Nordstrom valves, Problem c: blockage of sealant system – Flowserve Nordstrom Dynamic Balance Plug Valve and Double DB Plug Valve User Manual
Page 19
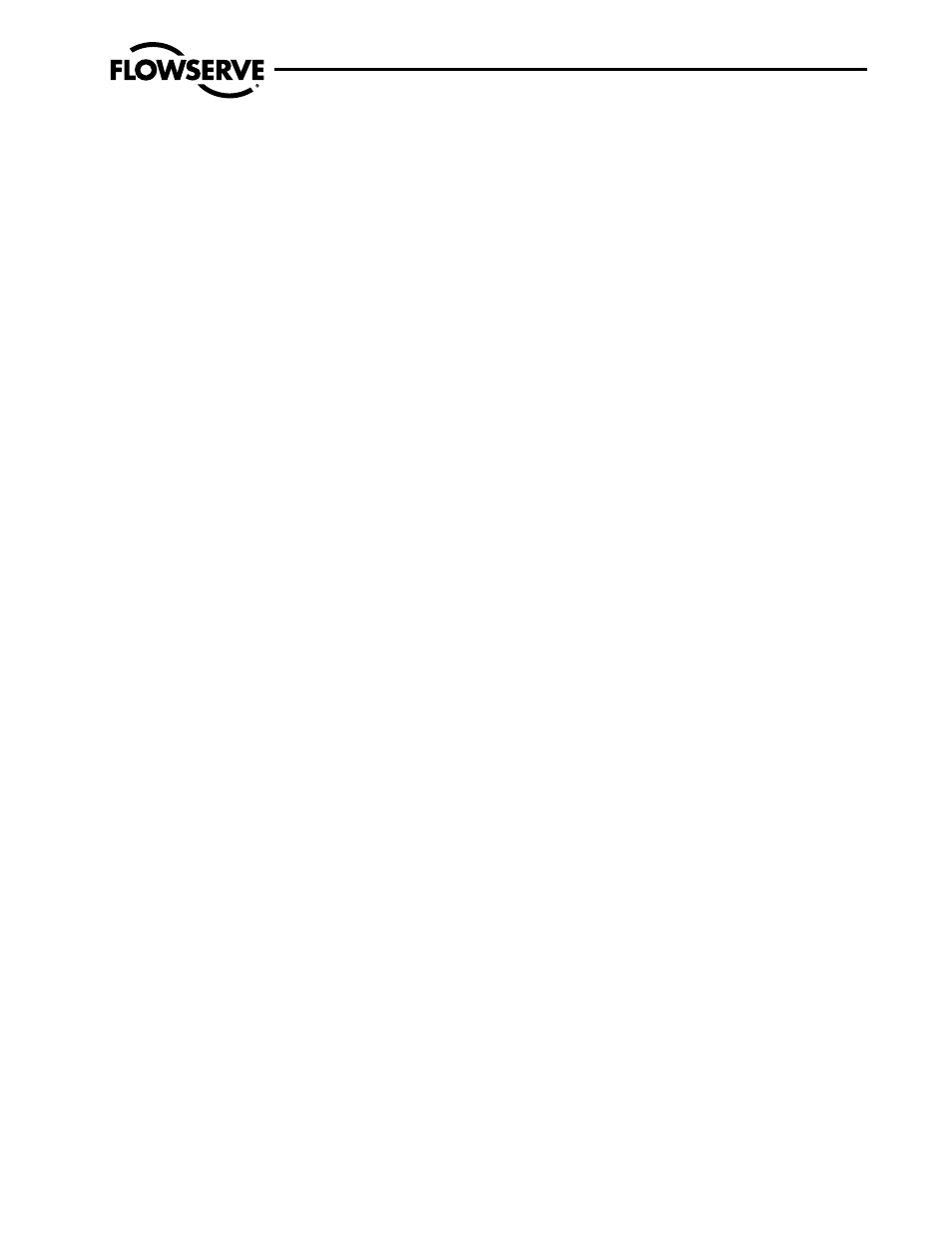
Flow Control
Nordstrom Valves
FCD NVENIM2005-01
Dynamic Balance
®
Plug Valve and Double DB
®
Double Isolation Plug Valve
19
Cause B4: Severe Stem corrosion (wrench-operated valves)
Solution B4
Remove corrosion from the Stem and interior surface of the Gland
or Gland Retainer (gear-operated valves).
1. Remove the Retaining Ring and Stop Collar.
2. Remove the Weatherseal and inspect it for signs of damage. If
the Weatherseal is damaged, replace it. Check for corrosion on
the Stem or internal surface of the Gland.
3. If there is corrosion, attempt to lubricate the Stem-to-Gland
joint, as described in Operation Difficulties, Cause B3 above. If
this procedure does not work, continue with Step 4 below.
a
CAUTION: Remove line pressure from the valve before
performing the following procedures:
4. Remove the Gland and Gland Bolts.
5. Remove internal corrosion from the Gland by scraping and/or
using a #120 emery cloth.
6. Remove Stem corrosion by scraping and/or using a #120
emery cloth.
7. Remove the liquid gasket from the Gland contact area of
the Body.
8. Clean debris from the top of the Packing and from the Gland
bolt holes.
9. Fill the relief area on the I.D. of the Gland with valve sealant.
10. Apply liquid gasket to the Gland-to-Body mating surface.
11. Replace the Gland.
12. Apply an anti-seize compound to the Gland Cap Screws and
install. Use the bolting torque guidelines, as described on Table
I (Size 4 and Smaller Valve Gland Bolting) or Table 3 (Size 6 and
Larger Valve Pressure Retaining Bolting) in the Technical Data
section.
13. Apply lithium-base grease to the bottom of the Weatherseal
and replace.
14. Replace the Stop Collar and Retaining Ring.
Cause B5: Gearing problems
Solution B5
Check to see if the valve Gearing is causing operational problems.
1. Remove the Indicator.
2. Completely remove the Gearing.
3. Remove the Gear Segment Key.
4. Replace the Gearing less the Segment Key.
5. Rotate the Handwheel to operate the Gearing. If the Gearing is
difficult to operate, the problem is in the Gearing. If the Gearing
is easy to operate, the problem is within the valve.
6. Inspect the Gear Segment and the Worm Gear for excessive
wear, damage, or lack of lubrication.
7. Rotate the Worm Shaft to determine if the Bearings are binding.
8. Replace any parts as necessary and ensure the Gearing operates
properly before reassembling to the valve.
Problem C: Blockage of sealant system
Cause C1: Sealant groove blockage
Solution C1
Some sealant can harden in the valve sealant system if not properly
maintained. Hardened sealant can prevent or reduce the flow of
sealant injected into a valve. To clear the valve sealant system of
hardened sealant, inject VXX Valve Purge.
1. Inject VXX Valve Purge liberally into the valve using sealant
injection equipment. If possible, the valve should be operated
several times during application.
2. Allow the VXX Valve Purge to remain in the valve for an extended
period of time with periodic valve operation.
3. Repeat Steps 1 and 2.
4. Inject an excess amount of the appropriate valve sealant into the
valve.
5. If valve operation is improved by this procedure but the valve is
still not operating properly, repetition of this procedure may be
required.
6. Under conditions of severe sealant deterioration, VXX Valve
Purge may not be capable of dislodging sealant residues, and
valve disassembly and physical cleaning may be required.
Cause C2: Sealant Fitting blockage
Solution C2
In the event that no sealant is being injected into the valve even
though the sealant equipment is pressurized, the Sealant Fitting may
be blocked and should be replaced.
a
CAUTION: The following procedures should be performed
with extreme caution. Make sure the sealant fitting is
pointed away from your body before proceeding. Heavy
leather gloves and safety glasses should be worn during
these procedures.
1. Check for sealant pressure behind the Sealant Fitting by pressing
the center button of the fitting with a small punch or screw-