Worcester controls – Flowserve Factory Mutual Approved Oil or Gas Safety Shutoff Valve User Manual
Page 4
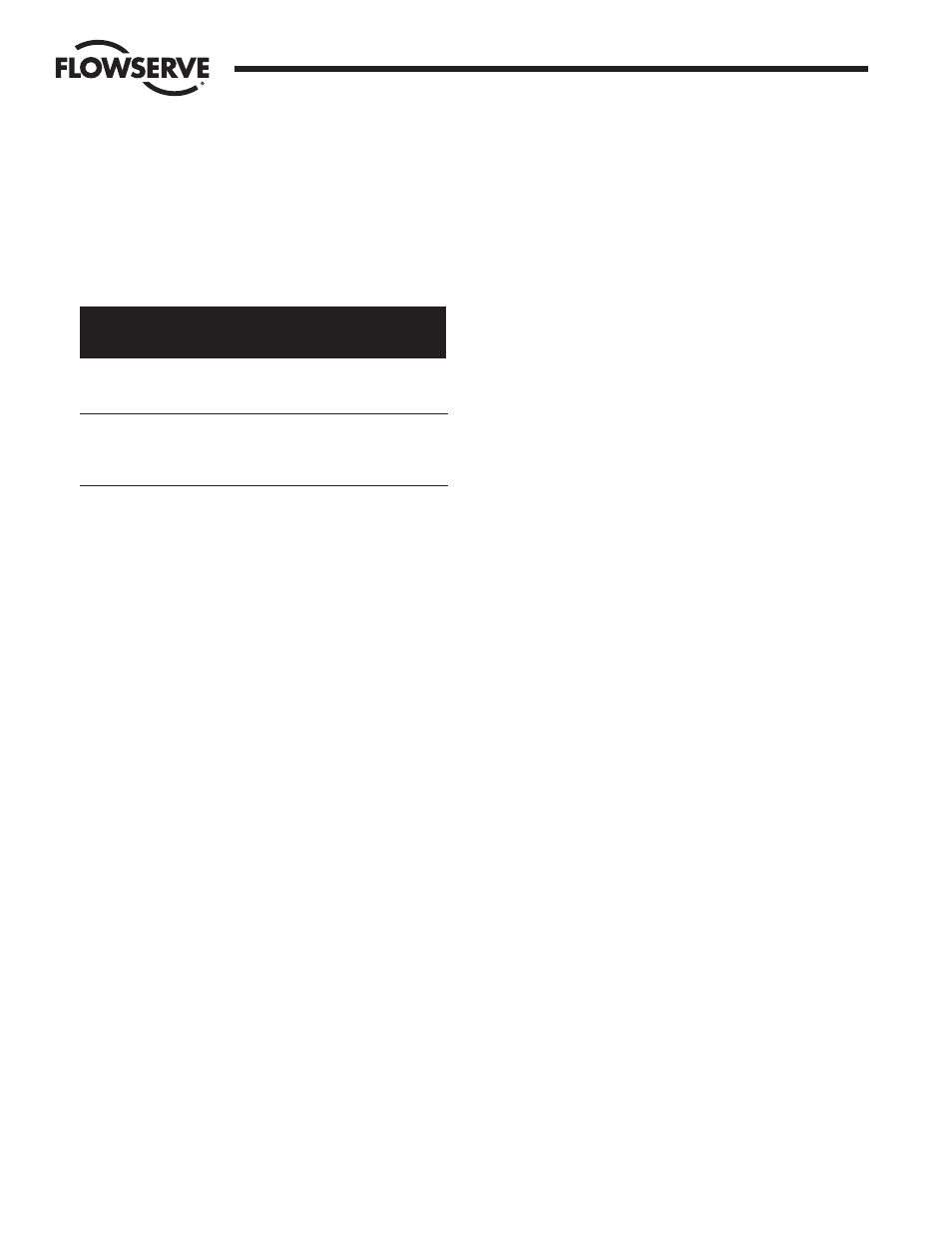
4
Factory Mutual Approved Oil or Gas Safety Shutoff Valves
WCAIM2054
The valve styles will be as follows:
Z|v"–2"
Three-Piece Reduced Port (Series 44)
Z|v"–4"
Three-Piece Full Port (Series 59)
2"–8"
Flanged Reduced Port (Series 51 and 52)
3"–4"
Flangeless Reduced Port (Series 4, Type 151)
To order the proper repair kit, use the following format.
NOTE: For
valve styles 4 (151) and 52, repair kits can be ordered as RK51:
Revision,
Valve
Valve
Seat
Seal
P, T, C, etc.
Size
Style
Material
Material
No. (If Any)
Examples:
3"
RK 51
R
T
R5
2"
RK44
T
T
P1845
CAUTION: If the seats and seals installed differ from those
removed, the valve nameplate must be replaced or remarked
to indicate the altered materials and ratings, or valve tagged
to so indicate.
If spare parts are necessary, include the complete valve code as
given on the valve nameplate, stop plate or actuator bracket
nameplate and then the part(s) that is (are) being ordered.
The terminology shown in the exploded views and Part Listings
on following pages is standard.
B. Disassembly
1. Disassemble
Z|v"–2" 44 three-piece and Z|v"–1Z|x" 59 valves as
follows:
a. Place valve in open position, remove three body nuts and
bolts, loosen fourth, swing out center section from
between pipe ends with valve open.
b. With valve in closed position, remove old seats, body
seals and ball.
c. Using a wrench to prevent stem from turning, remove
self-locking stem nut, Belleville washers, and stem seal
follower from stem. Remove stem through body cavity.
d. Remove thrust bearings from body or stem; stem seals
and stem seal protector from recess in top of body.
e. Discard all seats, seals and Belleville washers removed
from the valve.
2. Disassemble 2"–4" 59 three-piece valves as follows:
a. Place valve in open position. Remove all body nuts and
bolts or studs and lift out center section from between
pipe ends.
b. With valve in closed position, remove old seats, seat
retainer (if present), body seals and ball.
c. Prevent stem from turning by holding inside body. (The
ball can be inserted and prevented from rotating with a
non-metallic rod such as a screwdriver handle.) This will
hold the stem stationary without damaging the ball.
d. Remove retaining nut and spacer from stem.
e. Push stem into body cavity and remove. Retain follower
and centering washer(s). There are no washers on 2"
valves.
f. Remove and discard stem seals and thrust bearing, which
may be stuck on the stem or in the body cavity.
3. Disassemble 2" 51/52 Flanged Valve as Follows:
a. Place valve in open position, unscrew all flange bolts and
remove valve from line.
b. Place valve with end plug up on a clean surface. Secure
by clamping or bolting.
c. Unscrew end plug. Set aside. If the body seal was not
removed with the end plug, remove it from the valve and
discard. Remove and discard near seat.
NOTE: If required, end plug assembly/disassembly tools
are available from your supplier or Flowserve.
d. Place valve in the closed position and remove the ball.
e. Remove self-locking stem nut. Use a wrench to prevent
stem from turning.
f. Remove and discard Belleville washers. Push stem into
ball cavity and remove.
g. Remove and discard stem seals, stem seal protector and
thrust bearings, which may be on the stem or in body
stem cavity, and far seat. Retain the follower.
4. Disassemble 3"–8" 51/52 flanged and 3"–4" 4 (151) flangeless
valves as follows:
a. Place valve in open position. Unscrew all flange bolts or
studs and nuts and remove valve from line.
b. Place valve in closed position, remove end plug retaining
screws.
c. Remove end plug. If necessary, drive end plug from valve
using wooden drift applied to ball.
d. Remove body seal, ball and seats. Discard seats and body
seal.
e. Using a wrench to prevent stem from turning, remove
retaining nut, spacer, and follower.
f. Push stem into body cavity and remove. Remove and
discard stem seals and thrust bearing. Remove and retain
any existing washers.
5. Visually inspect all valves as follows:
a. The ball and the surfaces against which the seats and
seals are installed should be undamaged, clean and free
of pit marks and scratches. Light marring from the action
of the ball against the seats is normal and will not affect
the operation of the valve. Flaws which can be seen but
not detected with fingertips are acceptable.
Flow Control Division
Worcester Controls