6 valve maintenance: troubleshooting, Nordstrom valves, Problem a: valve seat leakage – Flowserve Nordstrom Dynamic Balance Plug Valve and Double DB Plug Valve User Manual
Page 17
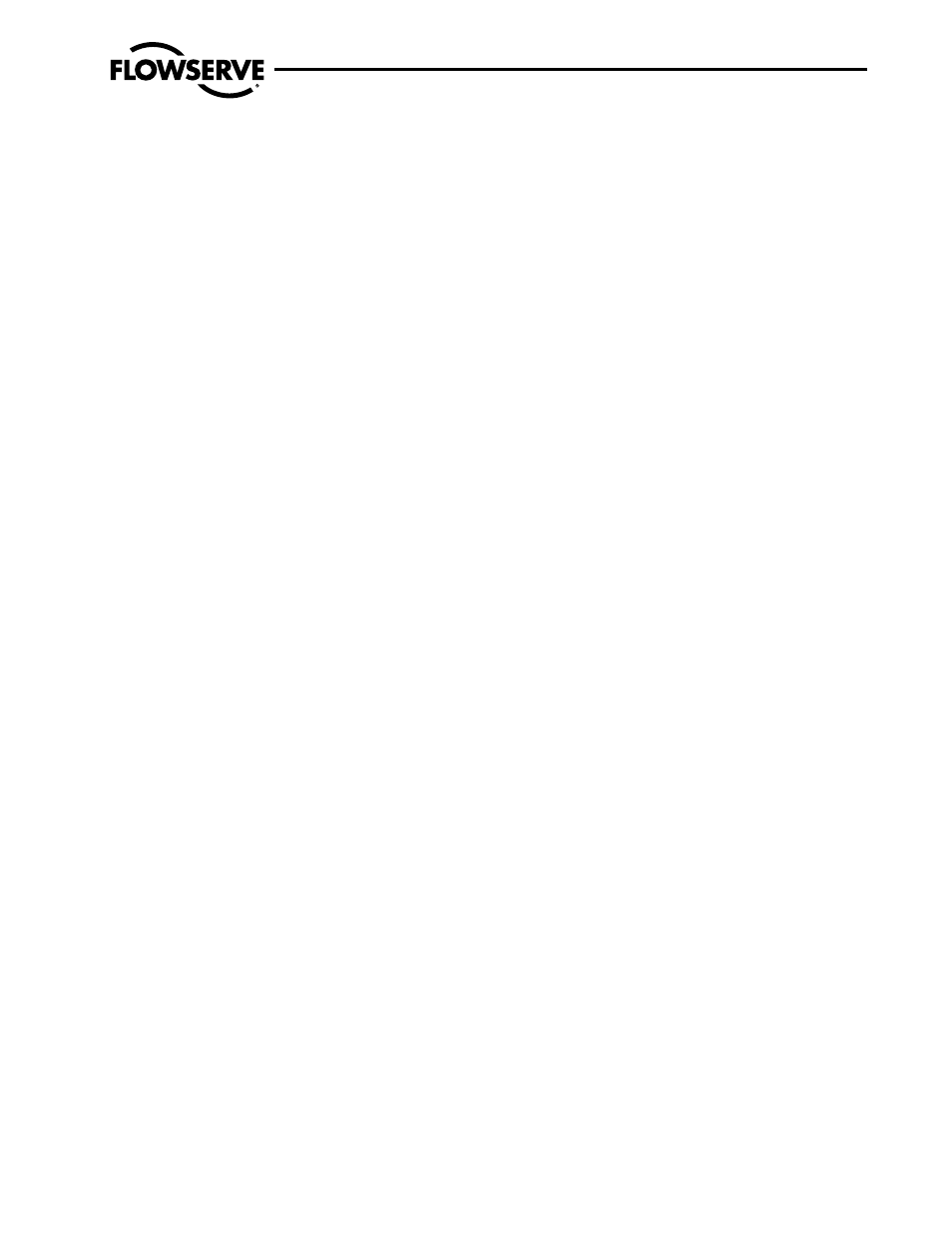
Flow Control
Nordstrom Valves
FCD NVENIM2005-01
Dynamic Balance
®
Plug Valve and Double DB
®
Double Isolation Plug Valve
17
even after you have injected more than enough sealant to fill the
valve.
This scenario signals one of the following conditions:
a. If the Plug is not locked in the Body Taper, then the Plug
may be unseated and additional sealant is bypassing the
Plug. This is normal and indicative of a properly maintained
and well-pressurized valve.
b. However, if the Plug is locked in the Taper and cannot be
operated, this indicates that the Plug or valve Body may be
damaged and sealant is bypassing the sealing surfaces.
c. If the valve is difficult to operate, the likely causes are the
same as those in Scenario Two: a) too tight an adjustment,
b) Stem corrosion, or c) gearing problems on gear-operated
valves.
Gauge Scenario Four The gauge indicates a continual rise in
pressure as sealant is injected but never indicates a pressure
decrease.
This scenario indicates three possible problems:
a. The valve Sealant Fitting is faulty.
b. The sealant system is blocked.
c. The Plug has seized in the Body Taper
To solve the problem:
Open and close the valve several times while continuing to inject
sealant. If conditions do not allow you to fully open or close the
valve, rotate the Plug back and forth (approximately 20°) several
times.
5. After you have injected the sealant, relieve the pressure within
the injection equipment and remove it from the Sealant Fitting.
6 Valve Maintenance:
Troubleshooting
This section lists some possible problems with the Dynamic Balance
Plug Valve, the probable causes, and the solutions. The procedures
are intended to serve as guides to remedy conditions you may
encounter when performing maintenance on your valve. The proce-
dures, as well as information shown on the Tables in this manual, are
based on factory valve-assembly procedures. Precise estimates of
field conditions are not feasible. Judgment and experience must be
applied when working on valves in actual field site conditions.
It is highly recommended that sealant be injected into the valve prior
to proceeding with valve adjustment or repair. Gauge scenarios, as
detailed earlier, will help you focus on specific solutions to remedy
your valve problem. Your sealant injection equipment should be
operating properly prior to diagnosing valve problems.
a
CAUTION: If a non-compressible fluid is trapped in the
center cavity of the Plug, when the valve is in the closed
position, injecting sealant at high pressures or high volumes
can cause the Plug to lock in place. This can also cause the
Cover Bolts to yield, thus producing Cover leakage.
Problem A: Valve seat leakage
Cause A1: Insufficient sealant in the valve
Solution A1
The lack of sufficient sealant to adequately fill and pressurize the
sealant system is the most common problem associated with seat
leakage. Inject the correct amount of sealant into the valve and again
check for seat leakage.
Cause A2: Plug adjustment too loose
Solution A2
One indication of loose plug adjustment is that the valve operating
torque is lower than normal. If possible, operate the valve a number
of times prior to adjusting the Plug Adjusting Screw and make
adjustments using the following procedures:
1. Remove the hex-head cap screw or thin 3-screw metal plate
located on the Bottom Cover of the valve to expose the Plug
Adjusting Screw. After the valve is assembled at the factory,
the Plug Adjusting Screw and valve Cover are marked by chisel
point to locate the position of factory adjustment. Check the Plug
Adjusting Screw for tampering.
2. If the Plug Adjusting Screw has been moved in a counterclock-
wise direction, insert the proper size hex-head wrench into
the hexagonal-shaped hole in the Plug Adjusting Screw and
retighten to the factory adjustment mark.
NOTE: During factory assembly, thread-locking compound is
applied to the Plug Adjusting Screw. Initially, the screw may be
difficult to turn.
3. Operate the valve back and forth through its 90° operating
range, and simultaneously tighten the Plug Adjusting Screw.
This action will help disperse previously injected valve sealant.
If operating conditions prevent rotating the Plug completely
through its 90° operating range, rotate the Plug through a 20°
arc to disperse the sealant. Continue to tighten the Plug Adjust-
ing Screw until a noticeable torque increase makes the Plug
harder to turn. This will indicate you have metal-to-metal contact
between the Body and Plug.
a
CAUTION: Overadjustment of the Plug Adjusting Screw
will lock the Plug into the Body Taper.