Troubleshooting, Worcester controls – Flowserve 51 Series Fire-Safe Valves User Manual
Page 10
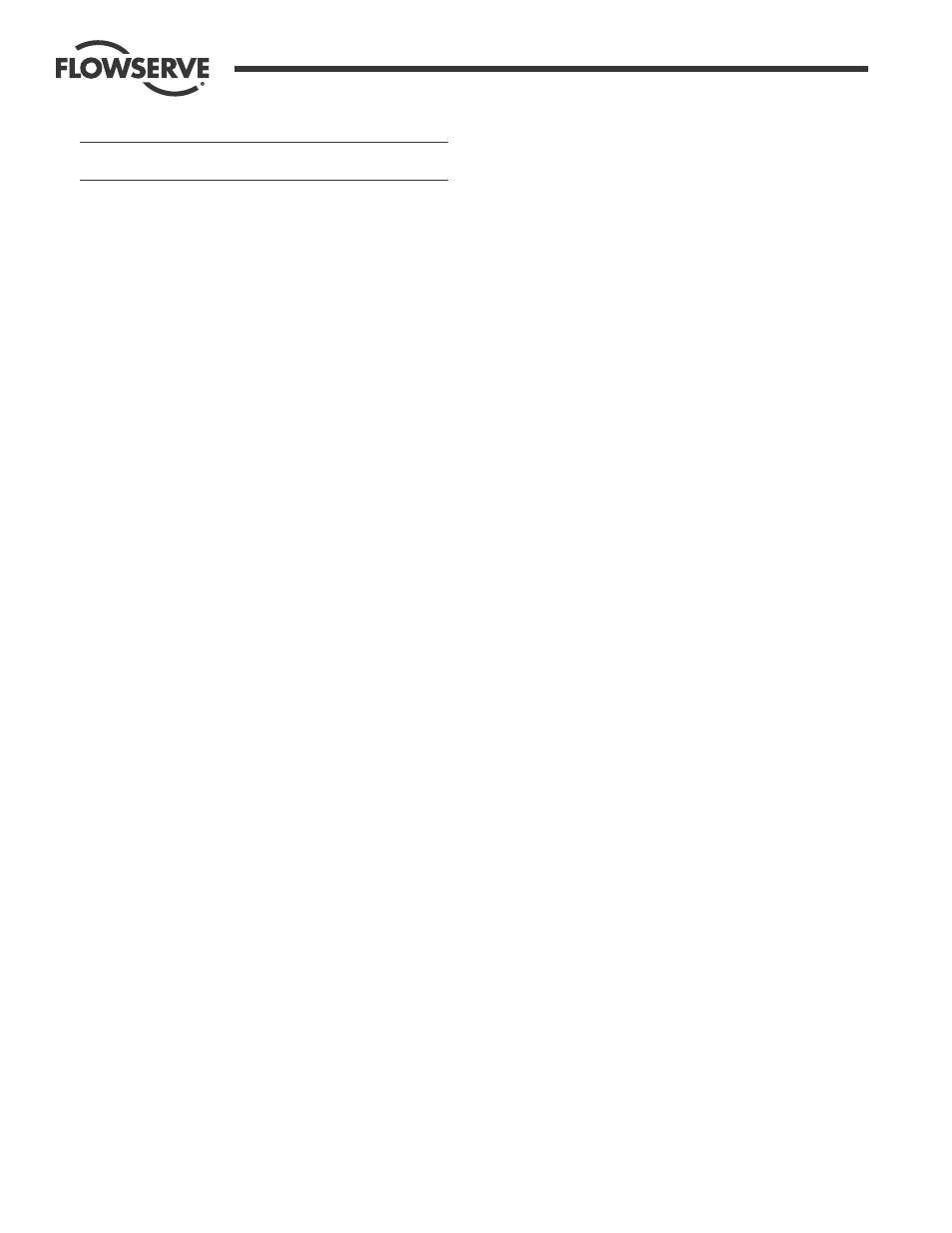
10
19406-H
CAUTION: Be sure that the fusible plug is reinstalled before
returning the actuator to service.
r. Mark Rebuild/Accessory Addition Label, if included in
repair kit, and apply to actuator.
TROUBLESHOOTING
1. If actuator does not function, check to ascertain:
a. That correct voltage is supplied to solenoid, if so equipped.
b. That sufficient air supply is available at inlet to actuator or
solenoid block. When checking supply pressure, place gage in
line at actuator or solenoid block inlet and monitor gage for
unexpected pressure drops.
c. That valve is free to rotate.
d. That speed control screw is loose (solenoid operated
actuators only). If screw is tightened all the way, actuator will
not operate.
2. If proper voltage and air pressure have been verified and valve is
free, proceed as follows:
a. Turn on signal voltage. Check the solenoid for clicking sound.
b. If no sound is detected:
1) Remove air pressure.
2) Carefully unscrew solenoid and solenoid stem from block.
3) Reapply signal voltage and observe solenoid plunger. If it
does not retract, replace solenoid.
c. If solenoid functions, remove solenoid valve block and place
on bench. Connect to reduced air supply (50 psig) and
correct voltage. Switch signal voltage and check air flow. Air
should flow out output port to actuator when solenoid is
energized.
d. If block and solenoid are operating correctly, remove the
actuator from the line.
e. Cycle actuator shaft with wrench to ascertain the actuator
shaft and/or pistons are not bound.
f. If actuator does not cycle properly, disassemble (per
Rebuilding Instructions) to ascertain:
1) That internal porting is clear of obstructions.
2) That piston guide rod with hole is on side opposite
nameplate (see Step b. on Page 9).
3) That unit is well lubricated and that there is no solidified
grease between the pinion and the piston racks.
a) If actuator has no lubrication, apply generous amount
of a #1 grease. If actuator is prepared for high or low
temperature operation, consult Flowserve for proper
lubricants.
b) If solidified grease between the pinion and the piston
racks is present, clean, dry, regrease and reassemble.
4) Verify that actuator pinion shaft and/or pistons are not
bound. If bound, reassemble per Rebuilding Instructions.
5) If unit exhibits excessive amounts of backlash, check
teeth on piston racks for wear. If worn, replace piston
assemblies.
6) Check for misplaced or broken springs. If springs are
broken, check body bore for scoring.
a) If springs are broken, replace springs. SPRINGS
SHOULD ALWAYS BE REPLACED IN COMPLETE
SETS.
b) If body bore is scored, replace it. Also, replace piston
O-rings (contained in repair kit).
3. If actuator is free, valve is free, and solenoid block (if used) is
shifting air properly, reassemble and remount the actuator to
valve and retest. If Sections 1 and 2 have been verified, the
actuator will function. If unit still fails to operate, consult
Flowserve.
4. If the actuator functions but exhibits leakage, or power loss
accompanied by leakage, proceed as follows:
a. Check voltage as in Section 1 above. Voltage must be within
10% of the specified voltage (low voltage will cause leakage
out of the back of the solenoid and burn out the coil).
b. Check air supply as in Section 2. Be certain that no sharp
pressure drops occur as unit is cycled due to insufficient flow
at required pressure.
c. If air supply and voltage are adequate, proceed as follows:
1) If leak is at solenoid exhaust port, replace the solenoid.
2) On spring return piston seal, leakage will show at the
breather port of the end cap. However, care should be
taken not to mistake intake and exhaust of ambient air
during cycling for leakage. If there is leakage at piston
seal, replace seals to prevent leakage.
NOTE: The most common problem encountered on the 39S actuator
is the improper replacement of the piston guide rod assembly with
the hole in it relative to the nameplate on the body.
Flow Control Division
Worcester Controls