Worcester actuation systems – Flowserve DFC17 User Manual
Page 16
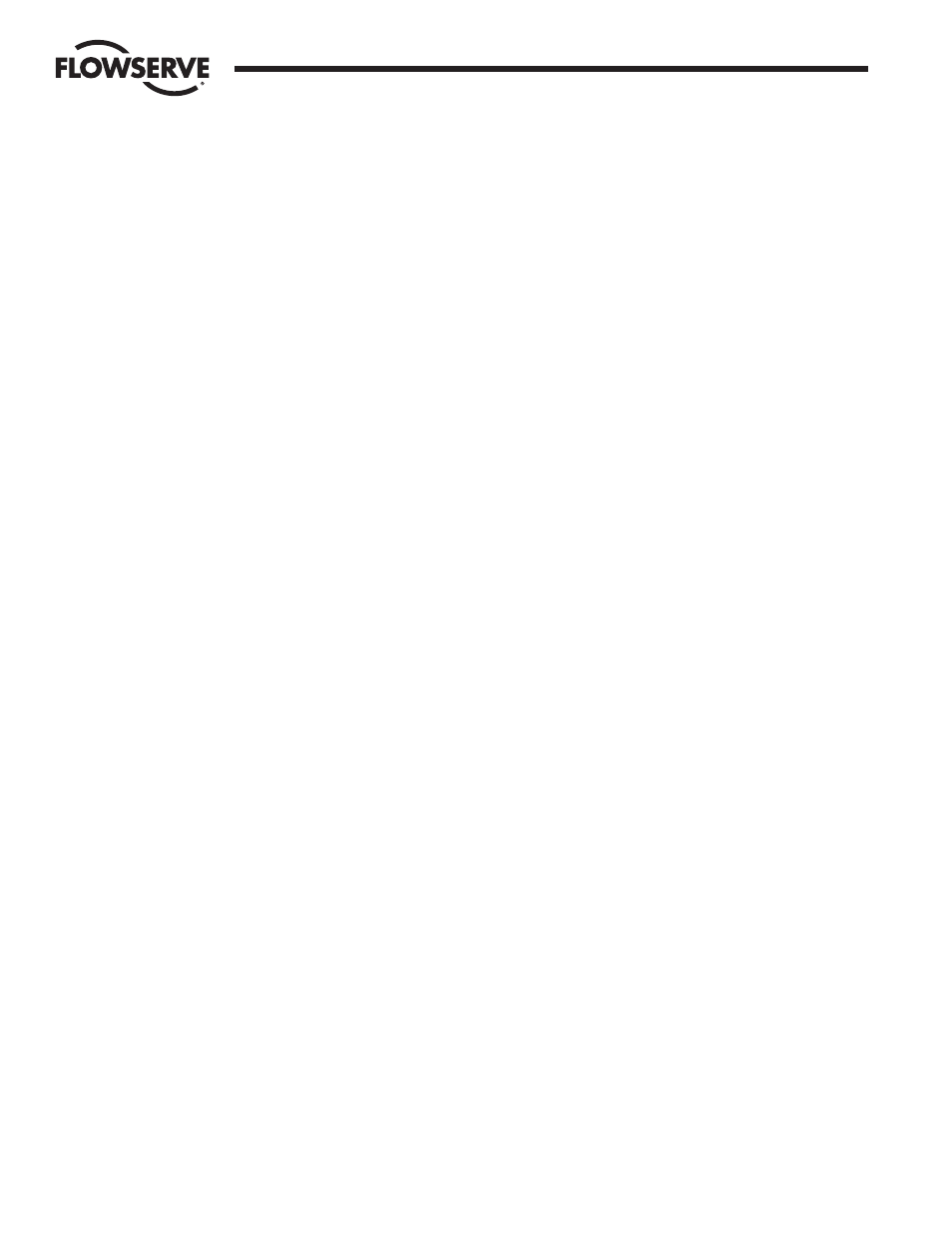
16
DataFlo Digital Electronic Controller DFC17 Installation, Operation and Maintenance Instructions
WCAIM2026
4.2.9 Key Sequences for Calibration of Optional Two-Channel
RTD Process Module
A. Key Sequences for Calibrating Two-Channel RTD
Process #1 Input Signal
This procedure is followed only if a two channel RTD
process module is used. This step calibrates both the
lower and upper process signals for input #1.
Press DN to select the lower input parameter PrlL
Press SEL + UP to begin calibrating the parameter.
1) Attach a calibrated RTD simulator to process
input #1.
2) Select an RTD resistance that corresponds to
-100°C. The voltage corresponding to the
resistance is shown on the display as “X.XX”.
3) Press the UP switch to record the lower
temperature value.
4) Select an RTD resistance that corresponds to
+350°C. The display will show a differential
voltage as “dX.XX”. The d indicates that the
displayed value is the difference between the
actual current voltage and the recorded lower
temperature voltage.
5) Adjust the span potentiometer for a differential
voltage reading of “d4.60” volts.
6) Repeat steps 2) through 5) until the voltage
difference reads “d4.60” without further
adjustments.
Press SEL to accept the value shown and return
to the calibration menu.
B. Key Sequences for Calibrating Two-Channel RTD
Process #2 Input Signal
This procedure is followed only if a two channel RTD
process module is used. This step calibrates both the
lower and upper process signals for input #2. Follow
this step only if an RTD is connected to the process
#2 input.
Press DN to select the lower input parameter Pr2L.
Press SEL + UP to begin calibrating the parameter.
1) Attach a calibrated RTD simulator to process
input #2.
2) Select an RTD resistance that corresponds to
-100°C. The voltage corresponding to the
resistance is shown on the display as “X.XX”.
3) Press the UP switch to record the lower
temperature value.
4) Select an RTD resistance that corresponds to
+350°C. The display will show a differential
voltage as “dX.XX”. The d indicates that the
displayed value is the difference between the
actual current voltage and the recorded lower
temperature voltage.
5) Adjust the span potentiometer for a differential
voltage reading of “d4.60” volts.
6) Repeat steps 2) through 5) until the voltage
difference reads “d4.60” without further
adjustments.
Press SEL to accept the value shown and return
to the calibration menu.
4.2.10 Key Sequence for Calibrating Thermocouple Process
Module
With this type of process module, an attached
thermocouple develops a voltage representing the
temperature of the process. Thermocouples can cover a
very wide temperature range. The thermocouple module
however allows a narrower temperature range to be used.
This is useful for applications that need higher resolution
and do not need a wide range.
The purpose of this procedure is to specify the
thermocouple type, temperature units, temperature range,
and to record the actual voltage values at the lower and
upper process limits. This procedure involves adjusting
components on the thermocouple module. This procedure
is entered by selecting either the Pr1L or Pr1U parameter
for calibration. When either of those parameters is
selected for calibration, the controller starts the following
calibration sequence. At any time in the menu, the user
can press the SEL key to return to the calibration menu.
Note: For greatest accuracy, the thermocouple simulator
should be connected to the controller input module, and
the simulator and the controller board should be turned
on and allowed to temperature stabilize for at least 15
minutes prior to calibrating. The minimum allowable
temperature span is 100°C (212°F).
Any one step in the calibration procedure can be
performed without performing the others. However, it is
recommended to perform all the calibration steps if any
one item is changed.
Calibrating the thermocouple module circuitry involves
adjusting the gain potentiometer on the module to
achieve the desired temperature range. When
adjustments have been properly completed, the
calibration routine will use the calibrated analog voltages
to create a linearization table.
The table below shows a calibration step and the
procedure required to complete the step. It is
recommended to perform all the calibration steps if any
one item is changed.
Press the DN key until the Pr1L parameter appears. On
that display, press the SEL and UP keys simultaneously to
enter the thermocouple calibration menus.
Flow Control Division
Worcester Actuation Systems