws (5C) by hand through the end cap. Take each end
cap screw in SMALL and EQUAL turns. Once the end cap
is temporarily secured to the body, turn the actuator over
to its normal position and uniformly take up the four end
cap screws.
Uniformly load all the springs to prevent any spring from
buckling.
IMPORTANT: Locating nibs are permanently cast into the
Rev. R1 (all sizes) and the Rev. R3 through R6 (sizes
25–42) actuator piston face. The actuator springs must fit
over these locating nibs on the piston face. Care in
following these instructions will ensure proper alignment
of the spring in the actuator body and proper contact with
the piston face and end cap.
o. In a similar manner, as written in the previous steps,
replace the springs in the other end of the actuator body.
p. If solenoid control block was removed:
Place gasket (9) on solenoid control block (7) and attach
block securely to end cap to obtain a seal at gasket.
NOTE: If fiber gasket is used, work a generous amount of
assembly grease or Vaseline into the gasket prior to
assembly (wipe off excess grease). If a rubber gasket is
used, do not apply any grease—it must be installed dry.
q. Replace the position indicator (17) (if any) by locating on
center gear flats. Press firmly until locating nibs snap into
recess on pinion.
NOTE: Check that indicator, when located on center gear
(shaft), will show correct indication. Indicator is set up to
show valve closed on in-line mounting, i.e., pistons
together on actuator.
r. Mark Rebuild/Accessory Addition Label, if included in
repair kit, and apply to actuator.
Flow Control Division
Worcester Controls