English – Flowserve BAE-ZKE User Manual
Page 9
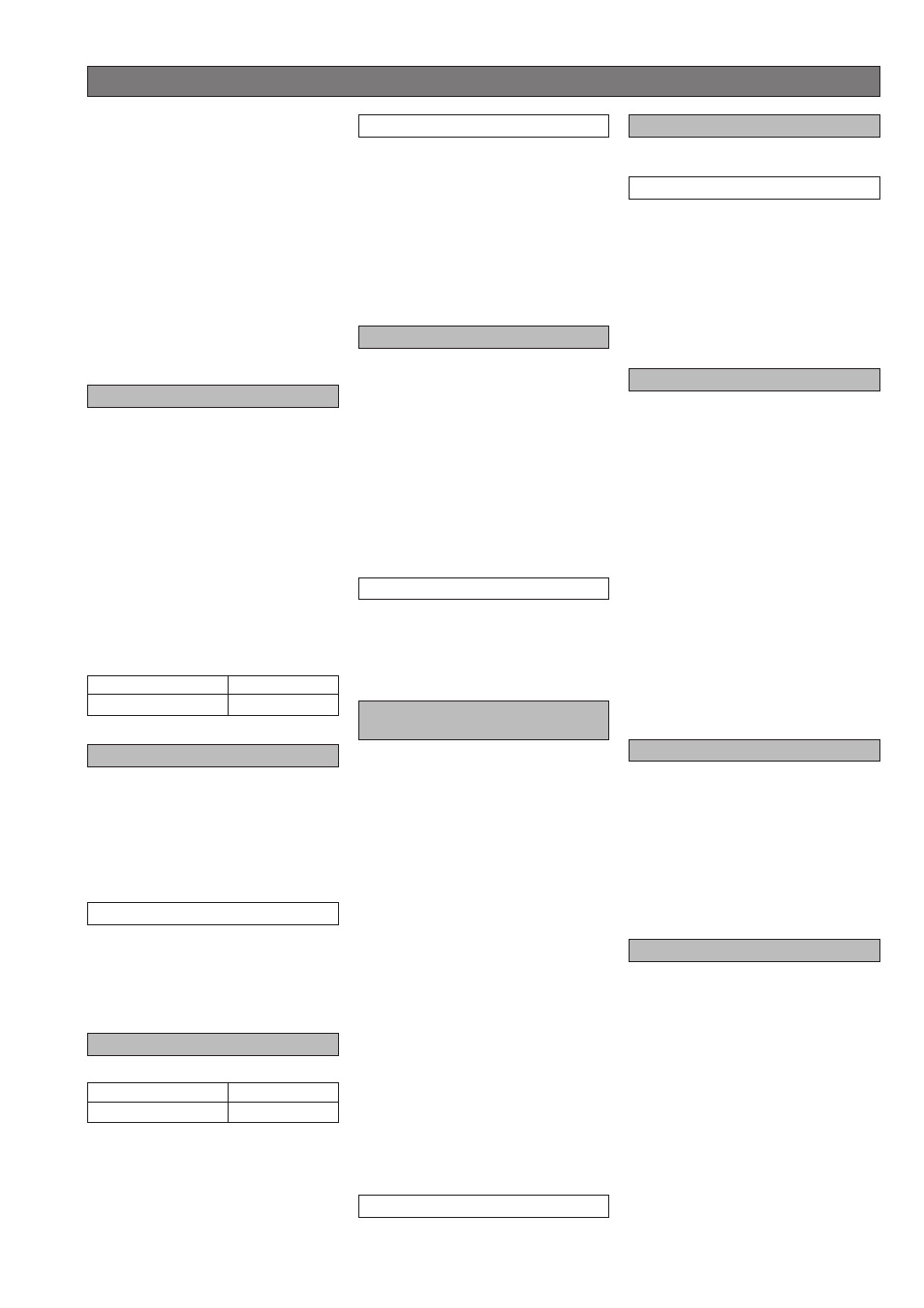
blowdown. Application in steam boilers or
similar plants, in particular plants operated
automatically, e.g. in accordance with the
regulations for operation without constant
supervision (TRD 604).
The boiler water is monitored by a conductivity
electrode. If the set point of the conductivity
value is exceeded the actuator opens the conti-
nuous blowdown valve. If the conductivity falls
again below the set point the actuator moves
the valve back to the LOW (operating) position
ensuring continuous economic blowdown.
On shut-down of the boiler the valve is auto-
matically closed (position CLOSED).
To operate the regulating lever manually, the
actuator can be disengaged.
The equipment consists of the following
components:
●
A
Actuator
●
B
Stage nozzle
●
C
Radial stage nozzle
●
D
Coupling/gear
●
E
Continuous blowdown valve
●
F
Control camshaft
●
G
Screws
●
H
Sample valve
●
I
Stuffing box (self-tightening)
●
J
Angle bracket
●
K
Regulating lever
see
The contiuous blowdown valve is supplied
with the actuator fitted.
BAE 36
The sample valve
●
H
is supplied separately
and has to be screwed into the valve body in
lieu of the lower plug.
The continuous blowdown valve must not be
installed upside down since droplets of water
might get into the actuator; otherwise installa-
tion in any position. Take care of flow direction.
The flow arrow is on the valve body.
Wiring according to wiring diagrams:
For wiring to the potentiometer (terminals
18 - 20) a four-core overall screened cable,
minimum conductor size 0.5 mm
2
is required.
For voltage supply to the actuator motor a
standard five-core cable can be used, mini-
mum conductor size 1.5 mm
2
.
For the ZKE see separate wiring diagrams.
BAE 210, 211
Fig. 1, 5
BAE 36, 36-1, 36-3
Fig. 2, 6
Configuration
Installation
Important Notes
Wiring
LRR 1-5b/-6b
Fig. 7
LRR 1-9
Fig. 8
Important Notes
■
The external wiring shown is valid only if
the supply phases and voltages of the
controller and actuator are identical.
■
Connect screen only to the corresponding
terminal of the controller.
■
The screen must not make any other elec-
trical contact.
■
After shut-down of plant mains voltage
must be applied to the actuator until the
valve has closed completely.
■
Fig. 9 and 10 show the hot-water capaci-
ties with the various adjustments of the
regulating lever corresponding to the
number of scale divisions indicated in the
chart.
■
In purge position - regulating lever against
stop - the capacity of the BAE 36 is
approx. three times the capacity at scale
division 35.
■
If the boiler water downstream of the valve
is lifted the differential pressure (working
pressure) is reduced by approximately 1
bar for 7 m (or 2 psi for 3 feet) in lift.
■
Continuous operation at scale setting up
to 35 (BAE 36kk: up to 45); short-time
operation with adjustment values up to
max. 100; purge position - regulating lever
against stop - for rapid discharge of dirt.
The OPEN and CLOSED positions are set at
our works and must not be changed. The
operation position is adjusted with the upper
cam and preset at our works. It can be read-
justed in either direction:
1. Open housing cover.
2. Apply voltage to terminals 1 and 2 (OPEN)
or 1 and 3 (CLOSED) – dependent on cur-
rent valve position. The actuator turns infi-
ven direction. The control camshaft
●
F
turns in the same direction.
3. Switch off mains voltage when position to
be adjusted is reached (gear must not
block).
4. EF 0,5: (see Fig. 4) Turn top gear screw
●
G
of the limit switch until the top cam opera-
tes the upper snap-action contact (positi-
on-controlled limit switch clicks). The
position of the control cam is between the
OPEN and CLOSED position.
EF1, EF2: (see Fig. 5): The gear screw
●
G
,
which is the longest of the setting screws
and features a black ring, is accessible
from top.
5. Check the adjustment by electrically
motoring to the desired switch position
and, if required, make necessary readjust-
ments.
Voltage is applied across the limit switch.
ENGLISH
Capacity Charts
Important Notes
Adjustment of
Position-Controlled Limit Switch
Attention
LRR 1-5b/-6b, LRR 1-9e
With the max.-min. limit switch URS-2b
connected, the LRR 1-5/6 must be perma-
nently in operation.
When the valve must be closed during shut-
down of the burner (modulating burner ope-
ration) an additional auxiliary relay provided
on site must be used. Take care that the valve
only goes back to the HIGH (open) or LOW
(operating) position when the limit value has
been reached.
Disengaging of valve actuator
1. Switch off actuator.
2. BAE 36
Push up coupling
●
D
against spring of
actuator and hold in this position.
BAE 210, 211
Push up fork until the driving pin disenga-
ges. Turn regulating lever together with
claw.
3. Operate continuous blowdown valve via
regulating lever.
Engaging of valve actuator
1. BAE 36
Push down coupling
●
D
(ensure that
recesses in coupling slide over regulating
lever).
BAE 210, 211
Turn back regulating lever, fork slides
downward. Take care that driving pin
engages in slot of fork.
2. Switch on actuator.
Special maintenance of the continuous blow-
down valve is not required.
The synchronous motor of the actuator is
short-circuit protected.
Stalling of motor produces short rhythmical
left/right turns and will, after a prolonged
period, cause damage to the gearing.
If the motor capacitor is defective, the sense
of rotation of the motor is indefinite, i. e. it will
turn in any direction.
Fault A: The actuator
●
A
is not operating.
Remedy: Check voltage supply. Check con-
trol line and actuator motor. If the motor is
defective, replace actuator.
Fault B: The actuator motor opens and closes
the valve arbitrarily (rhythmical left/right turns).
Remedy: The synchronous motor is stalled.
Remove the obstruction.
Fault C: The actuator motor opens and clo-
ses the valve arbitrarily despite definite con-
trol pulse from controller.
Remedy: The starting capacitor of the actua-
tor is defective, replace starting capacitor.
Fault D: The value indicated on the controller
varies considerably (more than 10 %) from
the valve position indicated on the graduated
scale plate.
Manual Operation
Maintenance
Fault Finding
Operation
Attention
- TK23 Steam Traps TK24 Steam Traps GESTRA BA28 Continuous Blowdown Valves BA29 Continuous Blowdown Valves BA210 Continuous Blowdown Valves BA211 Continuous Blowdown Valves PA110 BW31 Return-Temperature Control Valves GSF GESTRA Steam Systems SZ GESTRA Steam Systems UNA-Special Float Traps TK 23 TK 24 GK11 GK21 GK14 GK24 BA 28 BA 29 BA 210 BA 211 PA 110 GK 11/21 KALORIMAT BW 31 UNA-SPEZIAL PN 16-64 UNA Gestra