Yaskawa Drive Simulator User Manual
Page 6
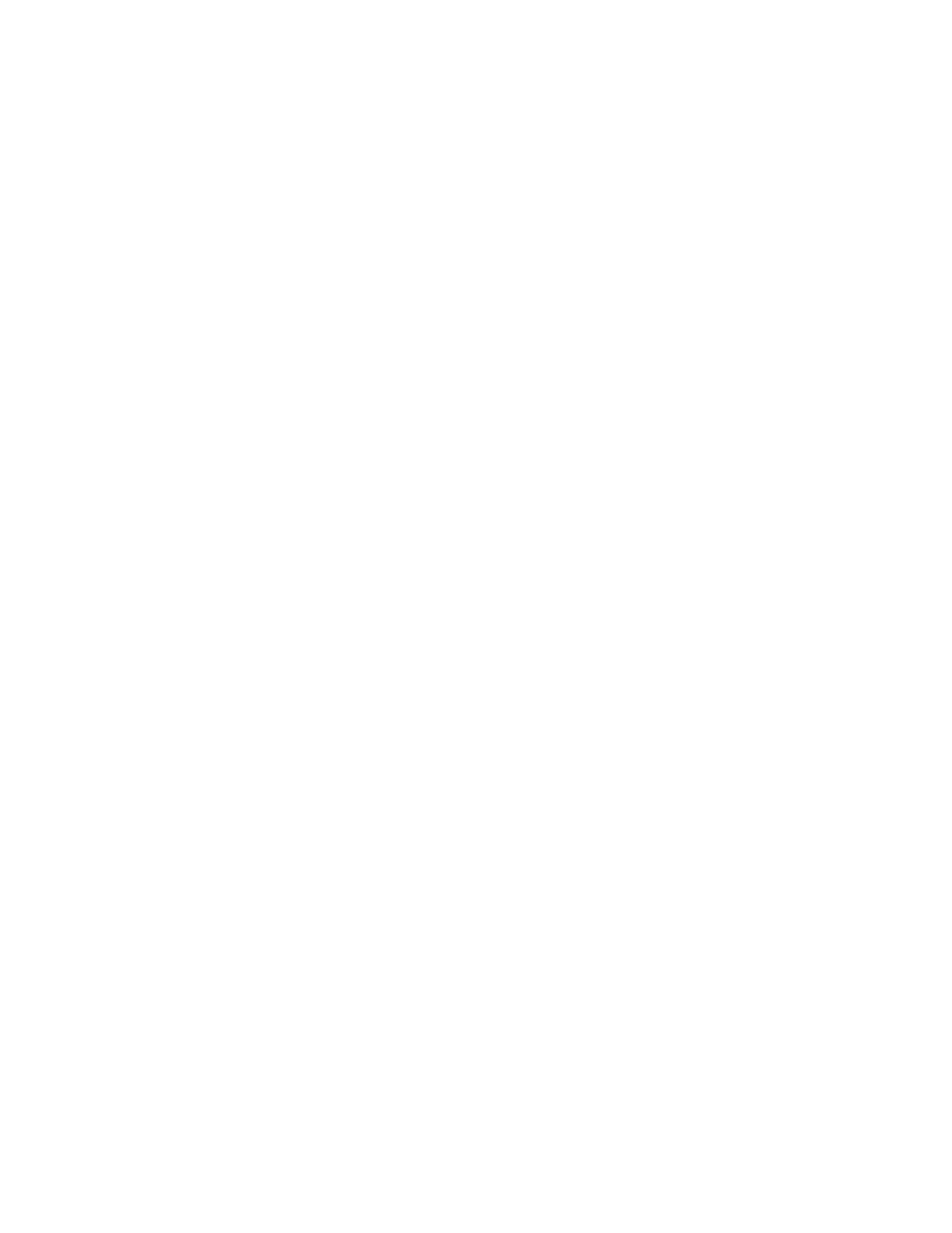
TM.AFD.Simulator Page 6
5. Module Description and Usage Guide:
• User I/O terminal:
1. Digital inputs: middle-positioned toggle switches ON/EXT/OFF S1-S12.
2. Digital outputs: Four green (D19-D22) and two red LED’s (D23 and D24).
3. Analog inputs: 0-10V/
±10V or external for AIN1 and AIN3. 4-20mA for AIN2.
VR1 is A1, VR2 is A2 and VR3 is A3. The reference voltage will be selected through S21 from
10V,
±10V and External.
4. Analog outputs: Two 10-LED displays, U31, U33 with negative-sign LED’s, D140 and D141
will monitor the AM and FM outputs in almost
±1V steps.
• Pulse generator module:
1. Amplitude: adjustable through VR5 between 0-22V
2. Current: Limited and short-circuit protected at 25mA dynamically
3. Frequency: Adjustable through VR4 between approx. 15Hz-25kHz
• Communication module:
1. RS-232, RS-485 and RS-422 standards and voltage levels are supported.
2. RS-422/RS-485 flow control selectable between internal or RTS signal through S14-position1
switch (internal is RS422 and external is RS485 through RS232).
3. Four LED’s, D13-D16 monitor all the transmission and reception activities.
4. Connectors: RJ-45 for Keypad, DB9 for RS-232 and Header for RS422/485 (J4 to connect to
control-board’s keypad connector, J5 for PC, J3 for keypad, J2 for user I/O-RS422/485)
5. Routing: Through S38 (RS422/485: PC-RS232 will be routed/converted to RS422 of the drive
and keypad will be routed to control card’s keypad port, MEMACCESS: PC-RS232 will be
routed to control card’s keypad port and keypad will be disconnected, MEMFLASH: PC-RS232
will be routed to control card’s keypad port in FLASH mode and keypad will be disconnected).
6. In communication router switch (S38) mode of “RS-422/485”, the connected PC through its RS-
232 will be also able to participate as a RS-485 network participant. Therefore, flow control will
be through its RTS pin and accessible through S14/1 switch, set to “External”. Also the related
parameter in the drive should be set accordingly (H5-07Å1) for the network-side flow control.
Note: The unit in this mode does not compromise the network/drive isolation, as the control
card’s link to network will be differential anyway.
• Power supply module:
1. Voltages available:
±15VDC, 24VDC, 5VDC, IP5VDC (10V-unregulated),
IP12VDC (19V-unregulated/unloaded), IP24VDC (26V-unregulated/unloaded)
2. All supplies monitored by LED’s D56-D59, D31-D33.
3. Power Recycle: Manually (through push button S37 -Power Recycle) and externally (through
EAP-External Access Port) recycled and monitored toward the control card, in almost 1 second.
The ready signal will be also generated and available to EAP after 2 seconds for automatic
testing purposes. LED’s D148 (READY) and D151 (R5V) monitor the whole recycling process
either way. Please note that this feature is exactly like recycling the main power switch of the
unit with exactly same functionality and effect.
4. Current available to external devices is limited at less than 50mA for all supplies. Please refer to
the pin-array on the left side of the unit.
• Dual Encoder emulator module:
1. PG-I is assumed to be the slave motor encoder and PG-II, the master motor encoder. However
they are independently interchangeable based on application.
2. Logic level: 5V-TTL differential
3. Max frequency: Approx. 25Hz to 44kHz separately adjustable and range-selectable through
VR8, VR9 and S28 (25Hz-44kHz, 250Hz-44kHz and 2.5kHz-44kHz).
4. Signal format: 90
°-Phase-shifted, quadrature, differential A/~A, B/~B, C/~C