Worcester controls – Flowserve Electri-SAFE DataFlo Digital Electronic Positioner User Manual
Page 4
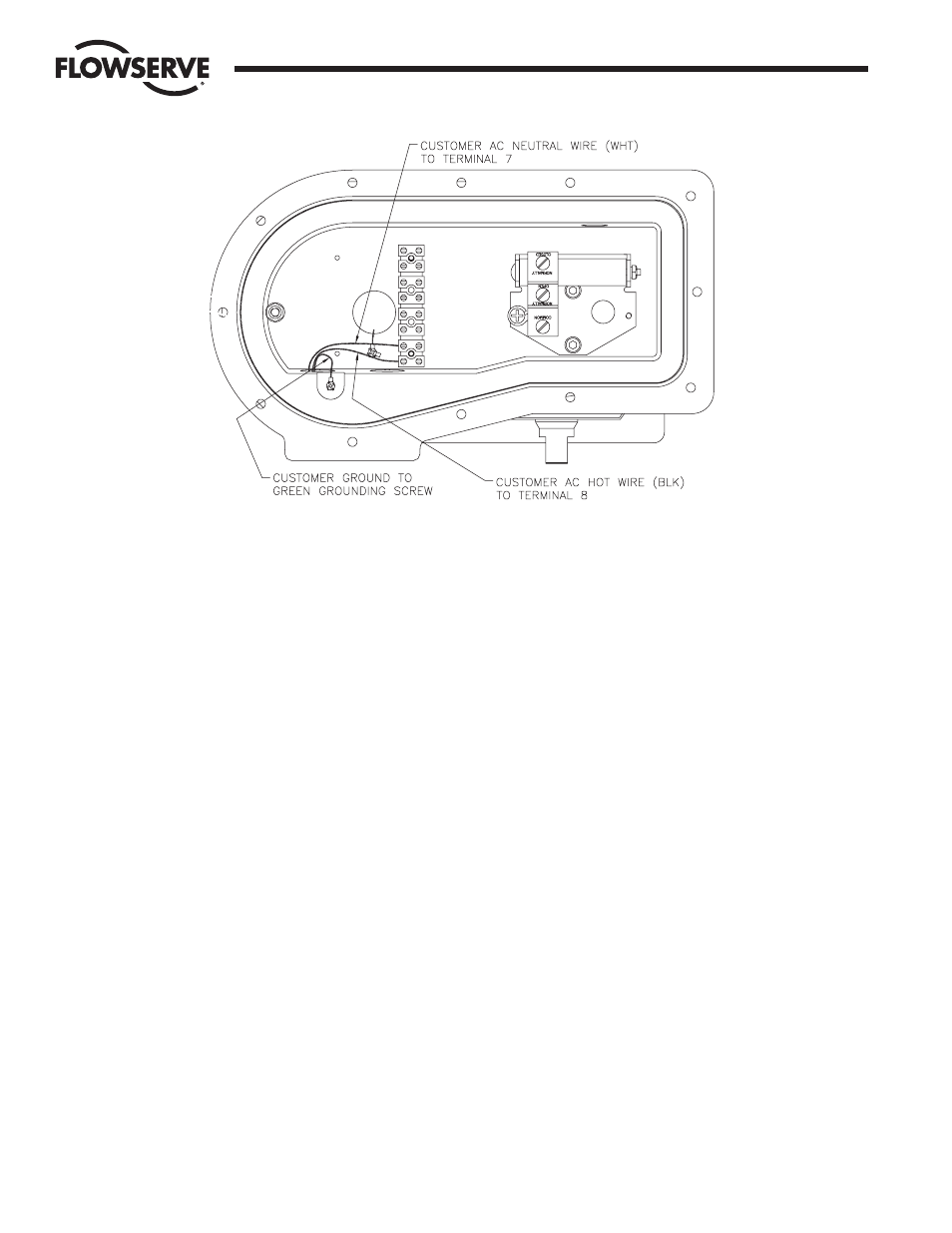
4
Electri-SAFE DataFlo Digital Electronic Positioner
WCAIM2025
Flow Control Division
Worcester Controls
For all Signal Input/Output Connections:
Remove the red plastic conduit connection plug and attach a suitable
conduit pipe to the
3
/
4
" NPT conduit connection to the positioner
housing.
NOTE: Connections and seals are to meet specifications listed in the
“National Electrical Code” Chapter 5 for the environment the actuator
will be installed in.
Loosen the retained housing cover screws and remove the top cover
of the positioner housing.
DP72-1, DP72-4, DP72-10 (milliamp Input Signal for Digital Positioner)
This Positioner is available for use with the standard milliamp signals:
1 to 5, 4 to 20, and 10 to 50 milliamp. The Positioner board is factory
calibrated for one of the three milliamp signal ranges.
Comparison of resistance measurements made at terminals B and C
against the resistances shown below provides a quick way to
determine the milliamp range for which a particular board is
calibrated. If fuse F1 is blown, an open circuit will be indicated.
1 to 5 milliamp models
approximately 1000 ohms
4 to 20 milliamp models
approximately 220 ohms
10 to 50 milliamp models
approximately 100 ohms
Connect the more positive (+) or “High” signal lead to positioner
terminal B. See wiring label on inside of positioner cover, and/or in
appendix of technical reference manual, and/or wiring diagram on
following page.
Connect the less positive (-) or “Common” lead to positioner
terminal C.
Connect one end of the shield wire to the positioner housing. Note
that only one end of the shield wire should be connected to a
grounded housing.
Do not replace the positioner cover until the unit has been calibrated
and the unit is operational. See the paragraph for Calibration and
Adjustment on the next page.
DP72-13, DP72-1K (Potentiometer Input for Digital Positioner)
Potentiometer input circuit boards are made in two versions, one for
low resistance command circuits - DP72-13 135 ohms nominal, and
one for high resistance command circuits - DP72-1K 1000 ohms
nominal.
NOTE: The Input Potentiometer is not the Feedback Potentiometer, but
is an additional Potentiometer provided by and externally located by
the end user.
Connect the signal leads to positioner terminals A, B and C. See
wiring label on inside of positioner cover, and/or in appendix of
technical reference manual, and/or wiring diagram on page 5.
A “Close” command is generated when the potentiometer is rotated to
its full CCW position, and an “Open” command when the
potentiometer is rotated to its full CW position.
If the command signal is derived from other than a rotary pot, it is
only necessary to keep in mind that a “Closed” (full CW) valve is
called for when the command potentiometer presents the least
resistance between terminals B and C and the most resistance
between terminals A and B. A full “Open” (full CCW) valve would be
the reverse condition; the least resistance between terminals A and B
and the most resistance between terminals B and C.
If the Command potentiometer is reasonably linear, the actuator/valve
will be approximately 50% open when the potentiometer shaft is
halfway through its travel and the resistance’s between terminals C to
B and B to A are equal.
If applicable, connect one end of the shield wire to the positioner
housing ground screw. Note that only one end of the shield wire
should be connected to a ground source.