Page 4 of 5 – Yaskawa iQpump1000 AC Drive User Manual
Page 4
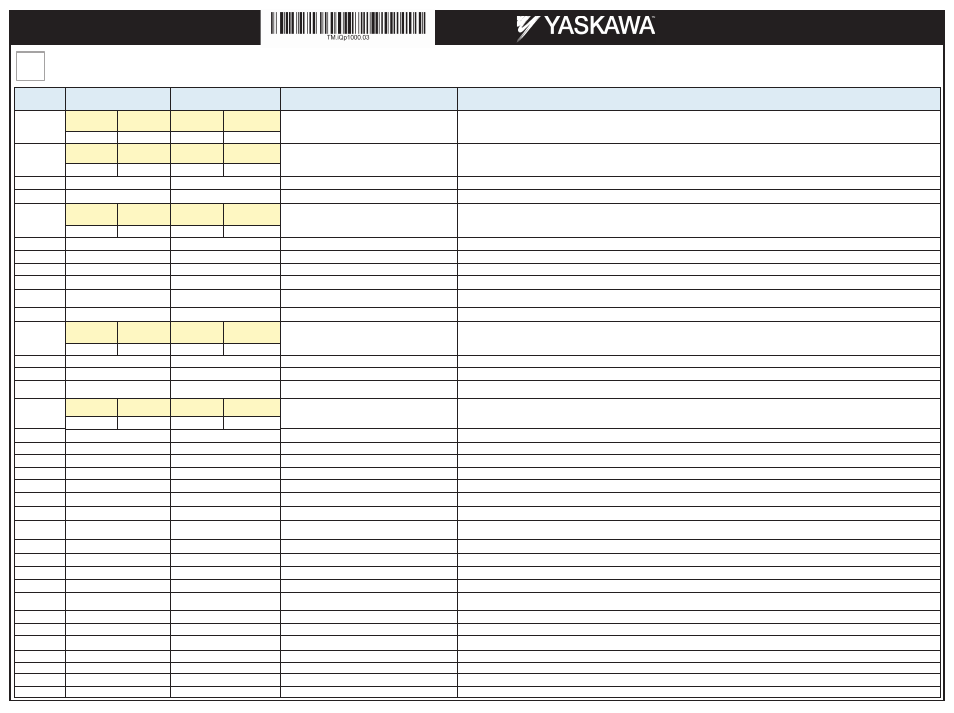
Page 4 of 5
Yaskawa America, Inc., 2121 Norman Drive South, Waukegan, IL 60085, (800) YASKAWA (927-5292) Fax (847) 887-7310, [email protected], www.yaskawa.com, Document Number: TM.iQp1000.03 05/29/2014 © Yaskawa America, Inc.
Parameter
Jockey iQPump1000
P1 Setting
Booster iQPump1000
P2 and P3 Setting
Description
Comments
b5-02
Pressure
Tank
No Pressure
Tank
Pressure
Tank
No Pressure
Tank
Proportional Gain Setting (P)
Increase proportional gain to make iQpump1000 more responsive. Caution: can cause instability if value is too high.
2.0
4.0
2.0
4.0
b5-03
Pressure
Tank
No Pressure
Tank
Pressure
Tank
No Pressure
Tank
PI Integral Time (I)
Decrease integral time to make iQpump1000 more responsive. Caution: can cause instability if value is too low.
3.0 sec.
2.0 sec.
3.0 sec.
2.0 sec.
C1-01
9.0 sec.
9.0 sec.
Acceleration Time 1
Time it takes to accelerate the pump motor from zero to maximum speed.
C1-02
5.0 sec.
5.0 sec.
Deceleration Time 1
Time it takes to decelerate the pump motor from maximum speed to zero.
C6-02
Centrifugal
Pump
Submersible
Pump
Centrifugal
Pump
Submersible
Pump
Carrier Frequency
Note: Please refer to the iQPump1000 manual for drive full load amp de-ratings if setting C6-02 carrier frequency selection other than 6 or 7
for drives above 40HP.
2
7
2
7
E2-01
11
P2 = Mtr FLA, P3 = Mtr FLA Motor Rated Current
Set to the motor nameplate full load amps.
H1-07
73
73
Terminal S7 Input - Low City Pressure
Make sure Low City Switch is wired into S7-SN of all drives.
H5-01
1
P2 = 2, P3 = 3
Drive Node Address
P1-01
3
3
Pump Mode
Set drive software up for Memobus Multiplexing.
P1-03
XX PSI
XX PSI
Feedback Scaling
This should be the maximum range of the transducer output based on 4-20ma. If transducer is 200 PSI that this is what should be
programmed in P1-03.
P1-04
-5 PSI
-5 PSI
Start-Draw down Level
Note: Make sure to see the "-" negative sign on display.
P1-06
Centrifugal
Pump
Submersible
Pump
Centrifugal
Pump
Submersible
Pump
Minimum Pump speed
This should always be set based on where the pump curve starts working to overcome the head and system losses.
35.0 Hz
40.0 Hz
35.0 Hz
40.0 Hz
P1-11
XX PSI
XX PSI
High Feedback Level
High Pressure fault should be set on average 20 PSI over the system set point.
P1-12
4 sec.
4 sec.
High Feedback Level Delay Time
P4-10
1
1
AUTO Mode Operator Run Power Down Storage
This allows drive to recover and automatically run after a loss of Utility Power if run (Auto) command is via keypad.
Warning: System will automatically restart.
P4-12
Centrifugal
Pump
Submersible
Pump
Centrifugal
Pump
Submersible
Pump
Trust Bearing Frequency
Thrust bearing frequency shout not be disabled when using a submersible pump motor.
0.0 Hz
30.0 Hz
0.0 Hz
30.0 Hz
P4-21
1
1
Low City Input Select
Note: input is based on Normally Closed. (Open switch indicates low city pressure, and system will shut down)
P4-21
5 sec.
5 sec.
Low City On-Delay Time
P9-01
1
2
Lead Drive Select
Booster pumps will alternate every run cycle. Jokey pump does not alternate.
P9-02
2
2
Feedback Source
System programmed for redundant transducer feedback. Each drive has its own transducer.
P9-03
0 Hr.
0 Hr.
Alternation Time
Alternation disabled as the Jockey pump will always be the lead pump to start and the larger booster pumps will alternate every run cycle.
P9-05
2
0
Lag Fixed Mode
When the Jockey pump cannot keep up with the system demand a booster pump will stage on and the Jockey pump will turn off.
P9-06
59.5 Hz
59.5 Hz
Lag Fixed Speed
P9-08
2
2
Add Pump Mode
Sets the conditions for the lead pump drive so that the output speed must rise above P9-09 and the pressure to fall below P9-10
before adding an additional pump to the system.
P9-09
59.5 Hz
59.5 Hz
Add Freq Level
Sets the system to stage on lag pump when lead pump is above P9-09 level and the system is 5PSI below Auto Set point.
P9-10
5.0 PSI
5.0 PSI
Add Delta Level
Sets the system to stage on lag pump when lead pump is above P9-09 level and the system is 5PSI below Auto Set point.
P9-11
14 sec.
14 sec.
Add Delay Time
Sets the time when the lag pump will stage on. Adjust as needed for system operation.
P9-12
0
0
Remove Pump Mode
P9-13
45.0 Hz
45.0 Hz
Remove Frequency Level
Sets the lag pump output frequency when it de-stages and goes back to a single lead pump. May have to adjust based on pump system
curve.
P9-15
5 sec
5 sec
Remove Delay Time
Sets the time when the lag pump will de-stage when speed falls below P9-13.
P9-18
98.0%
98.0%
High Feedback Quick De-stage
Allows program to this value when using High Pressure as Fault.
P9-20
2
0
Allow Network Run
Jockey Pump will be the first to run at all times until a booster pump is staged on.
P9-21
7
8
Run Priority
P9-24
0
5 sec
Lead swap at speed
When the booster pumps shuts down or goes into sleep mode for 5 seconds the lead is handed back to the Jockey pump .
P9-25
2 for Duplex, 3 for Triplex
2 for Duplex, 3 for Triplex
Max Number of Running Pumps
Program network for 2 or 3 pumps on the system.
Q1-01
120 PSI
120 PSI
System Setpoint
Note: Program this value last on the main keypad screen using Q1-01. U1-01 auto set point is the same as Q1-01.
Step
8
Parameter setup for triplex system with jockey pump and two pumps as boosters with or without pressure tank.
Transducers used with a range of 200 PSI and System setpoint set for 120 PSI. Booster pumps will lead-lag with 24hrs alternation.
iQpump1000 AC Drive
Multiplex Quick Start Procedure