3 threaded valve to pipe assembly, 4 flanged joint assembly, Nordstrom valves – Flowserve Nordstrom Dynamic Balance Plug Valve and Double DB Plug Valve User Manual
Page 7
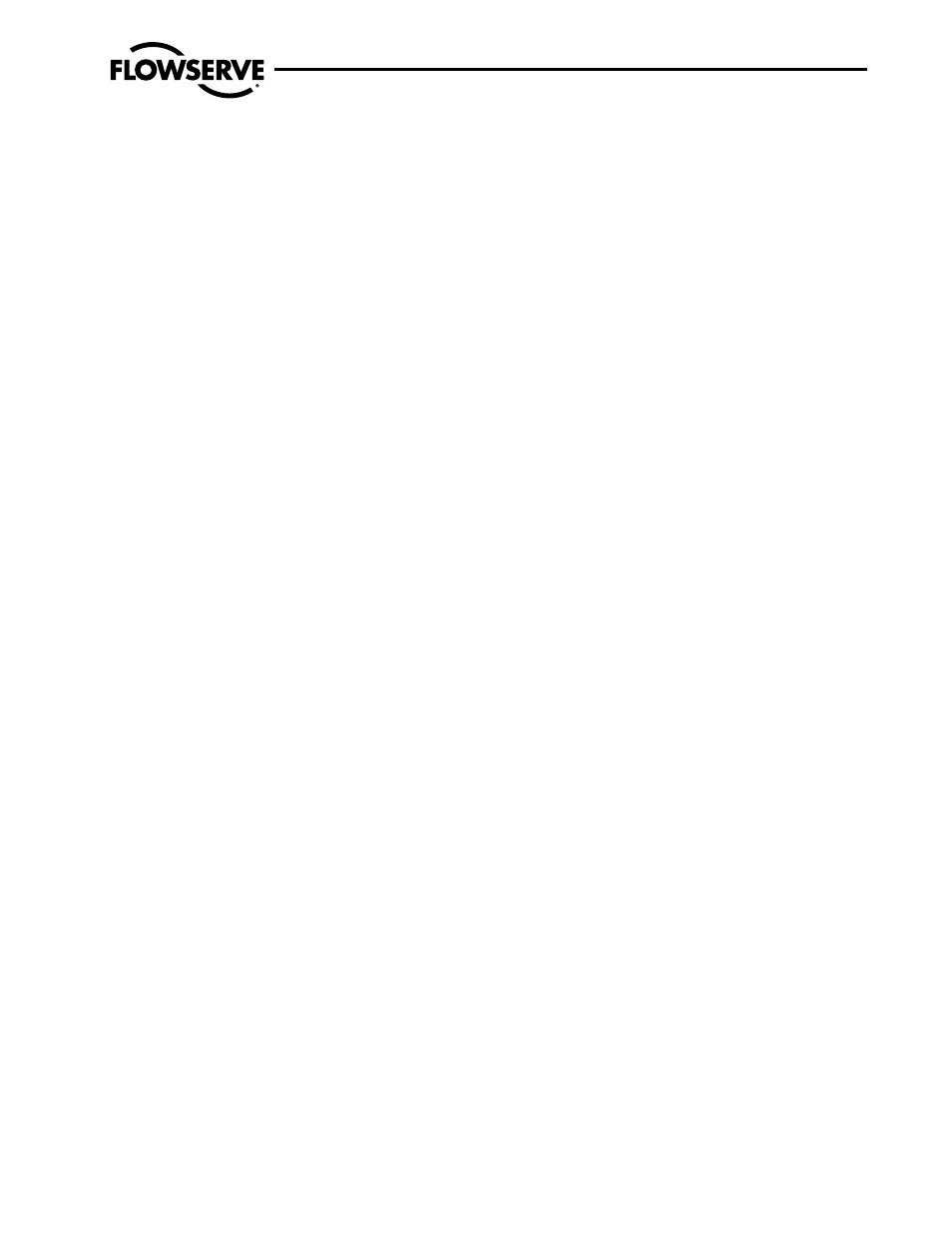
Flow Control
Nordstrom Valves
FCD NVENIM2005-01
Dynamic Balance
®
Plug Valve and Double DB
®
Double Isolation Plug Valve
7
b. Note any special warning tags or plates attached to or accompa-
nying the valve, and take appropriate action.
c. Check the valve for markings indicating flow direction. When a
flow direction is indicated on the valve, make sure that the valve
is installed in the proper flow orientation.
d. Inspect the valve interior (to the extent practical) through the
end ports. Make sure it is reasonably clean, and free from for-
eign matter and harmful corrosion. Remove any special packing
materials.
e. If practical, actuate the valve through an open-close-open or
close-open-close cycle. Inspect significant functional features
such as guides or seat faces that are made accessible by such
actuation.
a
CAUTION: Avoid contact with the valve closure element
during cycling. It is usually desirable to leave the valve
closure member in the position in which it was shipped
following such inspection.
f. Immediately prior to valve installation, check the piping to which
the valve is to be fastened for proper alignment, cleanliness, and
freedom from foreign materials.
3.3 Threaded Valve to Pipe Assembly
Threaded pipe joints depend on a good fit between the external and
internal pipe threads for tight sealing. Usually, a compatible soft or
viscous material is used between the assembled threads to assist
in ensuring a leak-free seal. The following installation practices are
recommended:
a. Check the threads on both the valve and the mating pipe for
correct thread form and cleanliness. Be alert for indication of an
impact that might have deformed the thread either out-of-round
or by a local indentation. Be sure no chips or grit are present.
b. Note the internal length of the threads in the valve ends and the
proximity of the valve internal seat to make sure the pipe end will
not hit the seat when assembled. If there appears to be a pos-
sibility of a problem, carefully check the pipe end thread to make
sure there is no extended straight portion beyond the standard
tapered section.
c. Apply an appropriate thread tape or thread compound to the
external pipe threads except when dry seal threading is speci-
fied. Avoid getting the thread tape or thread compound into the
internal flow area.
d. Use care to align the threads at the point of assembly. Tapered
pipe threads are inherently a loose fit at entry. Substantial
wrenching force should not be applied until it is apparent that
the threads are properly engaged.
e. Assemble the joint wrench-tight. The wrench on the valve should
be on the valve end into which the pipe is being threaded.
a
CAUTION: Because there is no clear limit on the torque
that may be developed in a tapered thread joint, it is
possible to damage the valves or piping by applying
excessive twisting forces through the body of the valve.
If at all possible, put the wrench on the end of the valve
into which the pipe is being threaded.
f. Repeat the process at the second valve end. Again, apply the
back-up wrench at the end of the valve into which the pipe is
being assembled.
3.4 Flanged Joint Assembly
For tight sealing, flanged joints depend on compressive deforma-
tion of the gasket material between the facing flange surfaces. The
bolting must provide the mechanical force necessary to maintain
the compressive stresses on the gasket as well as resist the normal
pressure forces tending to separate the joint. Attempting to align
misaligned flanges with only brute force may not provide sufficient
bolting force to sustain the required gasket loading and to resist the
load caused by the pressure separating force, resulting in a joint
leakage problem. The following practices should therefore be fol-
lowed for satisfactory flange joint make-up:
a. Check the mating flange facings.
a
CAUTION: Do not attempt to assemble the flanges if
a condition is found that might cause leakage (e.g., a
deep radial groove or a dent across the face caused by
mishandling) until the condition is corrected.
b. Check the bolting for proper size, length, and material. A carbon
steel bolt on a high-temperature flange joint can result in early
joint failure.
• High-strength material is always required for flange bolting
on steel flanges Class 400 or higher. Such bolting is usually
stamped “B-7” on the end, but other grades may be used in
some cases. The proper matching of flanges, bolting, and
gaskets is important. Specific requirements of ASME B16.5
should be satisfied.
• Low-strength bolting may be used both for lower pressure
flanges and for Classes 150 and 300 for operating tempera-
tures not exceeding 400°F (204°C) when using approved
gasket materials. See ASME B16.5 for gasket specification.
c. Check the gasket materials. See ASME B16.5 for additional
requirements for flange joints using low-strength bolting (e.g.,
gray iron flanges or Class 150 steel flanges). Metal gaskets (flat,