Worcester controls – Flowserve 51 Series Fire-Safe Valves User Manual
Page 3
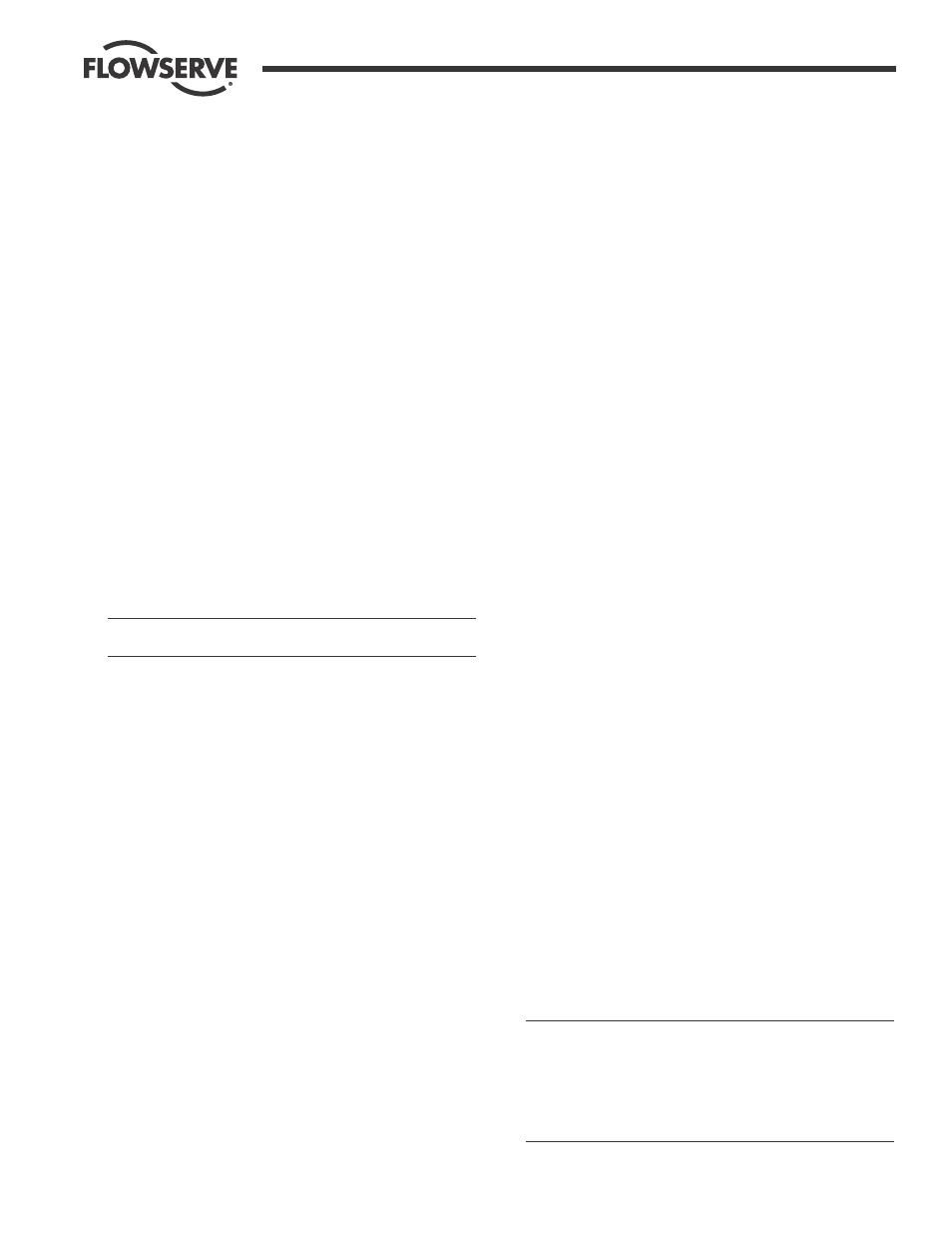
19406-H
3
-
Relieve the line pressure. Operate the valve prior to
attempting removal from line.
-
Place valve in half-open position and flush the line to remove
any hazardous material from valve.
-
All persons involved in the removal and disassembly of the
valve should wear the proper protective clothing such as face
shield, gloves, apron, etc.
A standard repair kit can be ordered which contains all necessary
seats and seals to rebuild the valve. To order the repair kit (RK),
specify the valve size and the R (Revision) number of valve, or the
“P”, “T”, “C” or similar number, as found o the valve nameplate. If
valve body is stainless steel, place a “6” after valve size in repair
kit ordering code. Use the following format to order:
Valve Size
MRK 51 Revision, P, T, C, etc. #
The seats and seals included in this kit are the only ones
approved for the Factory Mutual fire-safe valve. Please do not use
any others for rebuilding this valve. Doing so will void the Factory
Mutual approval.
If spare parts are necessary, include the complete valve code as
given on the valve nameplate and then the part(s) that is (are)
being ordered.
For part description and valve assembly, refer to the appropriate
parts list and exploded views.
CAUTION: Exercise caution that sealing and ball surfaces are
not damaged during disassembly, cleaning or reassembly.
1
/
2
"-2" 51/52 Valves:
1. Disassembly Of Valve
a. Place valve in open position, unscrew all flange bolts and
remove valve from line.
b. Place valve with end plug up on a clean surface. Secure
by clamping or bolting.
c. Unscrew end plug. Set aside. If the body seal was not
removed with the end plug, remove it form the valve and
discard. Remove and discard near seat.
NOTE: If required, end plug assembly/disassembly tools are available
from Flowserve.
d. Place valve in the closed position and remove the ball.
2. Removing Stem Assembly
a. Remove top nut, lockwasher and one-piece handle/stop, if
you have a manual valve. NOTE: This step is not
applicable to valves with self-locking stem nut.
b. Remove retaining or self-locking stem nut. Use a wrench
to prevent stem from turning.
c. Remove and discard Belleville washers. Push stem into
ball cavity and remove. On the
1
/
2
" size, the far seat must
be removed before pushing stem into cavity.
d. Remove and discard stem seal, stem seal protector and
thrust bearings, which may be on the stem or in body
stem cavity, and far seat. Retain the follower.
3"-4" 51/52 Valves:
3. Disassembly of Valve:
a. Place valve in open position, unscrew all flange bolts and
remove valve from line.
b. With valve in closed position, remove end plug retaining
screws.
c. Remove end plug. If necessary, drive end plug from valve,
using wooden drift applied to ball.
d. Remove body seal, ball and seats. Discard seats and body
seal.
4. Removing Stem Assembly:
a. Remove handle assembly (if any) by loosening handle
screw.
b. Remove retaining nut. Prevent stem from rotating by
holding stem with wrench.
c. Remove stop or valve stem spacer (actuated valves).
Remove and discard Belleville washer(s), if any. Remove
and retain the follower.
d. Push stem into body cavity and remove. Remove and
discard stem seal and thrust bearing. Remove and retain
stem centering washer.
5. Visual
Inspection
Important areas for visual inspection are:
a. The ball and the surfaces against which the seats and
seals are installed should be undamaged, clean and free
of pit marks and scratches. Light marring from the action
of the ball against the seats is normal and will not affect
the operation of the valve. Flaws which can be seen but
barely detected with fingertips are acceptable.
b. The stem and body surfaces that the thrust bearing(s)
and stem seal(s) contact must be undamaged, clean, and
should be free of pit marks and scratches.
6. Reassembly (Refer to exploded views on pages 6 and 7)
CAUTION: Care must be used when handling graphite stem seals
and body seals. These parts can be easily damaged by squeezing
the O.D. of the seal. Parts are to be handled on the flat surfaces
rather then the O.D. These parts will not work if they are cracked
or broken. Light flaking of the material is acceptable. If resistance
is encountered when installing stem seals over the stem, use
follower to gently push the stem seal down.
Flow Control Division
Worcester Controls