Troubleshooting – Flowserve L75 Series Electric Actuator User Manual
Page 15
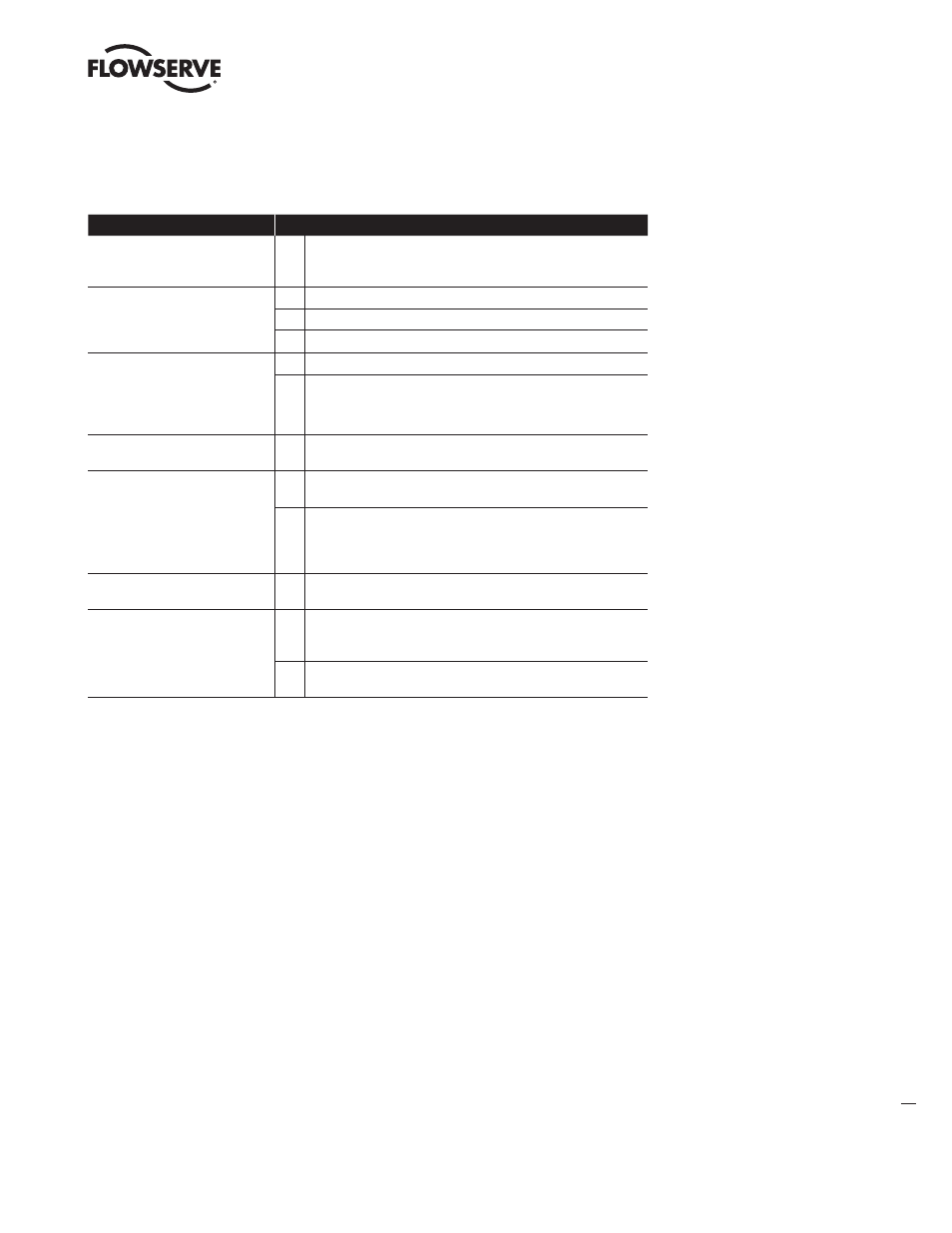
15
L75 Series Electric Actuator — Modbus RTU FCD LMAIM7502-00 – 07/05
flowserve.com
Troubleshooting
The following troubleshooting guide is given to help determine causes of some common problems.
Symptom
Things to Check
When power is applied, all three
indicator LEDs blink and the
actuator will not operate properly.
1
The Modbus address is not correctly entered on the address
switches. Refer to Modbus Address Selection section to correct the
problem.
Actuator does not respond to
any Modbus commands. The
COMM LED does NOT blink when
commands are sent.
1
Be sure power is applied to the actuator.
2
Be sure the Modbus baud rate and wire configuration is correctly set.
3
Check that communications wires are correctly connected.
Actuator does not respond to any
Modbus commands. The COMM
LED blinks when commands are
sent. No exception response is
received.
1
Check that the message is sent to the address of the actuator.
2
Ensure data cables are not located near sources of noise. Use
shielded, twisted-pair cable if possible.
The COMM LED blinks even when a
Modbus command is not sent.
1
Ensure data cables are not located near sources of noise. Use
shielded, twisted-pair cable if possible.
The actuator accepts Modbus
commands, but does not move in a
specified direction.
1
Check the actuator wiring to the motors. Check for loose or broken
wires.
2
If wiring appears intact, check the LED for the direction specified.
If it is ON after the command is issued, either the motor wire is
disconnected, or the actuator board needs replacing. If the LED is
OFF, replace the actuator board.
The actuator responds with an
exception response.
1
Read the error code received and determine the problem using the
Exception Responses table.
After a movement command is sent,
the valve moves but a subsequent
status read does not indicate the
valve in the desired position.
1
The valve may not be done moving when the read status command
is issued. Delay before reading the status to give the valve time to
move.
2
Ensure the limit switches are correctly set for the end-of-travel. See
the Installation Manual for details.