Repair procedures – Flowserve Edward Cast Steel Bolted Bonnet Valves User Manual
Page 7
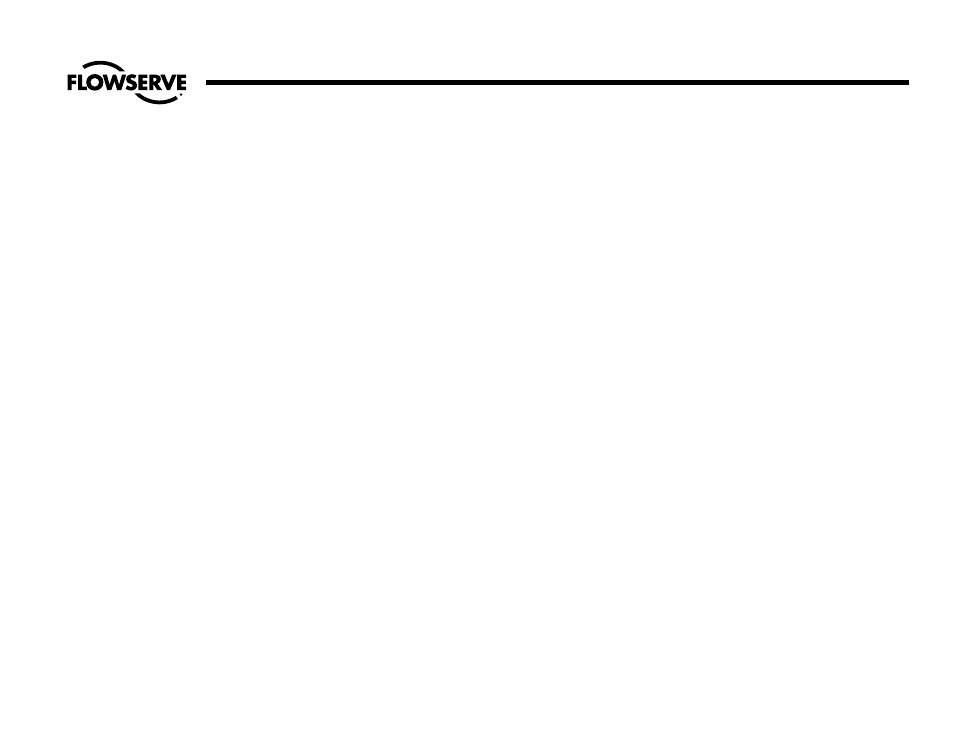
7
Flow Control Division
Edward Valves
Repair Procedures
BODY BORE GUIDE RIB REPAIR
Where more than one guide rib is
involved, each rib should be preheated
and welded before proceeding to the next.
1. Prior to any cutting or welding opera-
tions being performed on the valve, it is
necessary that adequate seat joint pro-
tection be provided and some means of
insurance against getting chips, weld
spatter or other foreign matter into the
pipe line, if the valve is permanently
mounted. A round piece of sheet metal
placed over the seat and taped in place
will furnish adequate protection.
2. Chip out the defective area in the body,
being careful to remove the affected
portion to its end, inside the casting,
and to thoroughly clean it away.
3. With a small hand grinder, grind the
chipped area smooth.
4. Heat the body area adjacent to the
guide rib to 200° Fahrenheit. This can
be done locally with an oxyacetylene
torch.
5. Select the proper welding rod to suit the
body material maximum size rod is rec-
ommended here). See Table B for weld
rod recommendations.
If replacing stainless steel inlay, use
AWS 5.4 E309L stainless electrodes.
6. The welding should be started at the
bottom so as to create a small shelf,
and then proceeded up the guide rib.
Lay the weld in thin, even layers, peen-
ing each layer before proceeding with
the next, and being careful to maintain
a temperature of 200° Fahrenheit in the
area being repaired. Peening the bead
actually stretches it and counteracts its
tendency to contract and shrink as it
cools. The last layer of weld must over-
lap onto the sound metal to ensure a
weld without an undercut at the edges.
The overlapping should be done along
this edge by using a welding rod of
1/8" maximum diameter. The last layer
should bring the height of the welded
area up to 1/16" above the original
surface, as checked with a straight edge
along the body bore.
For this type of weld repair, it is recom-
mended that the last layer be pounded
while still hot with the flat face of a ham-
mer. Thermal stress relieving is not
recommended.
7. With a hand grinder, rough grind the
welded surface to within about .010” of
the finished surface. The edges of the
guide ribs should be rounded off
smooth. Check the progress of the rough
grinding by using a straight edge and
feeler gages. As the bonnet bore and
guide rib approach alignment, a light
can be placed on one side of the
straight edge and the high spots in the
guide rib observed on the other. Where
a check valve or stop-check (non-return)
body is being repaired, the progress of
the finishing cuts can also be measured
by slipping some long pieces of shim
stock between the I.D. of the body
guide ribs and the O.D. of the disk-pis-
ton assembly, which has been placed
centrally in position on the seat joint. A
shim should pass around the disk at all
three guide ribs with equal clearance.
The disk-piston assembly should also be
moved up and down to make sure that
it is free.
It is recommended that where guide rib
repairs have been made, the seat and
disk joint be checked for distortion and
relapped, if necessary.
SEAT AND DISK REPAIRS
A valve seat joint will require repairing in
any instance where the seating surface
permits a leak because it has been altered
from the original state in which it was
shipped from the factory; where corrosion
has set in to cause pit marks on the seating
surfaces of either the body or disk, where
the seat has become distorted because of
an abnormal heating condition; or, where
a groove has been formed on the seat or
disk by closing the valve against a foreign
body. Verification of such a faulty condi-
tion may be obtained by a seat bluing test
or by careful visual examination.
The hard surfaced seats in these bolted
bonnet valves are not easily scored, but
where reconditioning is necessary, the fol-
lowing points should be observed:
Where an indention or pit marks on the
valve seat joint are deep (.010 or greater),
a cast iron lap with suitable lapping com-
pound will speed up repair. The cast iron
lap should be closely guided in the body
bore during the lapping.
Lap first with the cast iron lap and finish
with the valve disk, which has been
reground or relapped, if necessary. For
initial lapping, use Clover compound “A”,
Norton 320 mixed with olive oil or sperm