Worcester actuation systems – Flowserve RT92 Series User Manual
Page 5
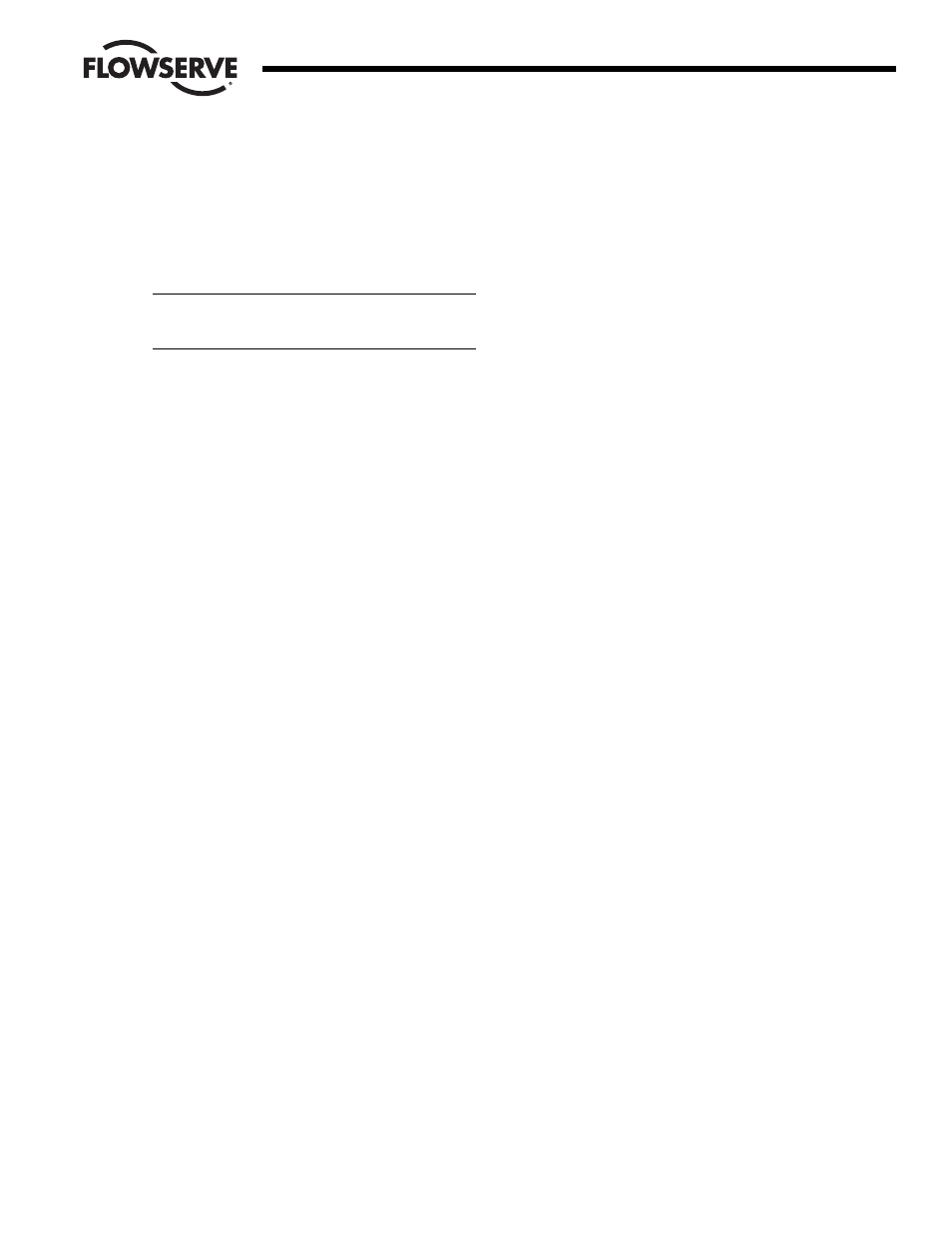
5
3. Adjusting Potentiometer: (Reference Figure 4)
a. Place the large face gear (item 12) over the actuator shaft
with the gear teeth down and secure with snap ring (item
13) provided.
NOTE:
The face gear utilizes a friction fit to the shaft. For
best results, wipe off any lubricant that may be on the shaft
before sliding on the face gear.
CAUTION: Do not overstretch the snap ring, use the
minimum opening to allow snap ring to slip over the
gear.
b. Adjust the potentiometer spur gear until there is
approximately
1
/
16
" engagement with the large face gear.
Tighten the spur gear set screw.
c. Rotate the face gear back and forth to ensure smooth and
easy operation of the potentiometer.
d. For units with 0-5 volt position output calibrate the
potentiometer per paragraph IV.B.3.f.
e. For units with resistive position indication, calibrate the
potentiometer as follows:
i. Position the actuator shaft in the full clockwise
position if it is not already there.
ii. With power off and using an ohmmeter, measure the
resistance between the purple and the white/black
leads from the potentiometer. The measured
resistance should be 80 ohms plus or minus 10
ohms. Rotate the large face gear to achieve this
resistance. Note: It is not necessary to loosen or
remove face gear snap ring to rotate gear.
f. For units with 0-5 volt position output calibrate the
potentiometer as follows:
i. Connect 12 VDC power to terminals 1 and 2. Terminal
1 is common or negative and terminal two is positive.
ii. Connect a digital voltmeter to terminals 1 and 10, with
the negative lead to terminal 1 and the positive lead to
terminal 10.
iii. Set the voltmeter to a full scale reading of at least 5
volts.
iv. Turn the 5 volt adjust pot on the RTU card to the mid-
position. With the switches on the RTU card, run the
actuator in the CW direction until the closed limit
switch trips. This should be the full closed position. If
not, readjust the closed limit switch cam until the
actuator stops in the proper position.
v.
Rotate the large face gear on the actuator shaft until a
positive voltage reading is observed on the voltmeter.
Now slowly rotate the face gear to reduce the voltage
reading towards zero volts. The lowest reading you
will probably observe is .02 to .03 volts. Stop rotating
the gear as soon as the voltage stops dropping. This
adjustment is important. You may want to move the
face gear back and forth several times to get the feel
for the proper adjustment.
vi. Once this adjustment has been made satisfactorily,
use the switches on the RTU card to run the actuator
to the full CCW position. If necessary, readjust the
CCW limit switch cam to achieve the proper full open
position. Now adjust the 5 volt adjust pot on the RTU
card to read 5 volts on the voltmeter.
vii. This completes the calibration of the 0-5 volt position
indication output. However, you may want to operate
the actuator full open and closed several times to
verify proper adjustment of the position indication
output. Disconnect the voltmeter from terminals 1
and 10.
IMPORTANT:
The feedback potentiometer is calibrated
for only one 90° quadrant of valve operation. If the
output shaft is repositioned to another 90° quadrant
or if the output shaft is rotated a multiple of 360°
from its original position the feedback potentiometer
will no longer be in calibration and must be
recalibrated as directed in section IV.B.3.
4. Dual
Potentiometer:
a. In the case of a dual potentiometer, D75, “A” (front, close
to the potentiometer bracket) potentiometer wires are
wired as stated in IV.B.2. “B” (rear, far from the bracket)
potentiometer wires must be wired directly to external
instrumentation.
NOTE:
Voltage limit of “B” pot is 30 volts maximum.
C. Mounting Circuit Board
1. For 12 or 24 VDC 10-23 Size Electric Actuators:
(See Figures 5 and 6).
a. Pre-tap circuit board bracket holes with the self-tapping
circuit board mounting screws (item 5). Remove the
outside corner motor screws and mount the brackets to
the appropriate spacers using the self-tapping
spacer/bracket mounting screws (item 8) being careful to
avoid stripping the threaded holes in motor base. The
longer bracket is mounted to the right side of the actuator
when facing the terminal strip.
NOTE:
For actuators with single motor, be sure that
shorter spacers are used on side with motor.
b. Once these screws and brackets are firmly secured, firmly
tap the motor stators with a plastic faced hammer to
force realignment of the motor bearings.
c. Loosen all terminal strip screws and install the A and B
connector cable assemblies into the actuator terminal
strip. See figure 6 (next page) for proper wiring of cable
assemblies to terminal strip. Wire routing is important.
Ensure that wiring is not pinched and is not touching any
moving parts such as cams or switch arms.
Flow Control
Worcester Actuation Systems