Insinger GalleyMaster Series User Manual
Page 19
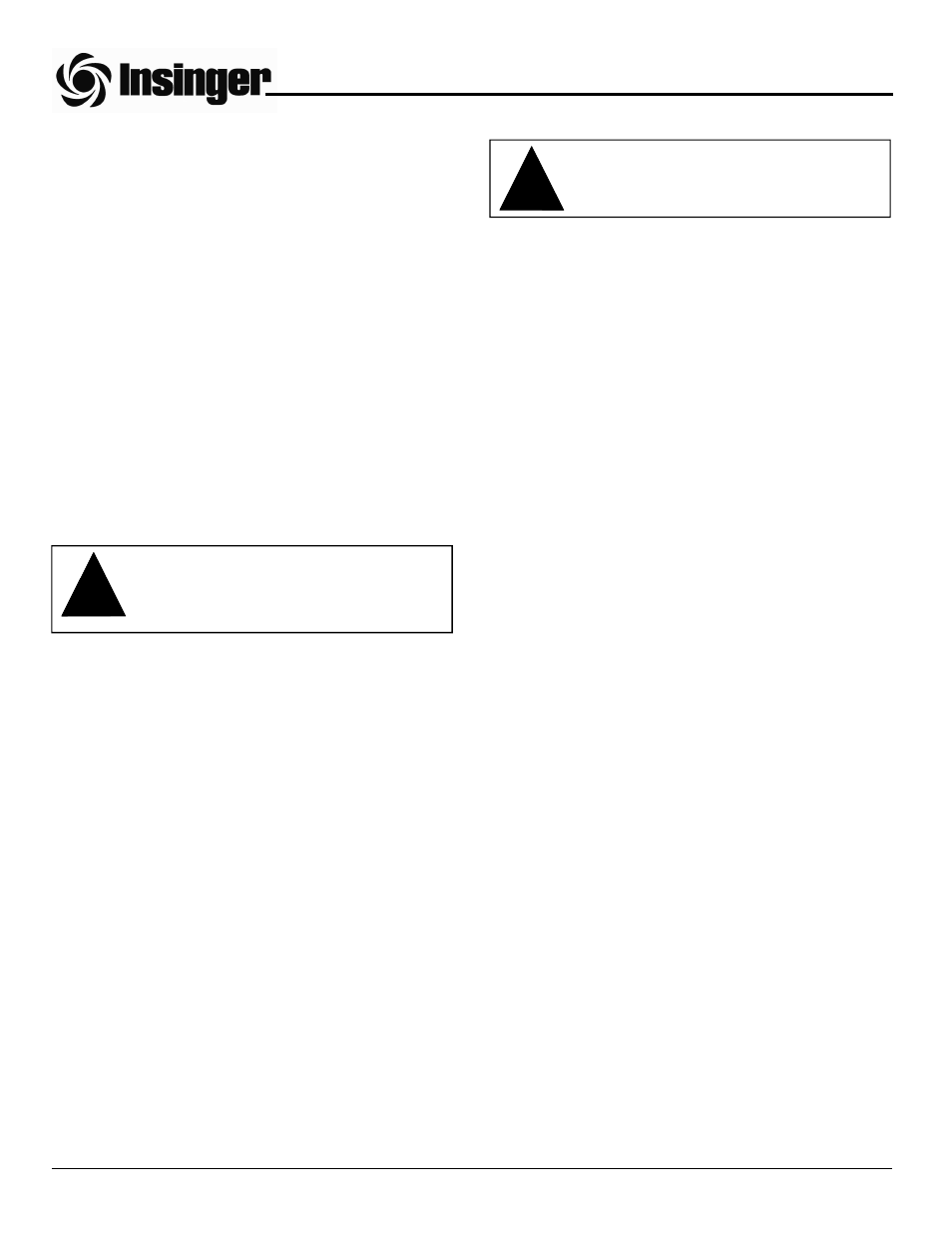
SCHEDULED MAINTENANCE
The GalleyMaster Dishwasher is a rugged and simple
machine. The scheduled maintenance described in this
chapter is mostly a periodic set of inspections and
cleaning.
WEEKLY REQUIREMENTS FOR INSPECTION AND
MAINTENANCE
Inspect for external leakage.
Inspect the outside of the machine, including all piping,
piping components, rinse water booster, and the tank
side and bottom seams for leakage. Tighten or repair
as necessary.
Inspection of probes and moving float switches.
Stop the machine and drain both tanks, see page ____
for detailed instructions.
PART 4 MAINTENANCE & REPAIR PROCEDURES
QUARTERLY REQUIREMENTS FOR INSPECTION
AND MAINTENANCE
Check and adjust final rinse pressure.
The final hot rinse pressure must be 20 psig. while the
rinse water is flowing. Adjust the pressure reducing
valve during a rinse cycle (CW to increase, CCW to de-
crease pressure).
If the supply pressure to the booster is 20 psig. or
greater, and the rinse pressure is below 20 psig and can
not be increased, the strainer in the pressure reducing
valve may be clogged. Clean the strainer per 6.2.1.
Clean steam strainers (steam heated machine only).
Close the manual valves on the wash tank, rinse tank,
and booster steam supplies.
Remove the plug and strainer basket from each "Y" type
steam strainer and flush clean.
Replace strainer and plug.
Open steam supply valves.
Inspect condensate traps (steam heated machines only).
Condensate traps (Fig. 6-14; Fig. 7-7, item 13; Fig. 7-8,
item 23;) are located below the steam booster and below
each tank.
Check to see that each trap is operating correctly, allow-
ing condensate to flow when the supply valve is open. A
condensate trap that is stuck shut, possibly due to corro-
sion, will not allow the condensate to flow, and no heat
will be released within the booster or tank. A trap that is
stuck open will not allow the heated unit to reach full
operating temperature. A faulty trap should be replaced.
Inspect inside of control enclosures and junction boxes.
After draining, manually move each float switch to verify
that there is no binding or sticking. See Figure 6-13.
Check all electrical probes for dirt and mineral accumu-
lation. Clean as required.
De-liming.
Accumulated mineral deposits must be removed from
the inside surfaces of the machine on a periodic basis.
The frequency of de-liming depends on the hardness of
the water, the type and concentration of detergents
used, and the amount of washing time. Until the proper
frequency can be determined, de-lime on a weekly
schedule. Follow the instructions supplied with the de-
liming chemicals.
Exterior Cleaning.
Wipe down the exterior surfaces of the machine, using a
commercial stainless steel cleaner.
!
WARNING:
Inside of the machine is
hot. Allow the machine to cool to 110° F.
before proceeding. Wear rubber gloves.
WARNING:
Do not use a hose to clean
the exterior of the machine.
!