Oil tank and piping – Boyertown Regal Oil Furnace Nrg Max User Manual
Page 23
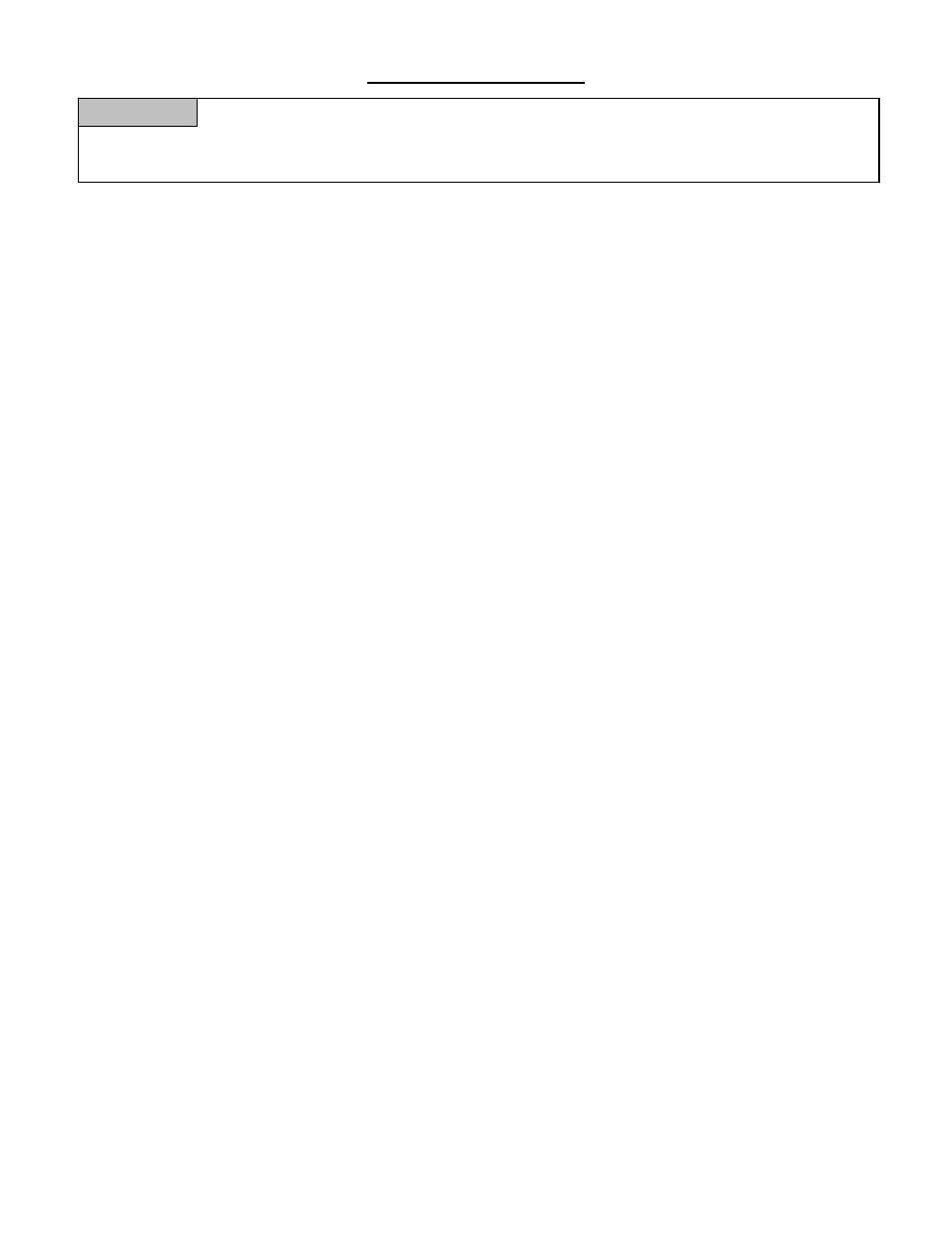
23
Oil Tank and Piping
Installation of oil tanks must meet all local codes and ordinances. Refer to NFPA-31 for
complete guidelines on oil tank installations internal to the building, outside above and below ground
tanks.
Oil tanks located inside the building shall not be in excess of 275 gallons individual capacity and shall
not be located within 5 feet horizontally from any source of heat, either internal or external to the
appliance being served or in a manner that the temperature of the oil in the tanks exceeds 25
º
F above
room temperature.
Connect burner to oil supply using the correct size heavy wall copper tubing, wrought iron, steel or
brass fittings in accordance with the literature attached to the pump. All lines must have shut off
valves, a good pipe joint compound approved for use with oil on all pipe threads, no kinks, no sharp
bends, and be properly tested for leaks. Use flare fittings only when assembling oil lines. Avoid use
of fittings in inaccessible locations. Avoid running tubing against any type of heating unit and across
ceiling or floor joists. Piping shall be supported and protected from physical damage and where
necessary, protected against corrosion as per code. Piping systems shall be maintained liquid tight. A
piping system that has leaks constitutes a hazard which must be repaired in an approved manner. All
oil feed lines to burners must be air tight. The slightest air leak, caused by loose fittings, bad gaskets
or any other reason, can cause a foaming oil stream which will cause any of the following conditions:
a) Intermittent firing, causing safety shutdown.
b) Poor starts.
c) Smokey starts.
d) Continual sooting of furnace and burner parts including the cad cell.
e) Reduced firing rate, inefficient operation and erratic fire pattern.
f) A dangerous combustion condition, allowing the combustion chamber to fill with a lean
mixture (too much air in the oil stream) which could cause a delay in ignition of the fuel
mixture until the danger point has been reached.
This fuel unit when connected with a single pipe system is satisfactory only where the oil supply is on
the same level or above the burner, permitting gravity flow of oil. When it is necessary to lift oil to the
burner, a return line must be connected between the fuel unit and the tank. This requires the insertion
of the "bypass" plug in the oil pump. The bypass plug and pump instructions are attached to the pump.
Installation of a check valve in the suction line of a two pipe system is advisable under all
circumstances. Be sure the check valve fittings are air tight. If lift exceeds 10 ft. a two-stage pump
must be installed with a two pipe system.
If any part of the fuel oil tank is above the burner, an anti-siphon device must be used to prevent the
flow of oil in case of an oil line breakage.
Suction vacuum must be held to acceptable limits. THE VACUUM TEST IS WORTH THE TIME
REQUIRED TO MAKE IT. This problem becomes proportionately larger with underground tanks.
Connect vacuum gauge to oil pump. Suction vacuum must not exceed 10 inches of mercury for single
stage pumps and 15 inches for two stage pumps. It is preferable to stay below these limitations. When
the suction line is tight and properly installed the pump will hold its vacuum for a minimum of 60
minutes after shutdown.
Use an oil filter with the proper capacity to filter for all installations. Install the filter inside the
building between the tank shutoff valve and the burner. The filter cartridge should be replaced at least
once a year. The filter body should be thoroughly cleaned before installing a new cartridge.
WARNING