5 weld joint assembly, 6 proprietary end connection assembly, Nordstrom valves – Flowserve Nordstrom Dynamic Balance Plug Valve and Double DB Plug Valve User Manual
Page 8
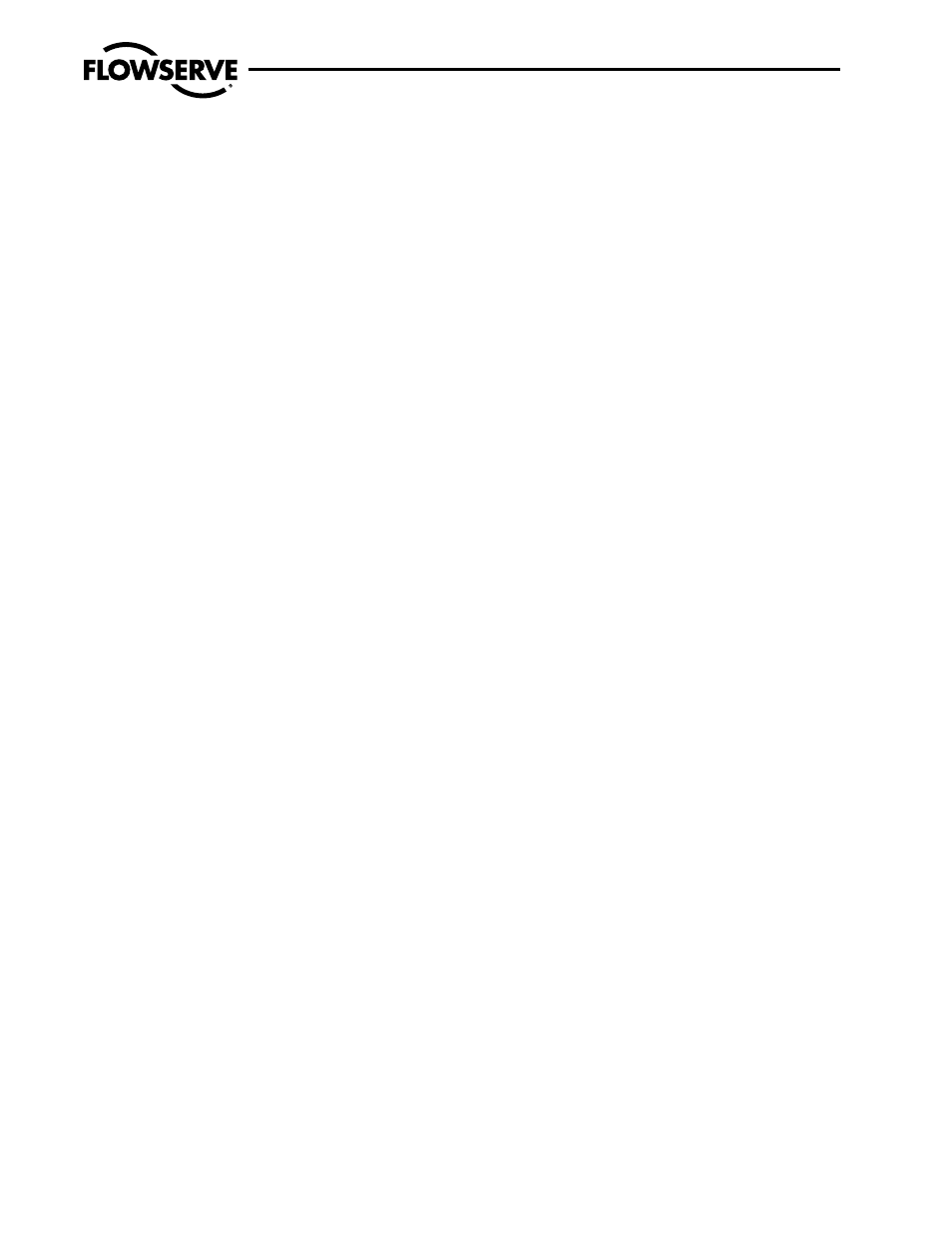
Flow Control
Nordstrom Valves
8
Dynamic Balance
®
Plug Valve and Double DB
®
Double Isolation Plug Valve
FCD NVENIM2005-01
grooved, jacketed, corrugated, or spiral wound) should not be
used with these flanges.
d. Check the gaskets for freedom from injurious defects or
damage.
e. Use care to provide good alignment of the flanges being
assembled. Use suitable lubricants on the bolt threads.
Sequence the bolt tightening to make the initial contact of the
flanges and gaskets as flat and parallel as possible. Tighten
the bolts gradually and uniformly to avoid twisting one flange
relative to the other. Use of a torque wrench is helpful to ensure
correct and uniform final tightening of the flange bolting. Parallel
alignment of flanges is especially important when assembling
a valve into an existing system. If the flanges are not parallel,
then it is necessary to bend something to make the flange joint
tight. Simply forcing the flanges together with the bolting may
bend the pipe or it may bend the valve. This is particularly true
in large-diameter piping. Such conditions should always be
brought to the attention of someone capable of evaluating the
bending condition and the corrective measures that need to be
taken. The assembly of certain short-pattern valves between
mating flanges requires that the installation be checked for any
possibility of interference between the moving parts of the valve
and the adjacent pipe, fitting, or valve.
a
CAUTION: Torque wrenches should always be used to
assure proper tightening of the flange bolting. A bolt is
considered to be yielding when, in the tightening pro-
cess, the torque on that bolt is increasing with each part
turn and then is observed to remain unchanged, or is
increasing a much lesser amount with an additional part
turn. That bolt should be replaced and scrapped, since it
is no longer capable of maintaining the proper preload.
3.5 Weld Joint Assembly
Welded joints that are properly made provide a structural and metal-
lurgical continuity between the pipe and the valve body. It is impor-
tant that the joint should not constitute a notch or weak link in the
pipe-valve-pipe assembly. Therefore, the weld fillet for socket weld
joints must always have more cross-sectional area than the pipe.
Butt weld joints require full penetration welds and a weld thickness
at least equal to that of the pipe. Welding a pipe of a high-strength
alloy to a valve with body material of lower mechanical strength
requires that the weld taper to a compensating greater thickness
at the valve end. An alternative is to have a matching high-strength
“weld-on extension” or “pup” welded to the valve prior to welding in
the line.
Sound welds are obviously important.
a
CAUTION: This guide is not a complete welding instruction.
All welding should be in accordance with all codes and/or
jurisdictional regulations applicable to the construction
of the piping system. The welds must be made following
approved welding procedures and be inspected as required
by all applicable specifications. The following are point-of-
use reminders of important requirements of good welding
practice:
a. Consult the manufacturer for the correct installation proce-
dure of a metal-seated valve prior to preheating, welding, and
postweld heat treatment of butt weld and socket weld valves. To
avoid the possibility of arcing, always attach the ground directly
to the body.
b. Consult the manufacturer for the correct installation procedure
before welding a soft-seated valve into a line. As a minimum, a
soft-seated ball or plug valve should be in the full-open position
prior to welding to prevent seat damage and/or weld splatter
from adhering to the ball or plug. A means for venting the ball
cavity is recommended to relieve fluid pressure that might
develop due to thermal effects.
c. Check materials for marking on the pipe and valve to confirm
that they are as specified.
d. Inspect the welding end surfaces for dimensions and cleanli-
ness. Correct any condition that might interfere with assembly
and satisfactory welding.
e. Check all backing rings that may be used to confirm that the ring
material is compatible with the pipe and valve materials and that
the individual rings fit and are clean.
f. Determine that all required welding parameters, including pre-
heating and post-weld heat treating, are in accordance with the
approved welding procedure.
g. Inspect the valve-to-pipe end alignment and adjust as required.
h. Securely tack weld the mating parts when required if it is part of
the approved procedure.
i. Complete the weld using the approved welding procedure.
j. Clean and inspect the finished weld.
k. Repair any defects using an approved weld repair procedure.
3.6 Proprietary End Connection Assembly
For proprietary end connections, such as clamp or compression end
connections, follow the connection manufacturer’s recommenda-
tions for installation.