Installation, Worcester controls – Flowserve Electri-SAFE DataFlo Digital Electronic Positioner User Manual
Page 2
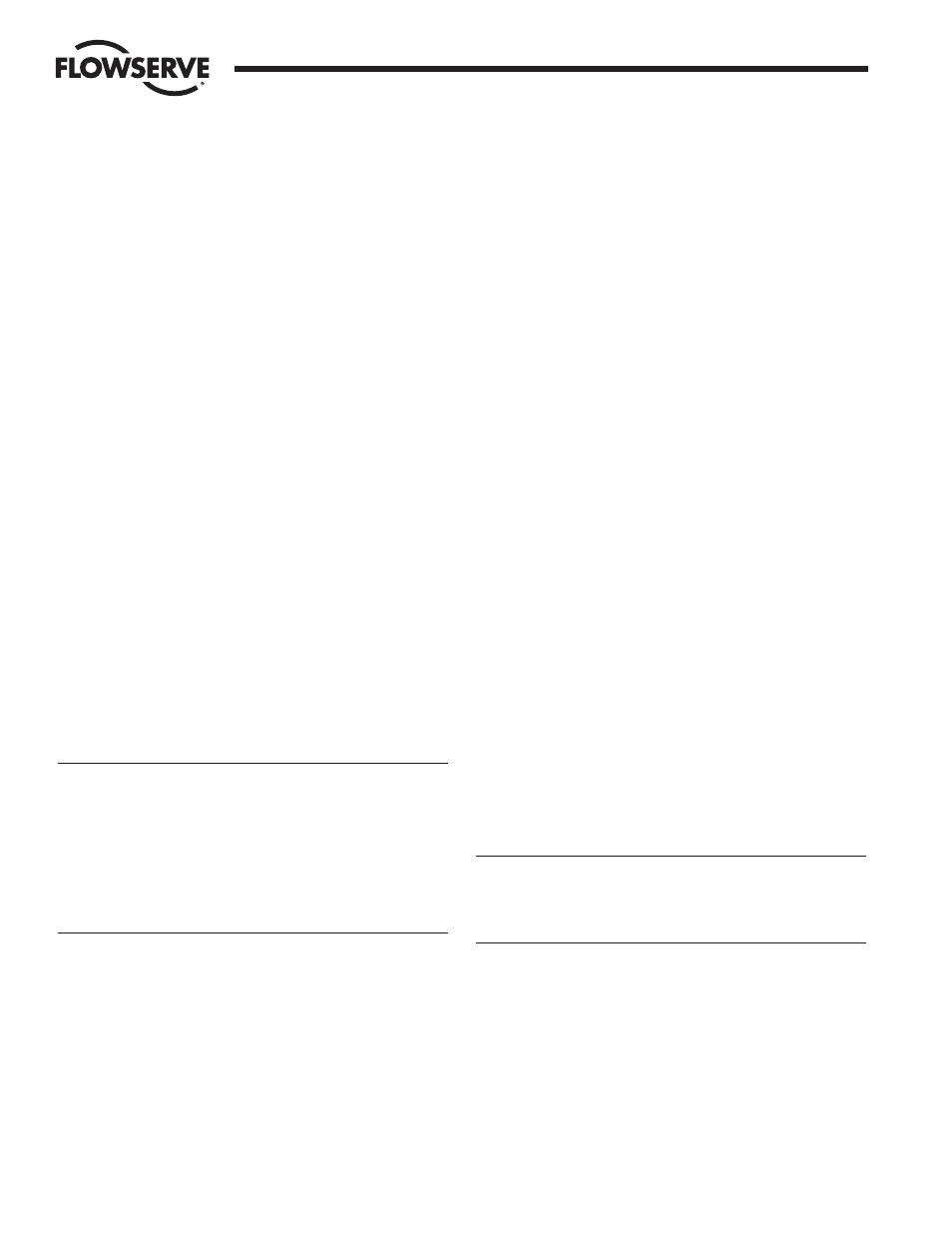
2
Electri-SAFE DataFlo Digital Electronic Positioner
WCAIM2025
Flow Control Division
Worcester Controls
The Worcester/McCANNA DataFlo Digital Electronic Positioner is rated
for operation between -40°F (with heater and thermostat) and 150°F.
Humidity
Most electronic equipment has a reasonable degree of inherent
humidity protection and additional protection is supplied by the
manufacturer, in the form of moisture-proofing and fungicide
coatings.
Such protection, and the 3 to 4 watts of heat generated by the circuit
board assembly, will generally suffice for environments where the
average relative humidity is in the area of 80% or less and ambient
temperatures are in the order of 70°F average. Where relative
humidity is consistently 80 to 90% and the ambient temperature is
subject to large variations, consideration should be given to installing
a heater and thermostat option in the enclosure. The heater should
not increase the enclosure temperature to the point where the circuit
board assembly’s temperature rating of 150°F is exceeded.
In those instances where the internal heater would bring the circuit
board’s operating temperature near or above its maximum rating, the
user might consider purging the enclosure with a cool, dry gas. The
initial costs can usually be paid off quickly in the form of greatly
extended equipment life, low maintenance needs, and much less
process downtime.
Input Circuit Noise Protection
Shielded wiring should be used as conductors for all signal input
circuit wiring regardless of length.
The shields should never be used in place of one of the input wires,
and the shields should be grounded to equipment housings at one
end of the wiring run only. Grounding both ends of shielding can
eliminate the shielding benefits because of current ground loops. If
two or more shielded cables come to the Positioner from different
locations, ground the shields at the Positioner.
a
WARNING: SERIES 72 ACTUATORS ARE ELECTRO-MECHANICAL
DEVICES SUBJECT TO NORMAL WEAR AND TEAR. ACTUATOR LIFE
IS DEPENDENT UPON APPLICATION AND ENVIRONMENTAL
CONDITIONS. IF APPLIED IN HAZARDOUS SERVICES SUCH AS, BUT
NOT LIMITED TO, MEDIA TEMPERATURE EXTREMES, TOXINS,
FLAMMABLE, OR OTHER SERVICES WHERE IMPROPER OR
INCOMPLETE OPERATION COULD PRODUCE A SAFETY HAZARD, IT
IS INCUMBENT UPON THE SYSTEM DESIGNER AND THE USER TO
PROVIDE PROPER WARNING DEVICES SUCH AS TEMPERATURE
SENSORS, OXYGEN SENSORS AND FLOW SENSORS.
INSTALLATION
Mechanical Assembly of Actuator to a Worcester Controls or
McCANNA Valve:
The Series DP 72 actuator assembly is in its full clockwise position
when no electrical power is supplied. Applying electrical power and a
position input signal will cause the actuator to rotate in a
counterclockwise rotation.
The Series DP 72 actuator is a heavy unit. Make sure that the unit and
the valve it is mounted to is supported properly in accordance with
good piping practices. When mounting the actuator to a non-
Worcester/McCANNA valve, please refer to the manufacturer’s
recommendations for installation and operation.
The actuator is normally installed with its major axis parallel to the
pipe line (this is mandatory when mounting actuator to 90° V1
diverter/Three-Way (D44 & T44) valves and CPT valves). The actuator
can be oriented above, beside, or below the valve without affecting its
operation.
Actuators come with an ISO locating ring used for optional ISO
mounting. For mounting to 818/828 Series valves, insert ISO locating
ring into groove on bottom of actuator before attaching to bracket.
Note: Ring can be permanently held in groove by applying Loctite to
ring before inserting in groove.
Determine mode of operation desired (normally open or normally
closed) of the valve.
Determine desired quadrant for bracket attachment and direction of
mounting of actuator (in-line or cross-line).
Fail-Safe Actuators - The normal method of mounting is to have the
actuator in-line with the pipeline and the valve and actuator in the
power off/FAIL-CLOSED position.
For FAIL-OPEN cross-line operation, rotate the valve ball and stem
90°, so coupling lines up with actuator shaft. Mount actuator cross
line to pipe line.
For FAIL-OPEN in-line operation using an in-line coupling, rotate the
valve ball and stem 90°, so coupling lines up with actuator shaft.
Mount actuator in-line with the pipeline.
Attach mounting bracket to actuator using four (4) cap screws and
lockwashers provided in mounting kit. To avoid any damage
to the Series 72 aluminum actuator body, ONLY the proper length
screws supplied with the mounting kit should be used. For small size
top-mount style valves, attach the mounting bracket such that bracket
nameplate will be to the side of the valve.
Attach bracket/actuator assembly to valve as follows:
CAUTION: Ball valves can trap pressurized media in the cavity. If it
is necessary to remove any valve body bolts, stem nuts, or remove
valve from the line, and if the valve is or has been in operation,
make sure there is NO pressure to or in the valve and operate valve
one full cycle.
It is not necessary to remove any valve body bolts or remove valve
from line in order to mount actuator on valve models:
44 (
1
/
4
"-2"), 45 (2
1
/
2
"-4"), 51/52 (
1
/
2
"-4"), 151/301 (3"-4"), 59 (
1
/
4
"-3"),
WK70/WK74 and H71 (
1
/
2
"-2"), 818/828 (2"-3"), 82/83 (
1
/
2
"-3"), 94 (
1
/
2
"-4"):
Rotate valve ball and stem to position necessary to achieve desired
operation. If any valve information is marked on stop plate or handle,
it will be necessary to transfer this information to the bracket
nameplate.