Flowserve MSS User Manual
Page 6
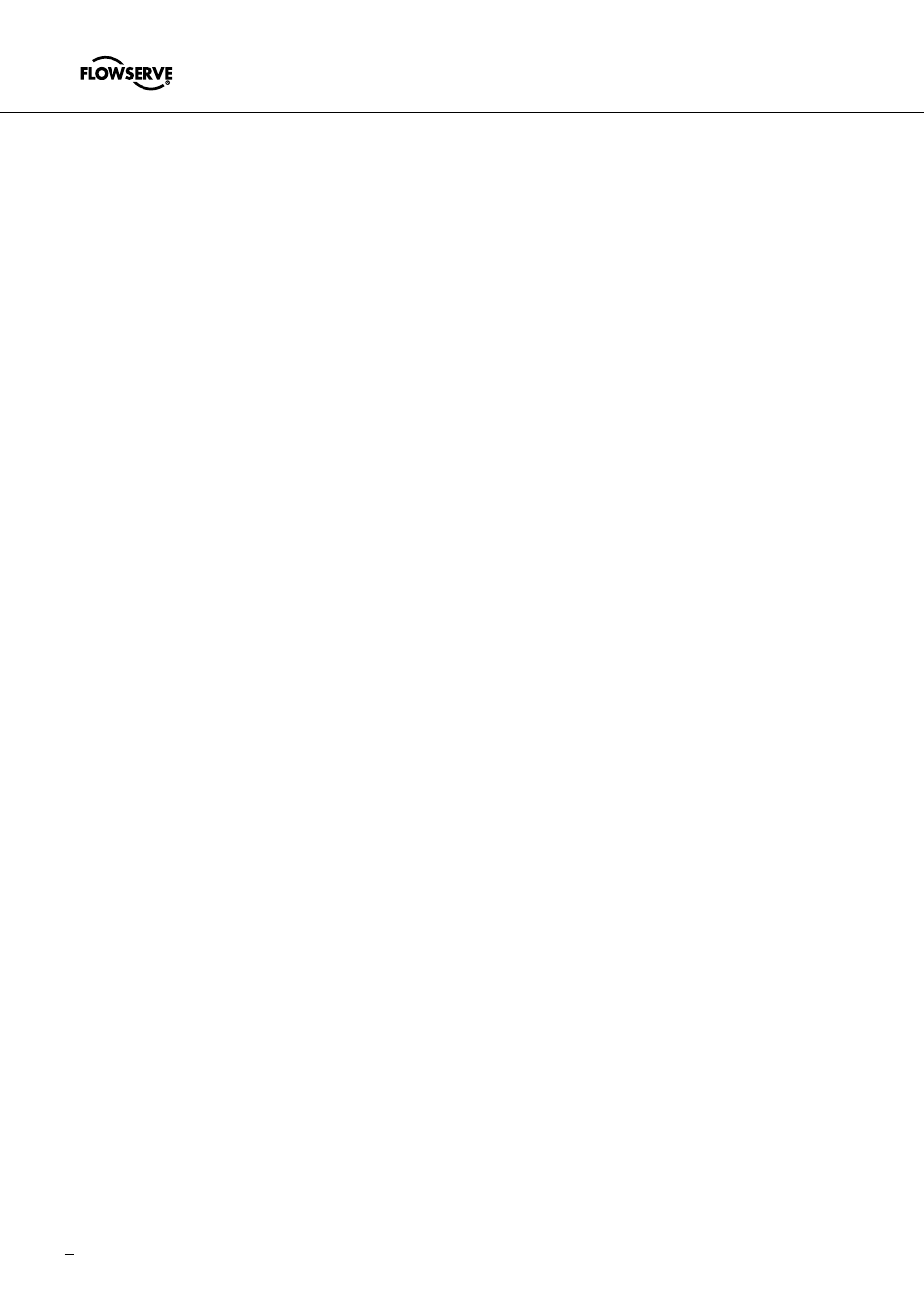
6
!
Ensure the highest degree of cleanness. Force must not be used to install the
seal. Use only suitable tools and devices.
!
The seal faces of the mechanical seal are important functional sections and may
not be damaged.
!
All functional and assembly areas for the secondary seals (e.g. O-rings) must be
dimensionally accurate, free of scratches and burrs, flash-free and rounded.
!
The fitting surfaces of the mechanical seal and the installation chamber must be
undamaged and dry. Ensure the highest degree of cleanness.
!
A thin coat of product-compatible grease (e. g. Molykote M55) is to be applied to
the sealing elements. Excess grease is to be avoided.
!
Depending on the installation direction, a lubricant, (e. g. Molykote D31R) or
PTFE spray without solvent, must be applied to the shaft or shaft sleeve.
!
The areas for the clamp-connections must remain free of grease, otherwise the
adhesive force will become inadequate for correct functioning
5.
Equipment Check
5..1 Follow plant safety regulations prior to equipment disassembly:
• lock out motor and valves.
• wear designated personal safety equipment.
• relieve any pressure in the system.
• consult plant MSDS files for hazardous material regulations.
5.. Dismantle the machine in accordance with the instructions from the machine manu-
facturer to reach the installation chamber for the mechanical seal.
5..3 Remove existing mechanical seal and gland or packing gland (follower flange) and
the first few rings of compression packing down to the lantern ring.
5..4 Make sure the shaft or sleeve in the seal shaft packing (P) area and the seal hous-
ing bore (B) and face are clean and free of burrs, cuts, dents or corrosion that might
cause leakage past the rotating face gasket or stationary face mounting O-rings.
5..5 Check equipment dimensions to ensure that they are within the dimensions shown
in Figures 1 and or 3. Critical dimensions include shaft or sleeve OD (A), seal
housing bore (B), and the distance to the first obstruction (J).
5..6 Check gland bolting to ensure that bolt size (D) and bolt circle (F) conform to the
dimensions shown in Figures or 3.