First Co WH / XH Horizontal Double wall User Manual
Page 5
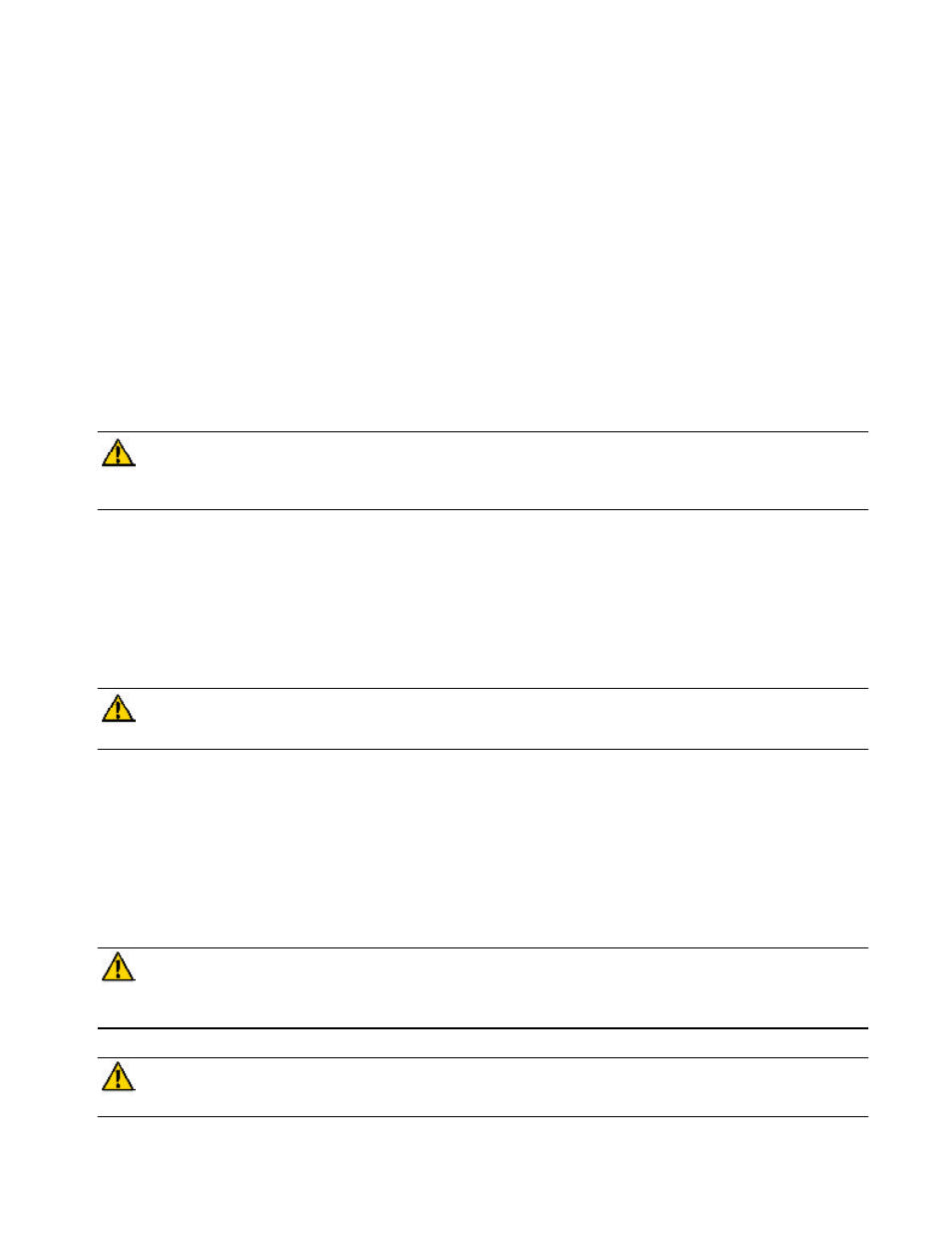
5
PROCEDURE 5 – COIL PIPING
Piping Precautions
All piping should be supported independently of the coils. Swing joints or flexible fittings should be provided to absorb
expansion and contraction strains. Rigid piping reduces the effectiveness of unit vibration isolators.
Water supply should be connected so that the entering water is on the leaving air side of the coil.
Flush all field water piping prior to connection to water coils to remove debris.
Use wet cotton rags to cool valve bodies when soldering.
Open all valves (midway for hand valves, manually open on motorized valves) prior to soldering.
When soldering to bronze or brass, heat the piping while in the socket/cup and begin introducing the solder when the flux
boils rapidly. Avoid direct flame into the solder joint.
Heat can only be applied to the cup of the valve body for a minimal time before damage occurs (even with the use of wet
rags).
Avoid rapid quenching of solder joints as this will produce joints of inferior quality.
Connect all piping per accepted industry standards and observe all regulations governing installation of piping systems.
When all connections are complete the system must be pressure tested. Repair any solder joint leaks and gently tighten
any leaking valve packing nuts and piping accessories as required. Hydronic systems are not designed to hold pressurized
air and should only be tested with water.
CAUTION:
Low temperature ambient air or cold leaving air from DX coil can cause coil freeze-ups. A
freeze-stat (field supplied) or other means (glycol) should be incorporated to prevent coil freezing. The
manufacturer is not responsible for damage caused by these conditions. Failure to do so will result in
equipment and structure damage.
Water Coil Piping
Chilled / Hot water coil connections (1,2,4, 6 and 8 row) are 3/4 “ nominal (7/8” OD) copper on the 8/12 WH, 1” nominal (1-1/8
OD)on the 16/20 WH and 1-1/4 “ nominal (1-3/8” OD) copper on the 30/40/60/80 WH. When soldering to coil, use a heat sink
/ shield to prevent damage to the rubber grommets on the coil access panel. When all connections are complete, pressure test
the system with water. Repair any solder joint leaks and gently tighten any leaking valve packing nuts and piping accessories
as required.After system has been proven leak free, all lines and valve control packages must be insulated to prevent conden-
sate drippage or insulated as specified on the building plans.
CAUTION:
Many valve packages will not physically allow all components to fit over an auxiliary drain pan.
It is the installers responsibility to capture all condensation or insulate the piping to ensure adequate
condensation prevention.
Direct Expansion Coil Piping
Liquid and Suction lines should be sized in accordance to the outdoor manufacturer recommendation. Reduce if required at the
evaporator coil. Maximum line length and installation of oil transport traps and risers are to be determined by the installer per
accepted industry practices. The expansion valves provided from the manufacturer are bidirectional for cooling or heat pump
use. TXV check valves are internal on 08 - 20XH and external on 30 - 80XH due to flow limitations.
When all connections are complete, evacuate the system and pressure test with nitrogen. Repair any solder joint leaks as
required. Follow the charging recommendations of the outdoor manufacturer for final evacuation and charging.
It is also required that the suction line be adequately insulated to prevent condensation. Failure to follow this could result in
property damage.
CAUTION:
Expansion valve is refrigerant specific. Make sure the correct expansion valve (R-22 or
R-410A) is on the air handler in accordance to the refrigerant used in the outdoor condensing unit. The
manufacturer is not responsible for damage caused by improper matching. Failure to do so will result in
equipment damage.
CAUTION:
When connecting piping or valve kits to the air handler, do not bend or reposition the coil header
tubing for alignment purposes. This could cause a tubing fracture resulting in a water or refrigerant leak.
Failure to do so will result in equipment and structure damage.