Up milling, Down milling, Feed rates – Smithy GN1300 User Manual
Page 108: High-speed-steel cutters
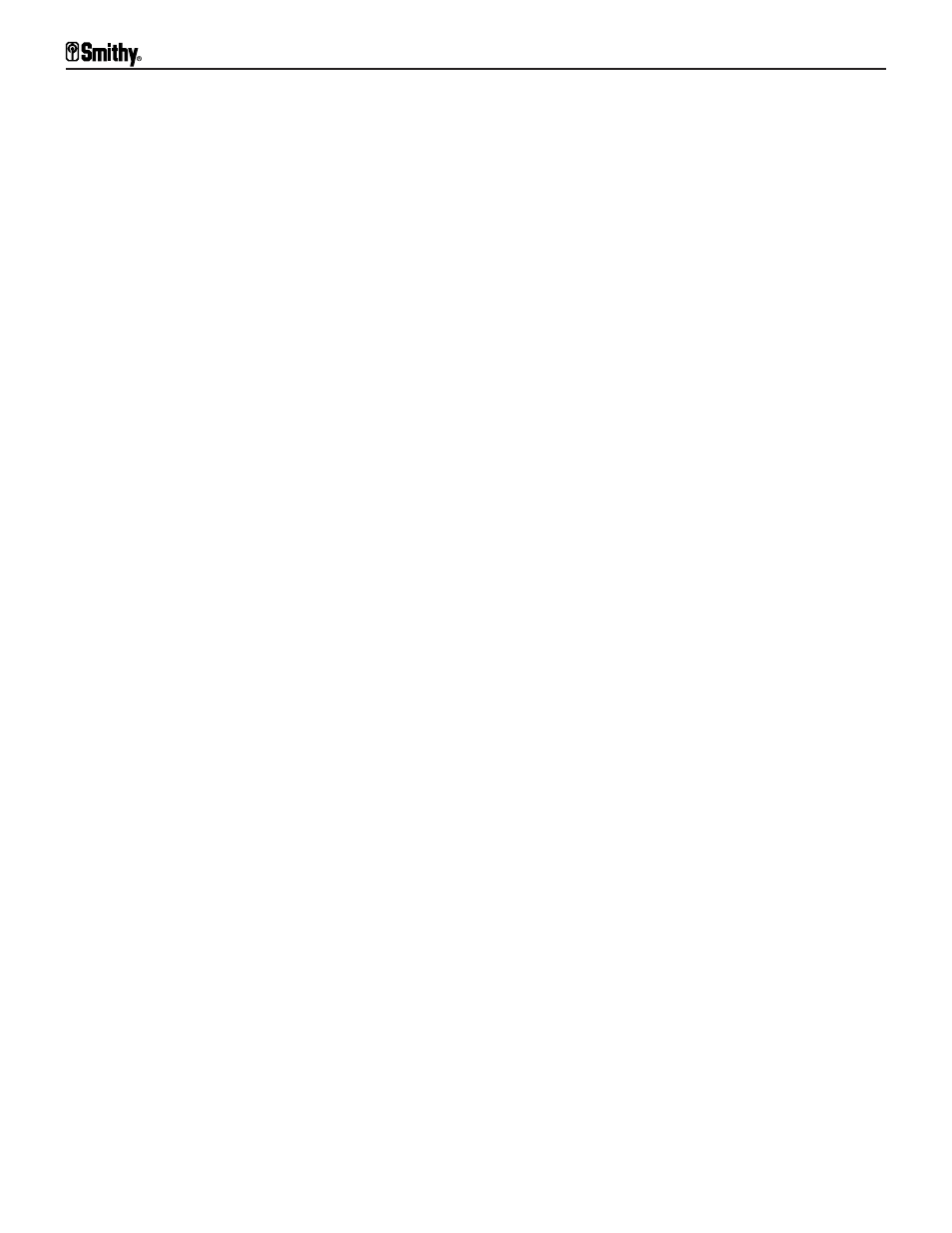
Up Milling
In up milling, forces on the workpiece tend to pull it out of the vise or fixture holding it,
so fasten it securely. These forces also push the workpiece away from the cutter, which
eliminates backlash. Up milling is advised for milling cast iron, softer steels, and other
ductile materials. In general, it's how you should perform milling operations.
Down Milling
Down milling usually produces good surface finishes because chips do not sweep back
into the cut. Setups are more rigid, an advantage when cutting thin workpieces held in a
vise or workpieces held in a magnetic chuck. Down milling also produces straighter cuts.
We recommend down milling when using carbide cutters because there is less wear on
the cutting tool. In general, however, avoid it because of the backlash problems
associated with it.
Feed Rates
Your feed rates should be as high as your machine, cutting tool, workholding method, and
workpiece can tolerate while giving a good finish. Feed rate is usually given in inches per
minute (ipm). You determine feed rate by the speed of the cutter in rpm and the num-
ber of teeth in the cutter.
There are many factors to consider in selecting the feed per tooth, and there is no easy
formula to follow. Here are several principles to guide you:
• Use the highest feed rate conditions allow
• Avoid using a feed rate below 0.001” per tooth
• Harder materials required lower feed rates than softer materials
• Feed wider, deeper cuts more slowly than narrow, shallow cuts
• Slower feed rates gives a better surface finish
• Never stop the feed before finishing the cut
If you know the feed in inches per tooth, use the formula to calculate table feed rate in
inches per minute (ipm):
ipm = ipt x N x rpm
where:
ipt - inches per tooth
N - number of teeth in the milling cutter
rpm - spindle speed of the milling machine.
High-speed-steel Cutters
The advantage of HSS cutter bits is you can shape them to exact specifications through
grinding. This lets you grind a stock shape into any form. Stock shapes come in an
assortment of types, including squares, flats, and bevels. Many shops buy their cutters as
ready-ground or ready-to-grind bits or blades.
Granite 1300 Series Operator’s Manual
A-6
For Assistance: Call Toll Free 1-800-476-4849