Flowserve 510si IOM Logix User Manual
Page 11
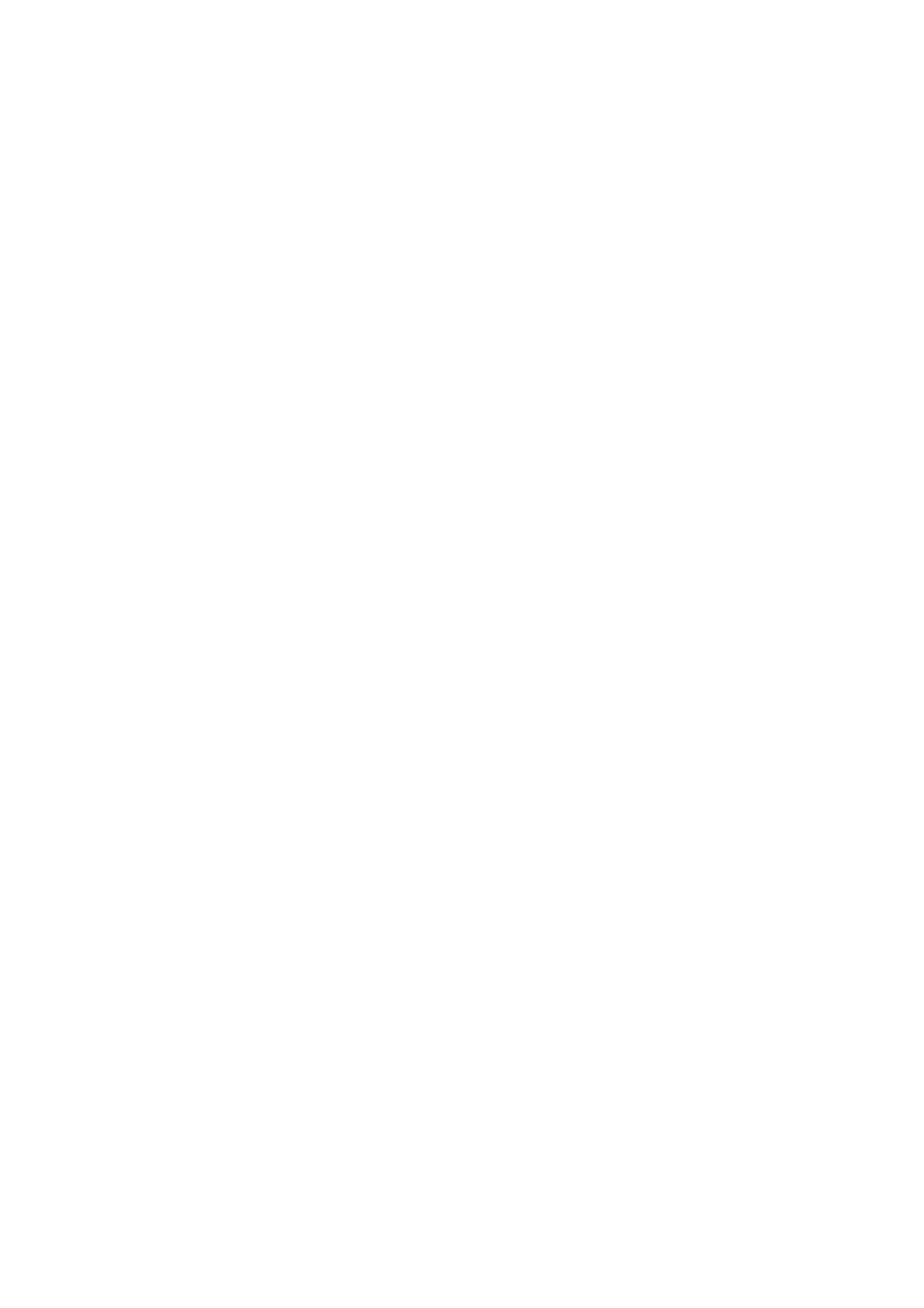
11
indicating that it is waiting for the maximum signal to
be input to the positioner. Normally this will be 20
mA, but if split range operation is required use the
maximum current for the desired range. When the
maximum signal value set at the desired value, press
the ∆ and ∇ buttons simultaneously to set the span.
The LED’s then will flash a sequence of Y-Y-G-G
indicating that the calibration is complete. The signal
can now be adjusted to the desired output value
without affecting the valve position. Press the ∆ and
∇ buttons simultaneously to put the unit back in
operation. Note that the input calibration correlates
the signal to 0% and 100% signal it does not affect the
position calibration all since that calibration is done
separately with the Quick-Cal button.
8.7.2
Output loop calibration (optional) - If a loop calibra-
tion is started with the Output loop selected on the
Loop calibration Dip switch, the LED’s will flash a
sequence of Y-G-G-G indicating that it is waiting for
the 0% signal to be adjusted using the ∆ and ∇
buttons for the output current loop on positioner on
terminals +31 and –32. (Note that the loop must be
externally powered with a voltage between 12VDC
and 40VDC and a current meter used to measure the
current in the loop). Normally this will be 4 mA, but
if split range operation is required adjust to the
minimum current for the desired range. When the 0%
signal value is set at the desired value, press the ∆ and
∇ buttons simultaneously to proceed to the next step.
The LED’s will now flash a sequence of Y-R-G-Y
indicating that it is waiting for the 100% signal to be
adjusted using the ∆ and ∇ buttons for the output
current loop. Normally the 100% setting will be 20
mA, but if split range operation is required adjust to
the maximum current for the desired range. When
the 100% signal value set at the desired value press
the ∆ and ∇ buttons simultaneously to complete the
calibration.