Test procedure – Flowserve Supplement 2 75 DeviceNet PLC User Manual
Page 2
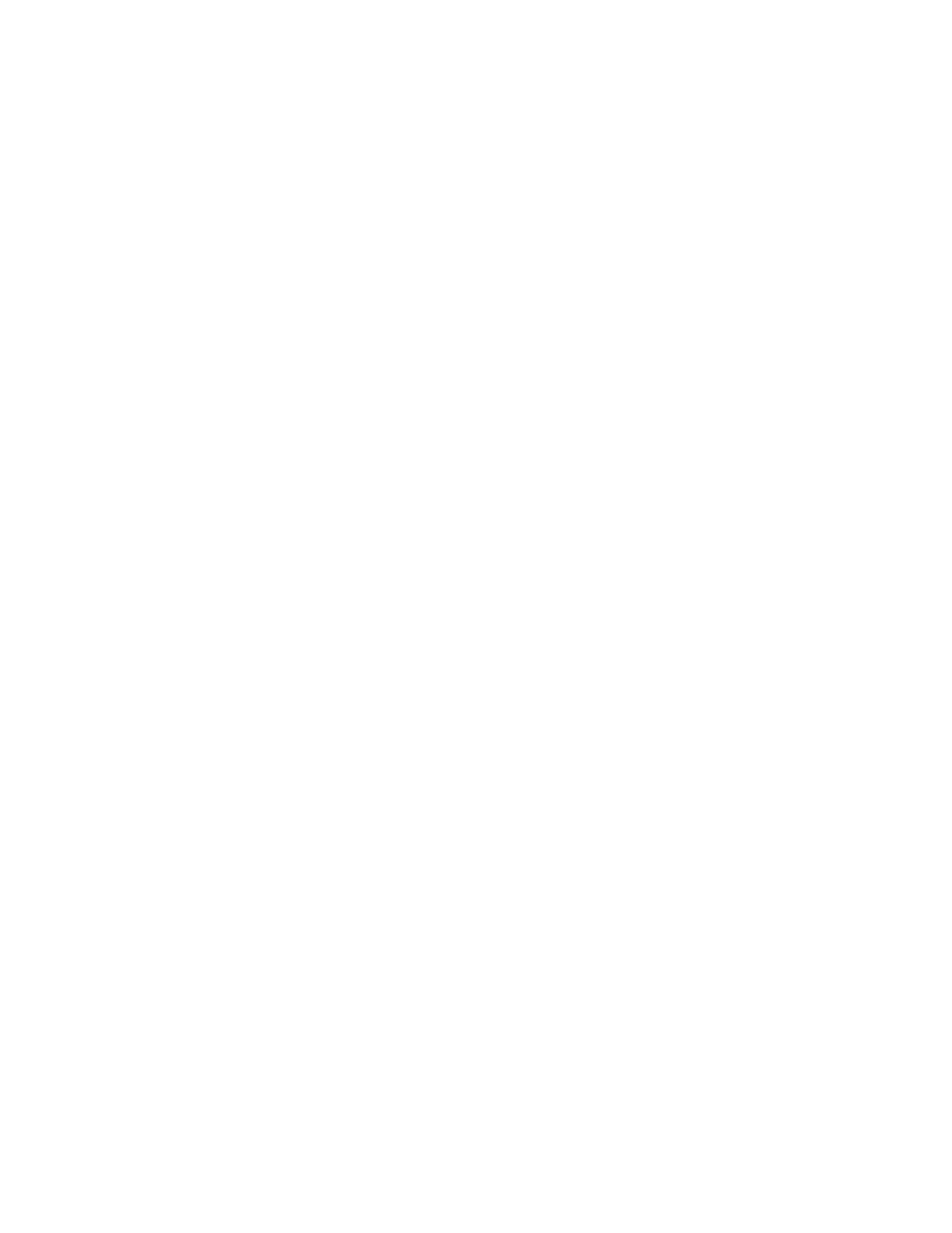
2
Supplement 2: 75 DeviceNet PLC
FCD WCAIM2062-00
Test Procedure
1. Installing Electronic Data Sheet (.EDS) File
Install the .EDS file (disk supplied with actuator) from the disk
to the Rockwell .eds folder found on the hard drive as follows:
Rockwell Software \ RS COMMON \ EDS
With the .EDS file placed as above, the RS Networx program
wiII automatically load the ACCESS .EDS file parameters when
a network browse is performed. The .EDS file-access actuator
(07159) can be found in the vendor category when running RS
Networx.
2. Connect the SLC Processor to the PC-COM-1 Port and the KF2
module to PC-COM-2 port.
3. On the Actuator DeviceNet Board
a) Set Switch 1 and 2 to the desired address, i.e., for Address
1 set Switch 1 to 1 and Switch 2 to 0. It is important that
the address is set correctly prior to turning 24 VDC power
on to the network. If the address is changed and power is
cycled, LED2 will flash to indicate that the current network
does not agree with what had previously been loaded to the
master/scanner.
b) Set Switch 3 to the desired communication Baud Rate, i.e.,
Position O = 125K Baud Rate.
4. With the equipment installed and connected, and with power
turned on to the SLC and 24 VDC turned on to the DeviceNet
Network, LED1 should be steady and LED2 will be flashing
green until this node has been mapped into the PLC Master/
Scanner.
A red LED-D2 indicates that there is an address conflict. See
step 13.
5. Using RS-LINX Configure Drivers
PC-COM-1 Port- to SLC- DF1-l-DH485 To be running
PC- COM-2 Port- to KFD-1 To be running
6. Using RS-Networx: Configure network, should consist of scan-
ner at node-00; actuator 07159(1) at node-01; KFD module at
node-62.
7. Go online with the Network and upload the slave parameters to
the scanner module.
8. Double click the scanner module and select “module” and
upload scanner parameters.
9. At the scanner module screen, select “module” and set the slot
number to the value that the scanner module resides in, i.e., the
scanner was installed in slot #4 in this example.
10. At the scanner module screen, select “scanlist” and highlight
-01,07159(1) (which is the 75 actuator module) in the left
window. Using the right arrow move the device into the right
window.
11. At the scanner module screen, select “input.” The display will
show the default mapped location of the 11 bytes of slave (01)
75 actuator output (produced) data.
Output data from slaves is input data to the scanner. The
default mapped address of 11 bytes of input data starts at
1:4.1 through 1:4.6 (1st byte). Note that the “4” represents the
scanner slot number.
12. At the scanner module screen, select “output.” The display will
show the default mapped location of the 1 byte of slave (01) 75
actuator input (consumed) data.
Input data to the slaves is output data from the scanner. The
default mapped address of 1 byte of output data starts at word
O:4.1 (1st byte).
The input/output data can be remapped at these screens, which
is beyond the scope of this example. It is important to note that
whenever any slaves are added or removed, or, remapping has
been performed, the “apply” button has to be activated with the
processor in the program mode to download the changes to the
scanner.
13. A red LED-D2 indicates that there is an address conflict. A Slave
on the network already has been assigned this address.
To correct this problem, assign and set switches 1 and 2 to an
unused address for this node and cycle the 24 VDC BUS power.
Perform a new Network Browse and go on-line, and upload the
network to the scanner. Select the correct scanner “slot.” In
the “scanlist” delete the slave(s) that have been removed from
the network and add the new slave(s) to the network. Put the
processor in the Program mode and select “apply.” Download
the new data to the scanner. When this is complete both LEDs
D1 and D2 should be on steady green.