Flowserve WUC Worthington User Manual
Page 45
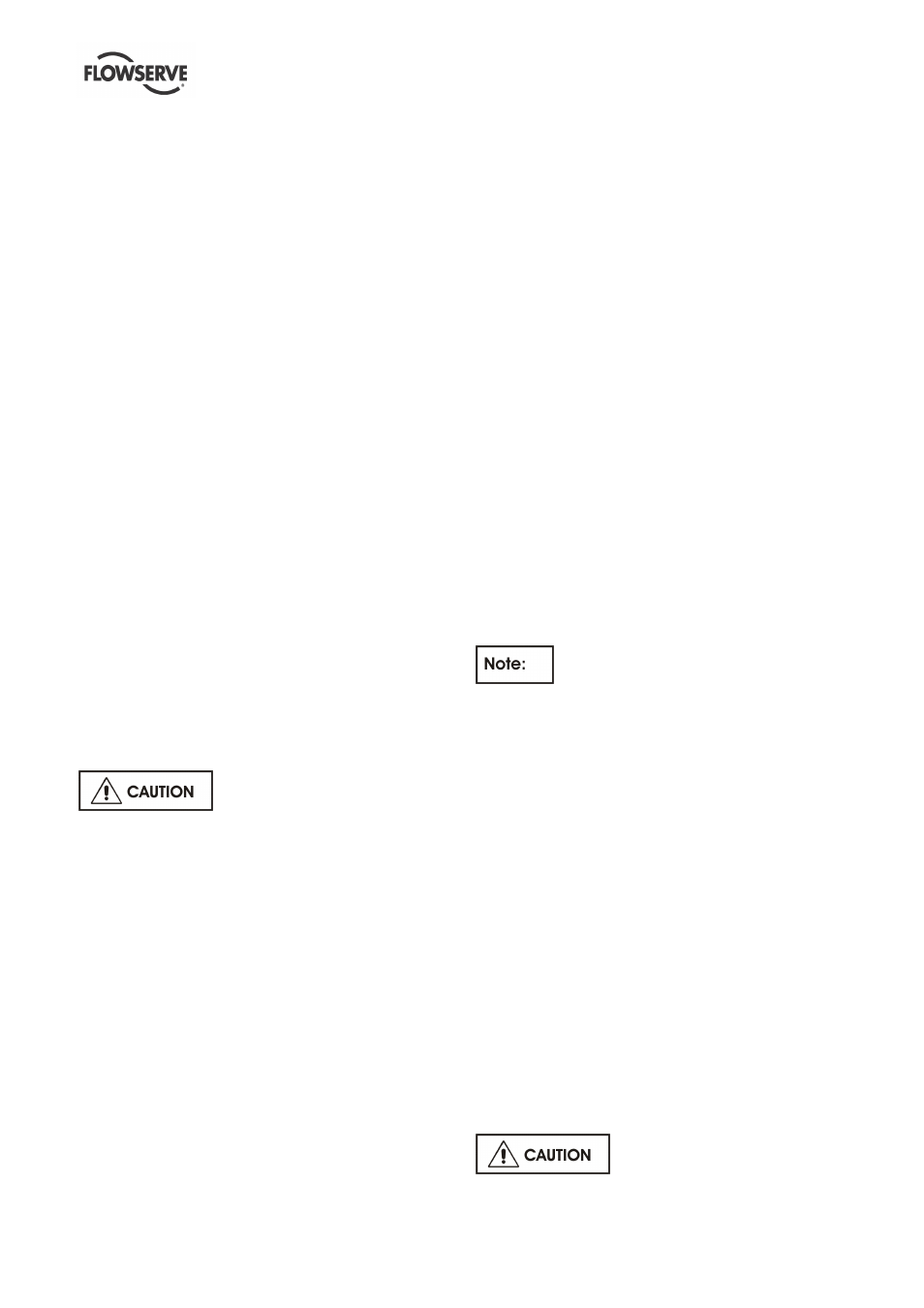
WUC USER INSTRUCTIONS ENGLISH - 07/14
Page 45 of 52
Actions after start up:
Check all connections to the seal gland and the
mechanical seal itself against leakage. It is usual that
at the seal faces a small leakage occurs after start
up, which decreases with the time of operation and
should stop after the seal is run in. Check the
temperature of the seal gland. I slight increase of
temperature may be observed during the run in
period. The mechanical seal is flushed by an API
Plan 13 and the temperature at the seal gland should
be max. 10 °C (18 °F) above the pumped liquid
temperature, unless otherwise specified by
mechanical seal supplier.
API Plan 13 provides self venting although a blinded
venting connection is forseen. This connection shall
be used by pumping flushing hydrocarbons at
ambiente temperatures and above. The seal
chamber is subjected to discharge pressure.
Plan 76 is suitable only for fluids, where no
condensation of the inner seal leakage or from the
collection system will occur.
Leakage from the inner mechanical seal is restricted
from escape by the containment seal and goes out
the containment seal vent. An orifice in the outlet line
of the collector restricts flow such that high leakage of
the inner seal will cause a pressure increase and
trigger the PSH set at a gauge pressure of 0.7 bar
(10 psi). The block valve in the outlet serves to isolate
the system for maintenance. It may also be used to
test the inner seal by closing while the pump is in
operation and noting the time/pressure buildup
relationship in the collector. If specified, drain
connection on the piping harness may be used to
inject nitrogen or other gas for the purpose of testing
the containment seal as well as for checking for any
liquid buildup.
Disassembly of the seal cartridge
is only allowed by authorized personal. Contact
Flowserve for any service of the mechanical seal. We
recommend to have a spare cartridge seal on stock
for easy replacement.
7.1.4 Dual Mechanical Seal pressurized with
gascoffer dam and API–Plan 53a
For temperatures below –50 °C (-58 °F) (cryogenic
service), a gascoffer dam shall always be used to
prevent the mechanical seal area from icing up. The
gascoffer dam consists of the de-gassing part
(chamber I) and the warm-up part (chamber II).
A throttle bushing between discharge head and
de-gassing chamber is provided, to reduce the
discharge pressure to suction pressure. By reducing
the pressure in the de-gassing chamber and the
simultaneous temperature rise, the pumped liquid will
partly vaporize.
The de-gassing chamber has to be connected to the
suction tank, by means of a balancing line, which
must be kept open to guarantee that only suction
pressure occurs.
The additional throttle bushing with a flinger between
chamber I and chamber II, is supplied for safety
reasons i.e. to exclude the eventual contact between
the medium and the barrier fluid.
In the event of seal failure, the leakage of the barrier
fluid will be collected in chamber II, to prevent any
contact with the pumped liquid. The loss of barrier
fluid will be detected by a level switch, mounted on
the seal reservoir. Chamber II is also provided with a
plugged drain.
The gascoffer dam is equipped with mechanical seals
in back to back arrangements, with API Plan 53a.
Advantages of the gascoffer dam design are:
a) no pollution of the pumped liquid by the barrier
fluid
b) only suction pressure is present at the inner
mechanical seal
c) mechanical seals are prevented from icing up
The mechanical seal requires no adjustment
anymore. Check if the mounting plates are already
swung out.
Actions after start up:
Check all connections to the seal gland and the
mechanical seal itself against leakage. Check the
temperature of the seal gland. I slight increase of
temperature may be observed during the run in
period.
Refer to mechanical seal drawing and
auxiliary piping drawing.
The pump is equipped with a dual mechanical seal in
back to back configuration.
Plan 53 pressurized dual seal systems are used in
services where no leakage to atmosphere can be
tolerated. A Plan 53a system consists of dual
mechanical seals with a liquid barrier fluid between
them. The barrier fluid is contained in a seal pot
which is pressurized to a pressure of approximately
1.5 bar (23 psi) greater than the pump seal chamber.
Inner seal leakage will be barrier fluid leakage into
the product. There will always be some leakage
(max.5 ml/hour).
The leakage rate is monitored by monitoring the seal
pot level. The gas coffer dam ensures that the
product is not contaminated with barrier fluid. The
seal pot pressure must be maintained at the proper
level. If the seal pot pressure drops, the system will
begin to operate like a Plan 52, or unpressurized dual
seal, which does not offer the same level of sealing
integrity. Specifically, the inner seal leakage direction
will be reversed and the barrier fluid will, over time,
become contaminated with the process fluid with the
problems that result, including possible seal failure.
Fill the seal system with a suitable
barrier buffer fluid (refer to lubrication table).