Worcester controls – Flowserve 51 Series Fire-Safe Valves User Manual
Page 5
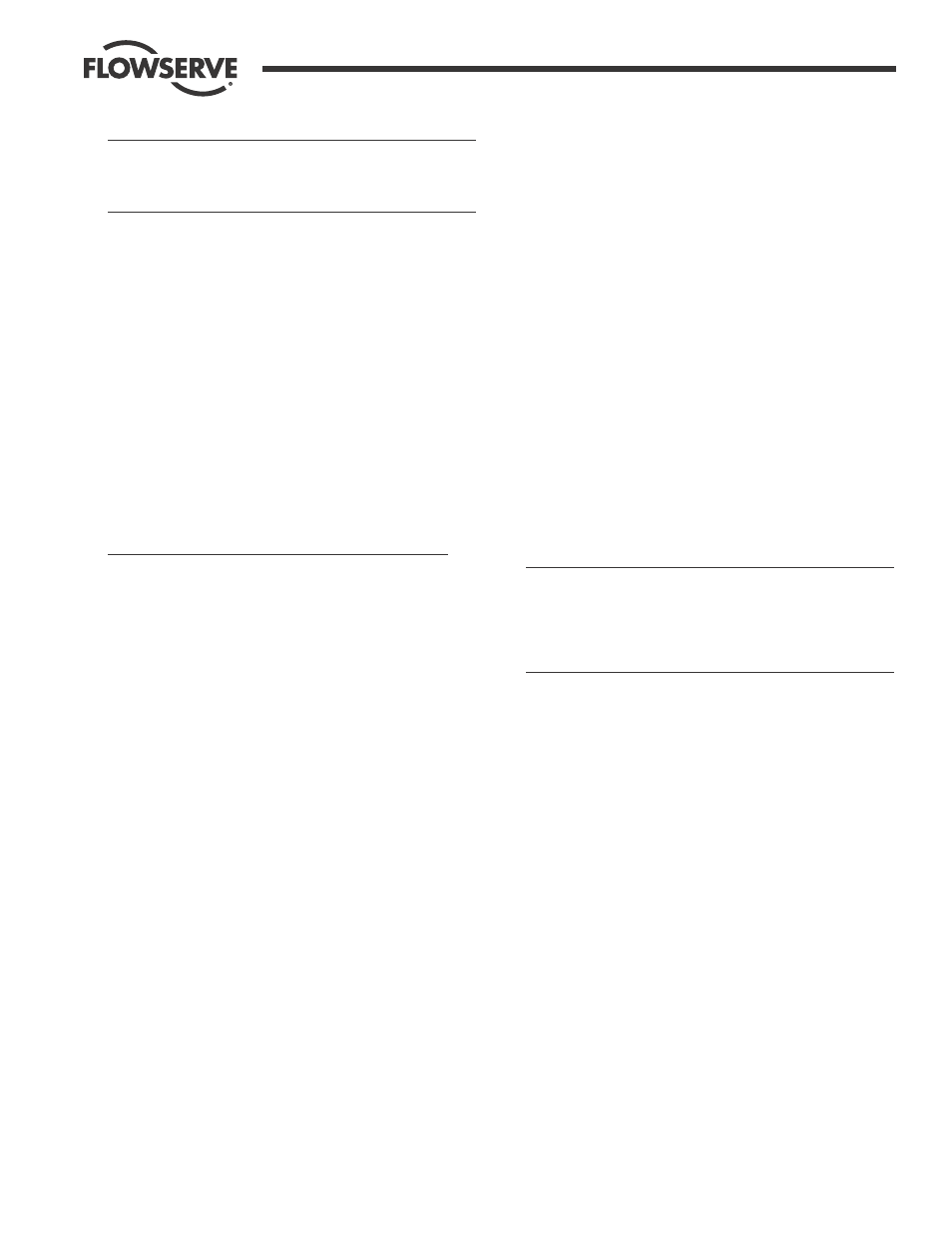
19406-H
5
Flow Control Division
Worcester Controls
CAUTION: Do not install 39S (spring return) models with air
connection in end cap or with integral solenoid vertical, if
water spray or rainfall can occur in area. End cap or solenoid
vent port will allow water to accumulate in spring chambers.
A. INSTALLATION:
NOTE: Sizes 10 - 35. Rev. R6 actuators may come with an ISO
locating ring (used for optional ISO mounting) shipped taped to
bottom of actuator.
The Series 39 Pneumatic Spring Return Actuator is factory
lubricated. For optimum operation, filtered and lubricated air is
recommended. Requirements are as follows:
1. Pressure: 60 psig minimum to 120 psig maximum.
2. Air
Connection:
1
/
8
NPT (Sizes 10-20),
1
/
4
NPT (Sizes 25-35),
1
/
4
NPT Port on integral solenoid block
3. Electrical Supply (On Solenoid Models Only): The solenoid coil
wattage and required amperage are as follows:
HOLDING
INRUSH
VOLTAGE
CURRENT
CURRENT
WATTS
24 VAC, 50/60 Hz
71 amps
1.18 amps
11
120 VAC, 50/60 Hz 14 amps
.23 amps
10
240 VAC, 50/60 Hz .07 amps
.11 amps
10
12 VDC
.81 amps
—
10
24 VDC
.41 amps
—
10
B. OPERATION
The actuated fire-safe valve is operated by energizing the solenoid
with the proper electrical supply, or by pressurizing the air inlet
with the required supply pressure. This opens the valve a full 90˚.
To completely close the valve, de-energize the solenoid, or
remove the supply pressure. Loss of electrical power, or air
pressure, or both, will result in the actuator closing the valve.
For solenoid operated actuators, only the speed of the spring
(closing) stroke is adjustable. This is accomplished by turning the
set screw contained in the exhaust nut (shipped separately in
envelope) which mounts directly to the end of the solenoid.
If the valve is subjected to a fire or high ambient temperature,
there is a fusible plug attached to the actuator which will melt out
and cause the valve to close automatically.
C. MAINTENANCE:
Check all fasteners periodically for proper tightness.
D. REBUILDING
NOTE: When rebuilding the actuator, please note that there are only
three (3) springs for each end cap on Rev. R2 and later actuators,
and eight (8) springs for each end cap on Rev. R1. This is done as a
benefit to the customer. When supply pressure drops due to peak
consumption levels, the actuator will still operate normally down to
an absolute minimum supply pressure of 50 psi.
For identification of all numbered parts discussed below, consult
exploded view of actuator.
INCLUDED IN ALL 39 ACTUATOR REPAIR KITS IS A
REBUILD/ACCESSORY ADDITION LABEL, WHICH IS TO BE
MARKED WITH A PERMANENT MARKER AND THEN APPLIED TO
THE ACTUATOR AFTER ACTUTOR HAS BEEN REPAIRED.
1. Actuator
Disassembly
a. Disconnect the air supply and electrical service to
actuator.
b. Remove the actuator and its mounting bracket from valve.
If the actuator uses a positioner, loosen the set screws in
the coupling between the valve and actuator. (See Caution
note below.)
CAUTION: Ball valves can trap pressurized media in the cavity.
Isolate the piping system in which the actuator/valve assembly
is mounted and relieve any pressure on the valve. Note
orientation of actuator to valve. It is important that the actuator
be remounted in the same position to assure fail-safe
operation.
c. Remove the actuator bracket from the actuator to begin
repair. Remove positioner (if used) by loosening
positioner coupling set screws, removing positioner
bracket screws and hose connections.
d. It is not necessary to remove solenoid control block (7) if
any, to rebuild actuator. However, if it becomes necessary
to remove the block, begin by removing the solenoid
block bolts (8E). Use care to retain the solenoid block
gasket (9).
e. Each end cap (5A, 5B) is aligned onto the body (1) over a
“foolproof pin”. This ensures that the end caps can only
be assembled to their respective end of the actuator.
Remove all four metric screws (5C) from and remove
both end caps. For Rev. R1 and R3 thru R6 actuators,
remove the two bearings (6A) and O-rings (15A and 15B)
from each end cap. Note that for Rev. 2 models with top-
hat style bearings (6C), the bearings and particularly the
retaining washers (16) in each end cap should not be
disturbed during O-ring seal replacement, as they are not
included in the rebuilding kit.