3 fieldbus overview, Understanding fieldbus, Hardware architecture – Flowserve 400MD Logix User Manual
Page 12: Software architecture
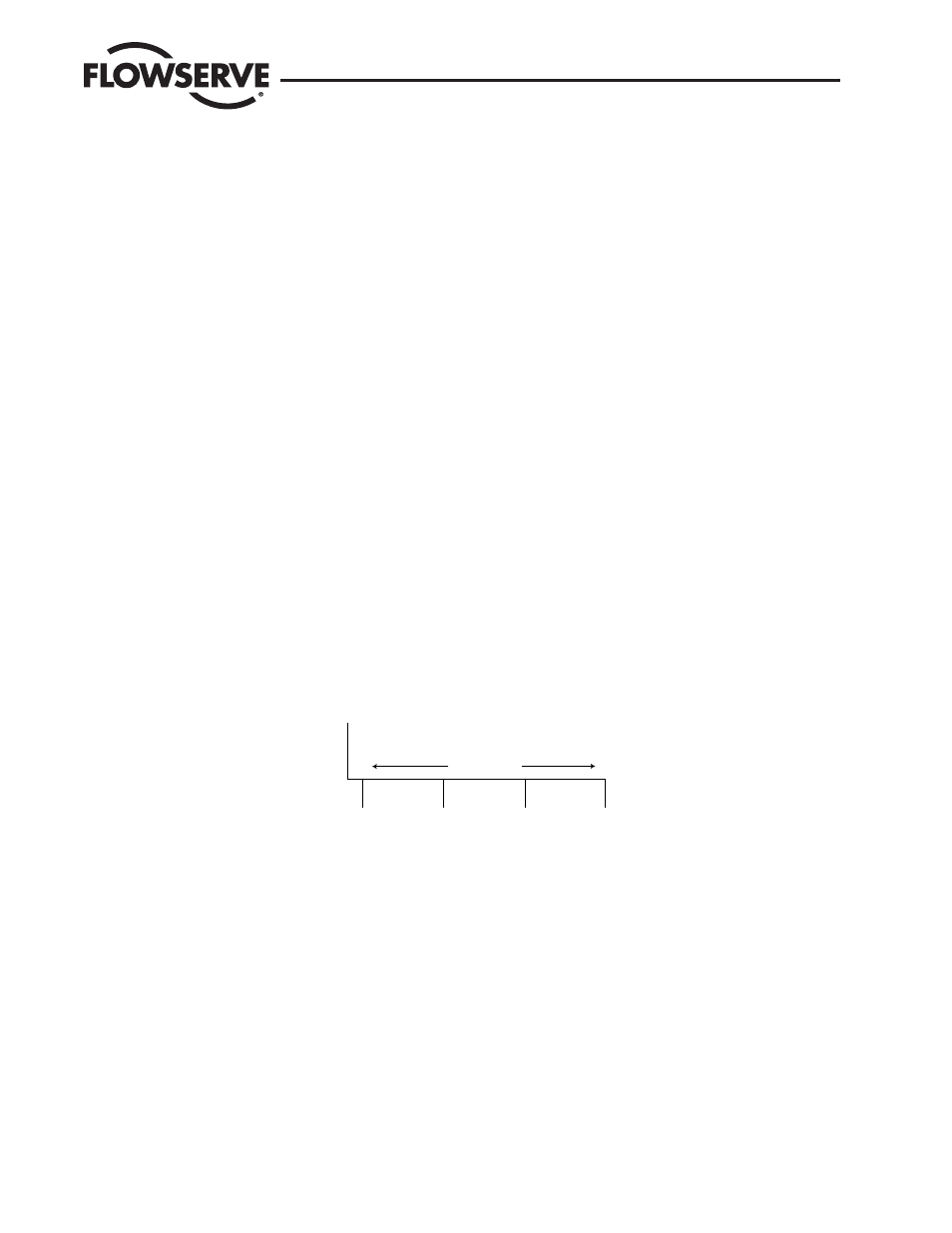
•
Soft limits or MPC functions are disabled
•
Valve has zero deviation with a present input command of 50 percent
•
Actuator is tubed air-to-open
Given these conditions, 50 percent represents a command of 50 percent. Custom characterization is disabled so the command is passed 1:1 to the
FINAL_VALUE. Since zero deviation exists, the stem position is also at 50 percent. With the stem at the desired position, the spool valve will be at a
posi tion in which no air flow is allowed to either side of the actuator. This is commonly called the null or balanced spool position. Upon a change in the
command from 50 percent to 75 percent the posi tioner sees this as a command of 75 percent. With linear characterization, the FINAL_VALUE becomes
75 percent. Deviation is the difference between control command and stem position: Deviation = 75 percent - 50 percent= +25 percent, where 50
percent is the present stem position. With positive deviation, the control algorithm sends a signal to move the spool up from its present position. As the
spool moves up, the supply air is applied to the bottom of the actuator and air is exhausted from the top of the actuator. This new pressure differential
causes the stem to start moving towards the desired position of 75 percent. As the stem moves, the deviation begins to decrease. The control algorithm
begins to reduce the spool opening. This process continues until the deviation goes to zero. At this point, the spool will be back in its null or balanced
position. Stem movement will stop. Desired stem position has now been achieved.
One important parameter should be discussed at this point: Inner loop offset or spool offset. Referring to Figure 1.3, a number called inner loop offset
(SPOOL_OFFSET) is added to the output of the control algorithm. In order for the spool to remain in its null or balanced position, the control algorithm must
output a non-zero spool command. This is the purpose of the inner loop offset. The value of this number is equivalent to the signal that must be sent to
spool position control to bring it to a null position with zero stem deviation. This parameter is important for proper control and will be discussed further in
the Control and Tuning section.
1.3 Fieldbus Overview
Understanding Fieldbus
Fieldbus is an all-digital, serial, two-way communication system which interconnects industrial ‘field’ equipment such as sensors, actuators, and controllers.
Fieldbus is a Local Area Network (LAN) for field instruments with built-in capability to distribute the control application across the network. See Figure 1.4.
Figure 1.4 Fieldbus Connecting Control Room and Field Devices
The Fieldbus Foundation has defined standards to which field devices and operator/control stations communicate with one another. The communications
protocol is an open system to allow all field devices and control equipment which are built to the FOUNDATION fieldbus standard to be integrated into a control
system, regardless of the device manufacturer. This inter operability of devices using fieldbus technology is becoming the industry standard for automation
and distributed control systems.
Hardware Architecture
The physical architecture of fieldbus allows installation of fieldbus devices using a twisted-pair cable. Often, existing wiring from analog
devices can be used to wire up digital fieldbus devices. Multiple field devices can be connected on one cable (a multi-drop link), rather than
conventional point-to point wiring used for analog devices. See Wiring the Logix 3400MD Digital Positioner to a Fieldbus Network.
Software Architecture
Fieldbus software architecture provides for more control functions to be available in the micropro cessor-based field device. Since fieldbus is a digital com-
munication system, more data is available to operators for process monitoring, trend analysis, report generation, and trouble analysis. Device software
changes can be downloaded to field devices remotely from the operator station (or PC) in the control room.
Fieldbus LAN
ST 3000 FF
Logix 3400IQ
Digital Positioner
Fieldbus
Device
Fieldbus
Device
Control Room Device
(Operator Interface)
Logix 3400MD Digital Positioner LGENIM3405-02 11/13
12