3 direction of rotation – Flowserve MP1 Sier-Bath User Manual
Page 22
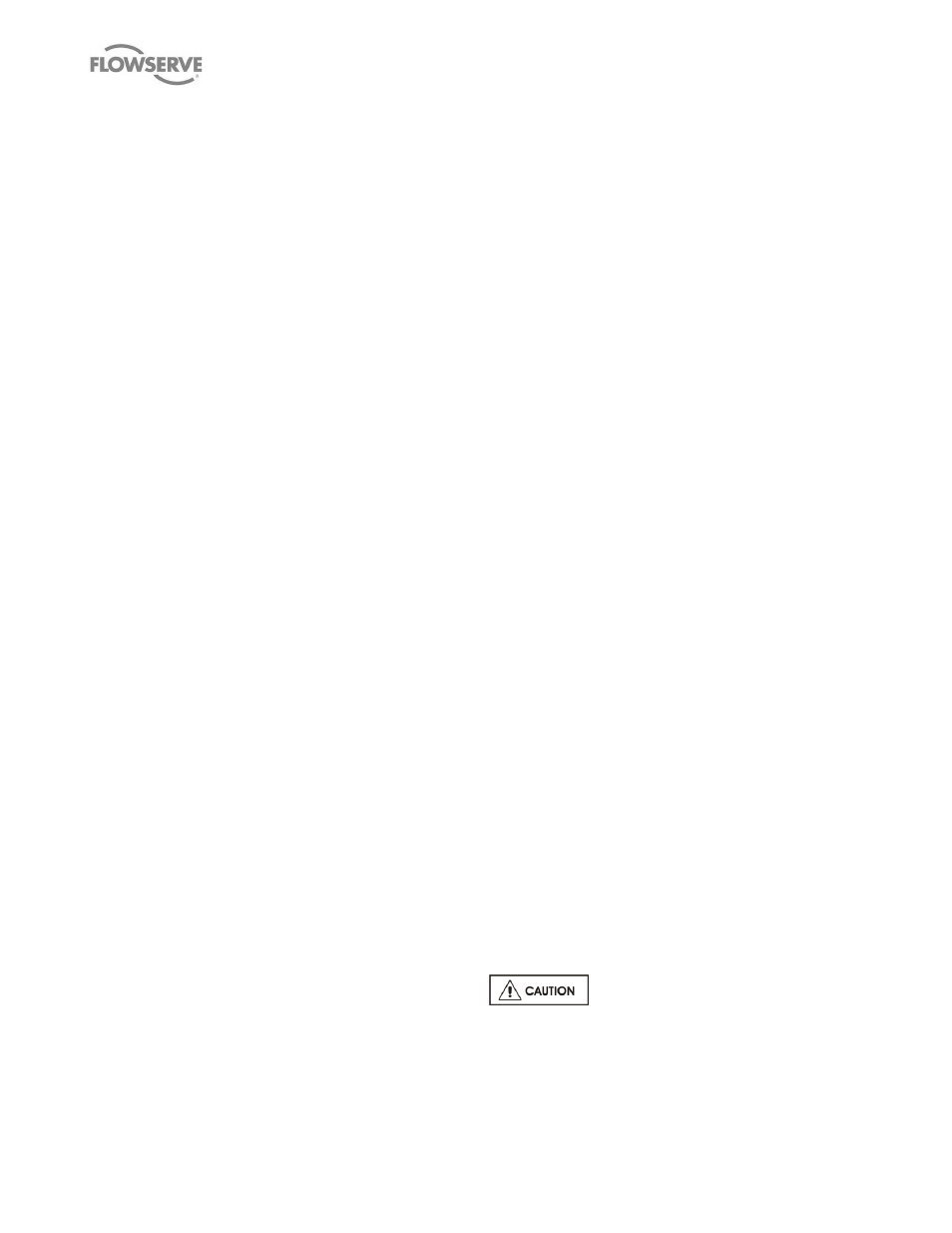
MP1 USER INSTRUCTIONS ENGLISH 26999958
– 10-12
Page 22 of 48
flowserve.com
Recommended oils are:
For normal running temperatures between 10
and
65
C (50
and 150
F):
Indoor installations or outdoor summer conditions with
ambient temperature of
–5
to 35
C (23
to 95
F).
Oil should meet ISO 3448 VG 220 (former AGMA
Standard 250.04 Lubricant No. 5), viscosity range 198
to 242 cSt at 40
C.
Typical oils per Column "A" in Section 5.2.1. Change
oil every six months or seasonally.
For winter running temperatures between
–18
and 38
C (0
and 100
F):
Cold Starting conditions with ambient temperatures of
–5
to 10
C (23
to 50
F).
Oil should meet ISO 3448 VG 68 (former AGMA
Standard 250.04 Lubricant No. 2EP), viscosity range
60 to 75 cSt at 40
C.
Typical oils per Column "B" in Section 5.2.1. Change
oil every 6 months or seasonally.
For high temperature service between 60
and 120
C (140
and 250
F):
Oil should meet ISO 3448 VG 460 (former AGMA
Standard 250.04 AGMA Lubricant No. 7), not
compounded, viscosity range 414 to 506 cSt at 40
C.
Typical oils per Column "C" in Section 5.2.1.
60
to 82
C (140
to 180
F) - change oil every four
months
82
to 104
C (180
to 220
F) - change oil every two
months
104
to 120
C (220
to 250
F) - change oil every
month
For temperatures above 120
C (250
F):
Same requirements as for high temperature service
between 60
and 120
C (140
and 250
F).
Initial start-up oil must be drained and replaced after
24 hours running time.
Change oil weekly.
Note: For some applications, depending on
conditions of service, separate shaft mounted lube
oil circulation/cooling system is required; check
the sectional drawing for recommended oils and
oil levels if this condition applies.
5.2.3 Oil levels
Check
the
Sectional,
Outline,
and
General
Arrangement drawings for bearing housing oil levels.
For simple Oil Splash Lubrication systems, not having
an external LOS, the oil levels are typically setup at the
lowest level of the gear teeth around the pitch diameter
on the gears housing end, and around the center of
the lowest bearing roller on the bearing housing end.
These levels are typically shown on the drawings as a
dimension below the shaft centreline, or with a mark
on the level oil gauge (if there is any), to facilitate the
operation of setting up the oil levels before starting the
pump to operation. Note that once the initial oil level is
set in the gear housing it should be adjusted after start
up following the directions in section 5.2.4. Pump
packages including an external LOS might not require
having an oil level setup.
5.2.4 Checking running oil level in gear housing
If the oil reservoir is filled to the level indicated on the
column gauge (when pump is at running speed),
ample lubrication will be provided for the timing gears
and bearings contained in the housing.
However, if field operating conditions (temperature,
etc.) vary considerably from standard, the level must
be checked internally to insure proper lubrication.
Follow the procedure as outlined below.
a) Remove the filler vent plug.
b) With the pump running at rated speed and
operating temperature, the timing gears should
pick up enough oil to create a fine mist throughout
the gear case. Too much oil will cause
overheating. Too little oil will cause gear and
bearing failure. Adjust oil level until fine mist is
present.
c) Replace vent filler and pipe plugs.
d) Repeat procedure periodically to ensure proper
lubrication and extended pump life.
5.3 Direction of rotation
Ensure the pump is given the same
rotation as the pump direction arrow cast on, or affixed
to, the pump casing.
To avoid dry running the pump must either be filled
with liquid or have the flexible coupling disconnected
before driver is switched on.