Worcester actuation systems – Flowserve DFC17 User Manual
Page 21
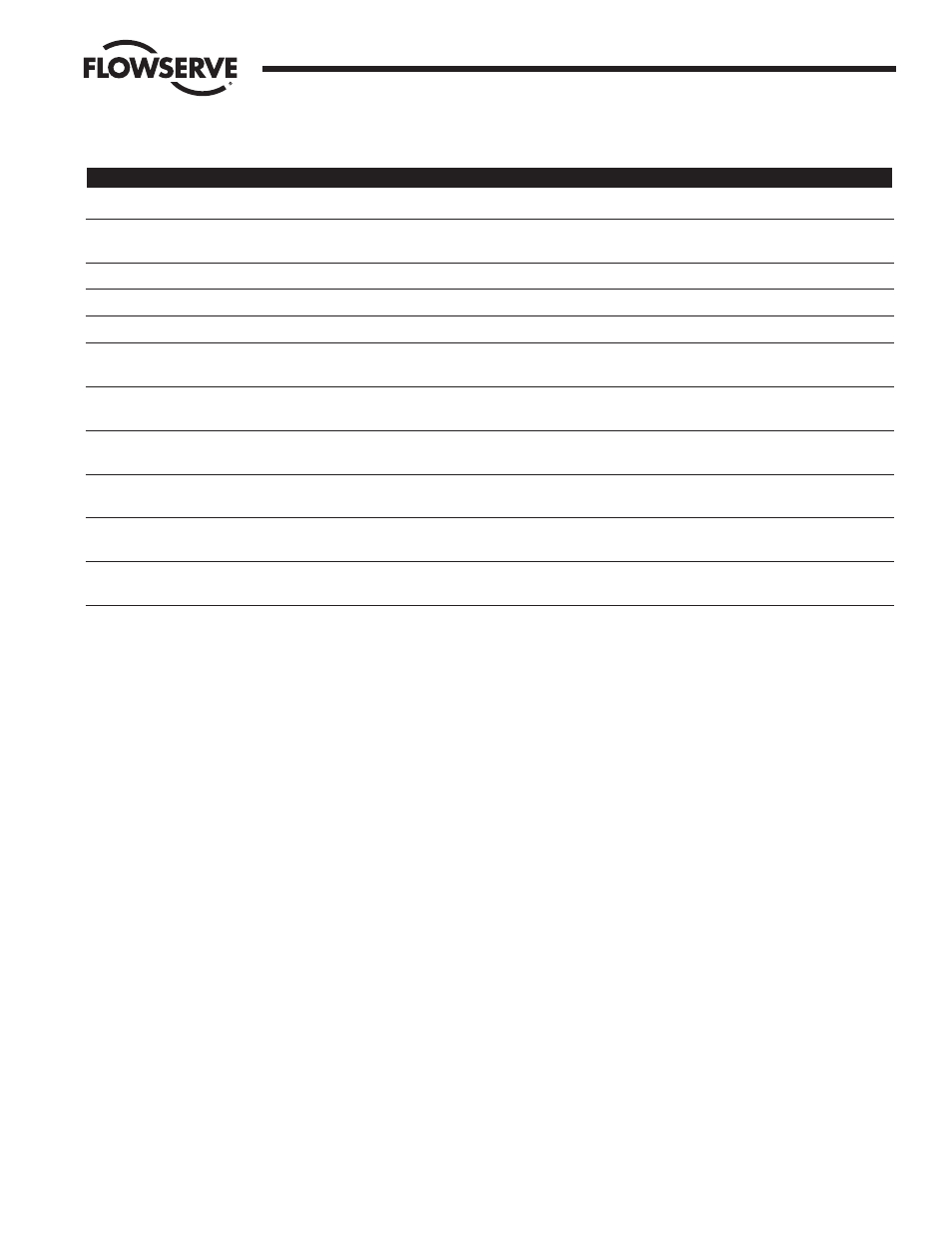
WCAIM2026
DataFlo Digital Electronic Controller DFC17 Installation, Operation and Maintenance Instructions
21
Flow Control Division
Worcester Actuation Systems
Setting Position
Press UP or DN to rotate the controller shaft either counter-
clockwise or clockwise respectively. The shaft will continue to
move as long as the key is held down and a limit switch has not
tripped.
During the Manual Position Mode, a host controller connected
on the serial data link has no control of either the setpoint or the
actuator/valve position. Also in this mode, the setpoint input is
ignored.
Auto-Tuning
Press SEL + DN to enter the Auto Tune mode. The display will
show Atun for three seconds. At this and at any point in the auto-
tuning procedure, the user can press the SEL key for three
seconds to exit auto-tuning and return to the Manual Position
Mode.
4.6 Positioner Mode
The controller has a unique feature, which allows the application
of a 24 VDC signal to the controller board to switch it to a basic
positioner mode. The board then uses the analog 4–20 mA
setpoint signal as the positioning signal. When the 24 VDC signal
is removed, the board switches back to the controller mode. The
24 VDC signal connects to circuit board terminals TB2–5
(positive) and TB2–6 (negative).
4.7 Auto-Tuning Safety Considerations
4.7.1 Things to Know Before Tuning
Know how fast and how much the process value
changes with a valve position change. The relationship
should be graphed.
Determine the valve safe operating range. This can be
determined from the step above. This range should
provide an adequate change to the process, but should
also not allow dangerous situations to occur. The safe
operating range should be considered when setting the
percentage offset term in Auto-Tuning.
The names for the lower and upper position limits
respectively are: yA and yE
If necessary, to ensure safe operation of the controller, set
shaft position limits using yA and yE.
4.7.2 Safety Concerns During Operation
Determine what should happen in the event of a loss of
either the process signal or the setpoint signal.
Program the Invalid Reading Action parameter
correspondingly. That parameter defaults to an action of
NONE which means that if it is not changed, no action will
be taken (control will attempt to be maintained) if an
invalid setpoint or process signal is received.
The name for the Invalid Reading Action parameter is:
FPOS
Auto Tune Menu
Display
Description
Min Value
Max Value
StEP
The amount of valve position step change desired when running Auto-Tune.
1%
40%
Flct
The amount of fluctuation in the signal value while it is monitored
for 60 seconds.
StP 1
The elapsed time since StP1 was started.
30 minutes
StP2
The elapsed time since StP2 was started.
30 minutes
StP3
The elapsed time since StP3 was started.
30 minutes
PtEr
The value of the suggested Proportional Term calculated by the
Auto-Tune Algorithm.
0000
9999
ltEr
The value of the suggested Integral Term calculated by the
Auto-Tune Algorithm.
000
999
dtEr
The value of the suggested Derivative Term calculated by the
Auto-Tune Algorithm.
0000
8000
CyCt
The value of the suggested Cycle Interval calculated by the
Auto-Tune Algorithm.
1.0 second
999.9 seconds
ALr
Any alarm except the setpoint alarm will cause Auto-Tune to halt and
the actuator shaft will return to its original position.
Erto
A 30 minute timeout error will cause Auto-Tune to abort and the
actuator shaft to return to original position.