5 table of engineering data (table 3), Installation, 1 location – Flowserve MP1 Sier-Bath User Manual
Page 14: 2 part assemblies, 4installation
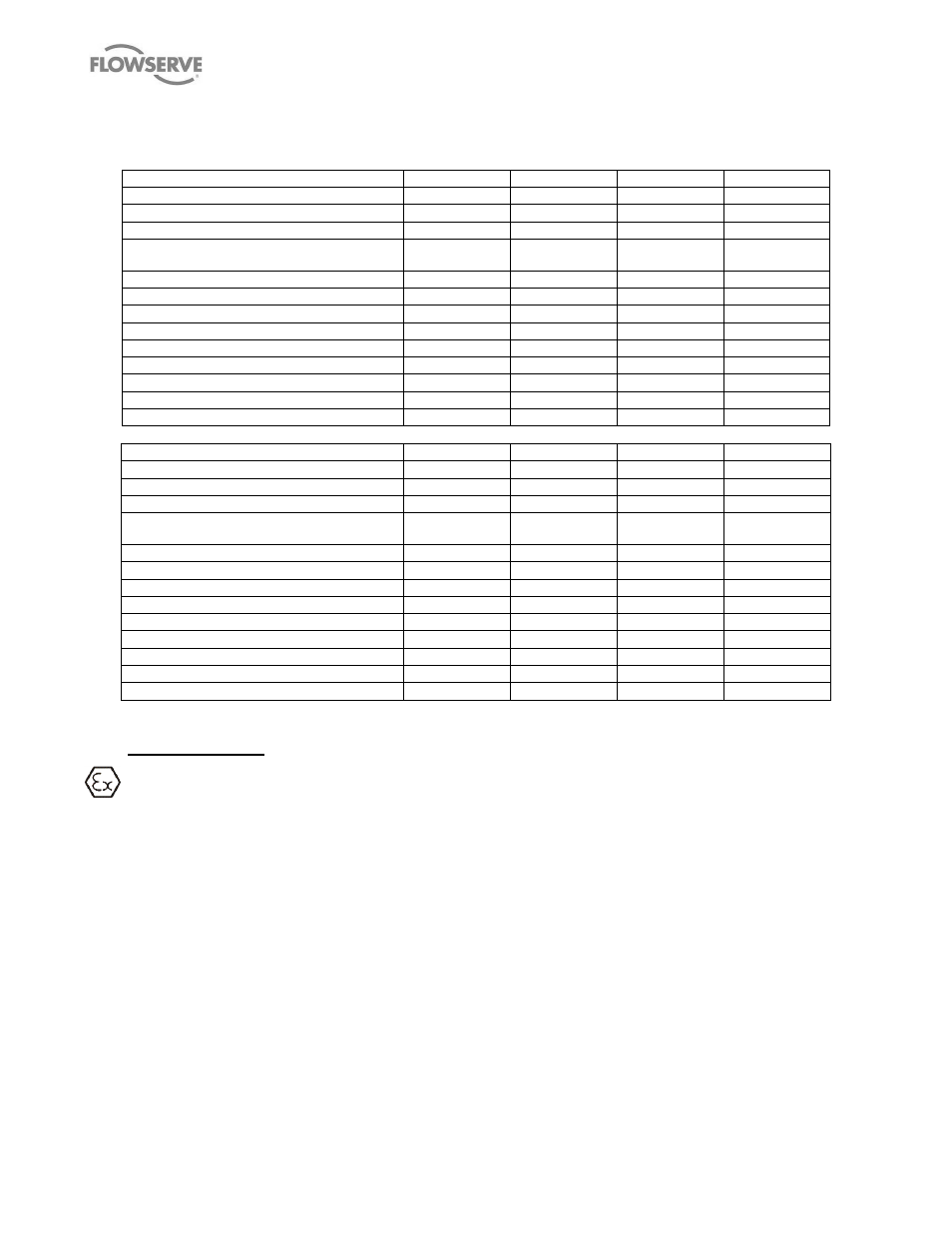
MP1 USER INSTRUCTIONS ENGLISH 26999958
– 10-12
Page 14 of 48
flowserve.com
3.5 Table of Engineering Data (Table 3)
Table 3 Engineering data
PUMP SIZE
MP1-150-200
MP1-275-255
MP1-275-355
MP1-380-305
SHAFT/SCREW DESIGN
INTEGRAL
INTEGRAL
INTEGRAL
INTEGRAL
STD SUCTION SIZE
6 in.- 600#
10 in.- 300#
10 in. - 300#
10 in. - 300#
STD DISCHARGE SIZE
4 in. - 600#
110 in. - 300#
10 in. - 300#
10 in. - 300#
STD OD CLEARANCE mm (in.)
0.30/0.45
(0.012/0.018)
0.51/0.76
(0.020/0.030)
0.51/0.76
(0.020/0.030)
0.51/0.76
(0.020/0.030)
APPROX PUMP WEIGHT kg (lb.)
658 (1450)
4490 (9900)
5900 (12990)
6591 (14500)
ROT ELEMENT WEIGHT kg (lb.)
136 (300)
508 (1120)
670 (1470)
990 (2175)
MOMENT OF INERTIA kgm^2 (lb·in
2)
0.250 (855)
3.670 (12 540)
3.670 (12 540)
2.356 (8050)
SHAFT DIAMETER @ COUPLING mm (in.)
53.98 (2.125)
92.08 (3.625)
92.08 (3.625)
92.08 (3.625)
SHAFT TAPER @ COUPLING mm/m (in/ft.)
60 (¾)
40 (½)
40 (½)
40 (½)
SHAFT DIAMETER @ ST BOX mm (in.)
73.0 (2.875)
130.2 (5.125)
130.2 (5.125)
130.2 (5.125)
NO OF SEALING CHAMBERS
4
4
4
4
OIL FILL TIMING GEAR HSG liters (qt.)
3.0 (3.2)
21 (22.2)
21 (22.2)
3.4 (3.6)
OIL FILL BEARING HSG liters (qt.)
0.25 (0.26)
8.5 (9.0)
8.5 (9.0)
1.5 (1.6)
PUMP SIZE
MP1-390-305
MP1-380-355
MP1-390-610
MP1-390-406
SHAFT/SCREW DESIGN
INTEGRAL
INTEGRAL
INTEGRAL
INTEGRAL
STD SUCTION SIZE
10 in. - 1500#
10 in. - 300#
16 in. - 300#
16 in. - 600#
STD DISCHARGE SIZE
8 in. - 1500#
10 in. - 300#
16 in. - 300#
16 in. - 600#
STD OD CLEARANCE mm (in.)
0.51/0.76
(0.020/0.030)
0.51/0.76
(0.020/0.030)
0.76/0.89
(0.030/0.035)
0.76/0.89
(0.030/0.035)
APPROX PUMP WEIGHT kg (lb.)
8300 (18 300)
6804 (15 000)
10 500 (23 148)
10 560 (23 280)
ROT ELEMENT WEIGHT kg (lb.)
975 (2150)
1157(2550)
1009(4583)
7612 (3460)
MOMENT OF INERTIA kgm^2 (lbs·in
2)
12.759 (43 600)
14.354 (49 050)
25.433 (86 909)
18.041 (61 650)
SHAFT DIAMETER @ COUPLING mm (in.)
92.08 (3.625)
92.08 (3.625)
111.13 (4.375)
111.13 (4.375)
SHAFT TAPER @ COUPLING mm/m (in/ft.)
40 (½)
60 (¾)
40 (1/2)
40 (½)
SHAFT DIAMETER @ ST BOX mm (in.)
130.2 (5.125)
130.2 (5.125)
209.5 (8.25)
209.5 (8.25)
NO OF SEALING CHAMBERS
4
4
4
4
OIL FILL TIMING GEAR HSG liters (qt.)
3.4 (3.6)
3.4 (3.6)
3.4 (3.6)
3.4 (3.6)
OIL FILL BEARING HSG liters (qt.)
1.5 (1.6)
1.5 (1.6)
1.5 (1.6)
1.5 (1.6)
4
INSTALLATION
Equipment operated in hazardous locations
must comply with the relevant explosion protection
regulations. See section
potentially explosive atmospheres.
The recommended order of operations to install a
pump skid is as follows:
a) Construct Foundation (Section 4.3)
b) Install Baseplate (Section 4.4)
c) Initial Alignment (Section 4.5)
d) Grouting (Section 4.6)
e) Fabrication and Installation of Piping (Section 4.7)
f) Final Shaft Alignment (Section 4.9)
g) Electrical Connections (Section 4.10)
h) Commissioning (Section 5.0)
4.1 Location
The pump should be located to allow room for access,
ventilation, maintenance and inspection and should be
as close as practicable to the supply of liquid to be
pumped. There should be ample room to allow the use
of an overhead crane or lifting device with sufficient
capacity to lift the heaviest part of the unit. Simple
suction and discharge piping layouts are desired.
Allow sufficient room to facilitate the back pull-out
feature.
Refer to the general arrangement drawing for the
pump set.
4.2 Part assemblies
Motors may be supplied loose on Twin Screw pumps,
typically on frame sizes 400 and above. It is the
responsibility of the installer to ensure that the motor is