Poor compressed air quality, Environmental and application impacts – Hypertherm MAXPRO200 Preventive Maintenance Program User Manual
Page 20
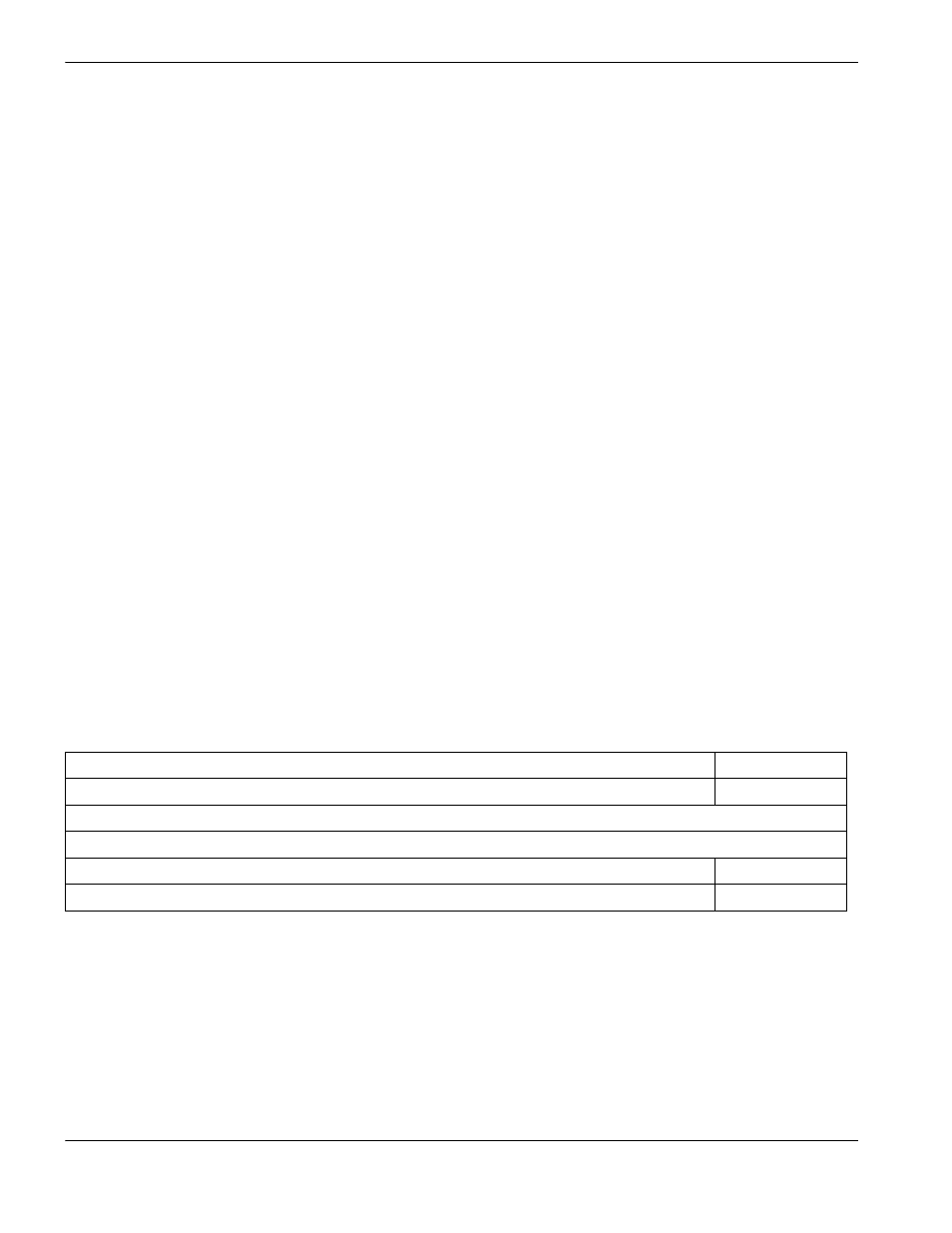
16
MAXPRO200 Preventive Maintenance Program Instruction Manual 808800
Environmental and application impacts
The component replacement schedule serves as a starting point for your replacement plans. Your operating environment
and cutting applications may include conditions that accelerate the wear rate of some components within your plasma
system. This accelerated wear will increase the frequency of component replacements. This section highlights the top
environmental or application-specific conditions known to decrease the life expectancy of components in the
MAXPRO200 Manual Gas plasma system.
Several environmental and application-specific conditions are described in the following sections. While the quantifiable
effect of each condition on the expected life of your system's components is difficult to determine, each condition is
known to have a negative impact on system performance and the life expectancy of certain components.
Review each section for the explanation of the effect on your system and components that each environmental condition
can have. If any of these conditions apply, consider adjusting your component replacement schedule.
If you have questions about the details of your replacement schedule, contact your regional Hypertherm Technical Service
team.
Poor compressed air quality
To maintain optimal performance of your system, it is important that the source of incoming air is free of contaminates
such as dirt, oil, and water. If the incoming air contains contaminates, system components can become clogged or fail to
function properly. Poor air quality usually results in increased system errors, poor cut quality, or both. The most common
components to be affected by contaminated incoming air are:
Air filter elements, solenoids and check valves. Debris in these parts limits the flow of air in the system, resulting in
poor cutting performance and gas errors (044, 053, 057, 058).
The quick-disconnect torch head. Debris in this part restricts air flow and reduces cut quality. Oil in the system may
also cause a fire in the torch head as the oil reacts with the oxygen cutting process.
Pressure sensors. Debris in these sensors can cause false pressure readings, resulting in cut performance issues
and gas errors.
If you have poor incoming air quality, consider adjusting the replacement schedule for the following components:
If you can, improve the quality of the air that enters your system to prevent this condition from impacting the life of your
system. Contact your regional Hypertherm Technical Service team if you need help or advice on the best way to improve
incoming air quality.
Description
Part number
Filter element
011093
Mechanized torches - See Table 2 – Mechanized torch parts replacement schedule on page 14 for part numbers
Handheld torches - See Table 3 – Handheld torch parts replacement schedule on page 15 for part numbers
Gas assembly
428034
Pressure transducer
428042