Flowserve Modutronic 20 II Modulating Position Controlle User Manual
Page 20
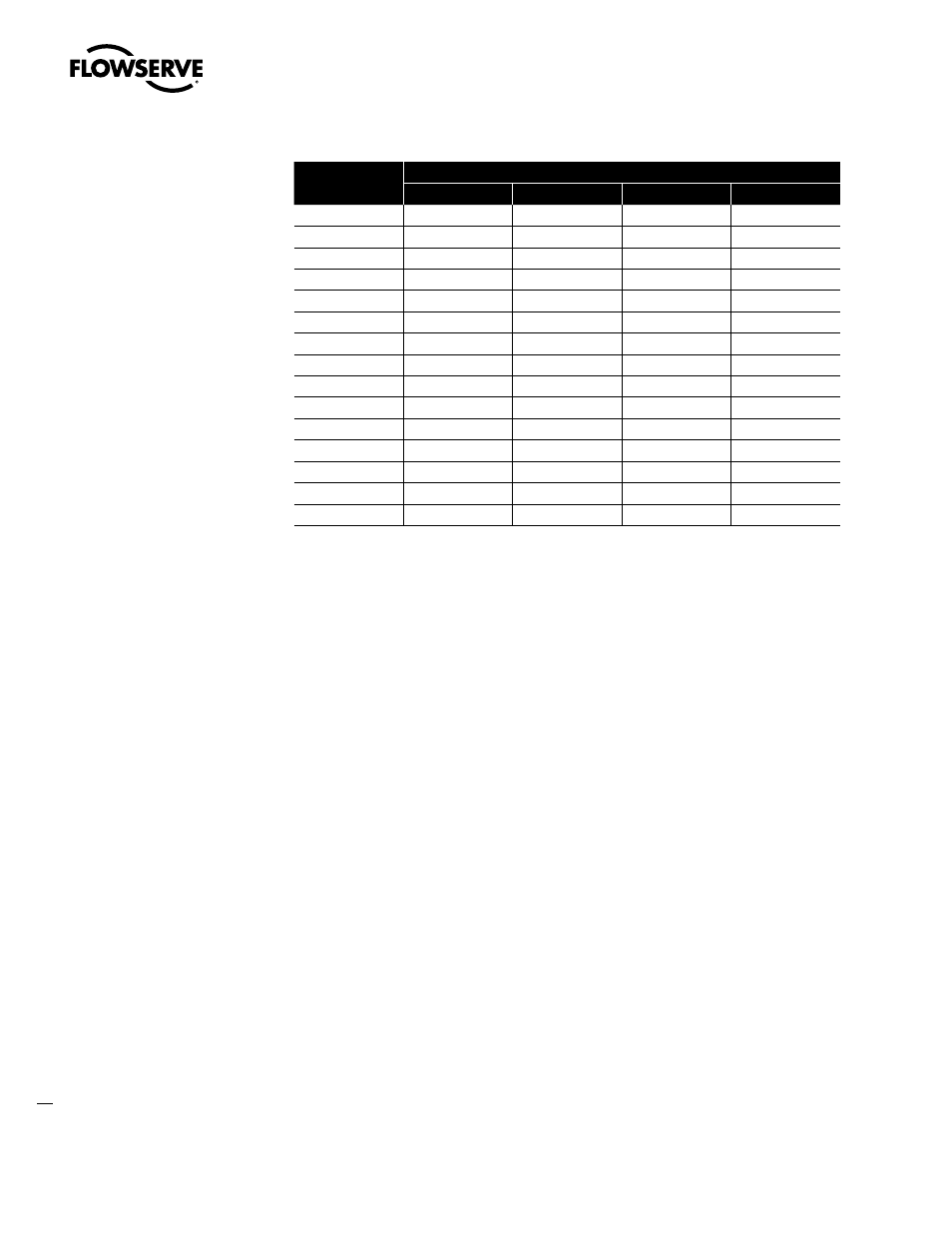
Limitorque Actuation Systems Modutronic 20 II FCD LMENIM4002-00 – 08/06
20
Table 6.1 – DIP Switch Setting Levels of Deadband Accuracy
Deadband
Percentage
Dip Switch Number
1
2
3
4
± .5%
Off
Off
Off
On
± 1%
Off
Off
On
Off
± 1.5%
Off
Off
On
On
± 2.5%
Off
On
Off
Off
± 3.0%
Off
On
Off
On
± 3.5%
Off
On
On
Off
± 4.0%
Off
On
On
On
± 6.0%
On
Off
Off
Off
± 6.5%
On
Off
Off
On
± 7.0%
On
Off
On
Off
± 7.5%
On
Off
On
On
± 8.5%
On
On
Off
Off
± 9.0%
On
On
Off
On
± 9.5%
On
On
On
Off
± 10.0%
On
On
On
On
WARNING: Hazardous Voltage in Control Compartment. Exercise caution while calibrating the
Mod 20 II with the Actuator Control Compartment open and power ON.
5. Set the mA Calibrator for the minimum signal level (normally 4 mA). The INPUT ACTIVE LED on
the Mod 20 II should be illuminated. If not, reverse the polarity of the mA calibrator connections.
6. If the Actuator is equipped with an AUTO/MANUAL or LOCAL/REMOTE selector switch, turn the
selector to the AUTO or REMOTE position.
7. Apply power to the Actuator and the Mod 20 II. The POWER ON LED on the Mod 20 II should be
illuminated.
8. The Actuator may run in either direction and then stop;
a. If the unit stops, proceed to Step 9.
b. If the unit hunts back and forth, decrease the DEADBAND accuracy by changing the DIP
Switch setting (refer to Table 6.1). Continue to Step 9.
c. If the unit runs all the way to one end of travel and stops, the Potentiometer Leads are
probably wired backwards; reverse the Feedback Potentiometer’s polarity by reversing the
end leads at the Terminal Strip or on the Interconnect Board (if your application uses the
Compact Integral Interconnect Board, the Plug-in Harness from the Pot to the Interconnect
Board can be rotated 180˚ to reverse the polarity).
9. Adjust the ZERO point. This step calibrates the minimum or zero set-point to correspond to
the end-of-travel of the Actuator and of the Feedback Potentiometer. Rotate the ZERO control
slowly in the CW
z
direction. This will cause the Actuator to be driven slowly towards the
minimum control position (normally CLOSED). Continue rotating the ZERO control CW
z
until
the minimum (CLOSED) Position Limit Switch trips and the motor stops. The CLOSE LED should
illuminate each time the Motor operates.
10. Adjust the control SPAN. This step calibrates the total SPAN of the control function and sets
the maximum setting to correspond to the end-of-travel of the Actuator and of the Feedback
Potentiometer.
c