Maintenance, Worcester controls – Flowserve 10 ACCESS I Worcester Controls User Manual
Page 7
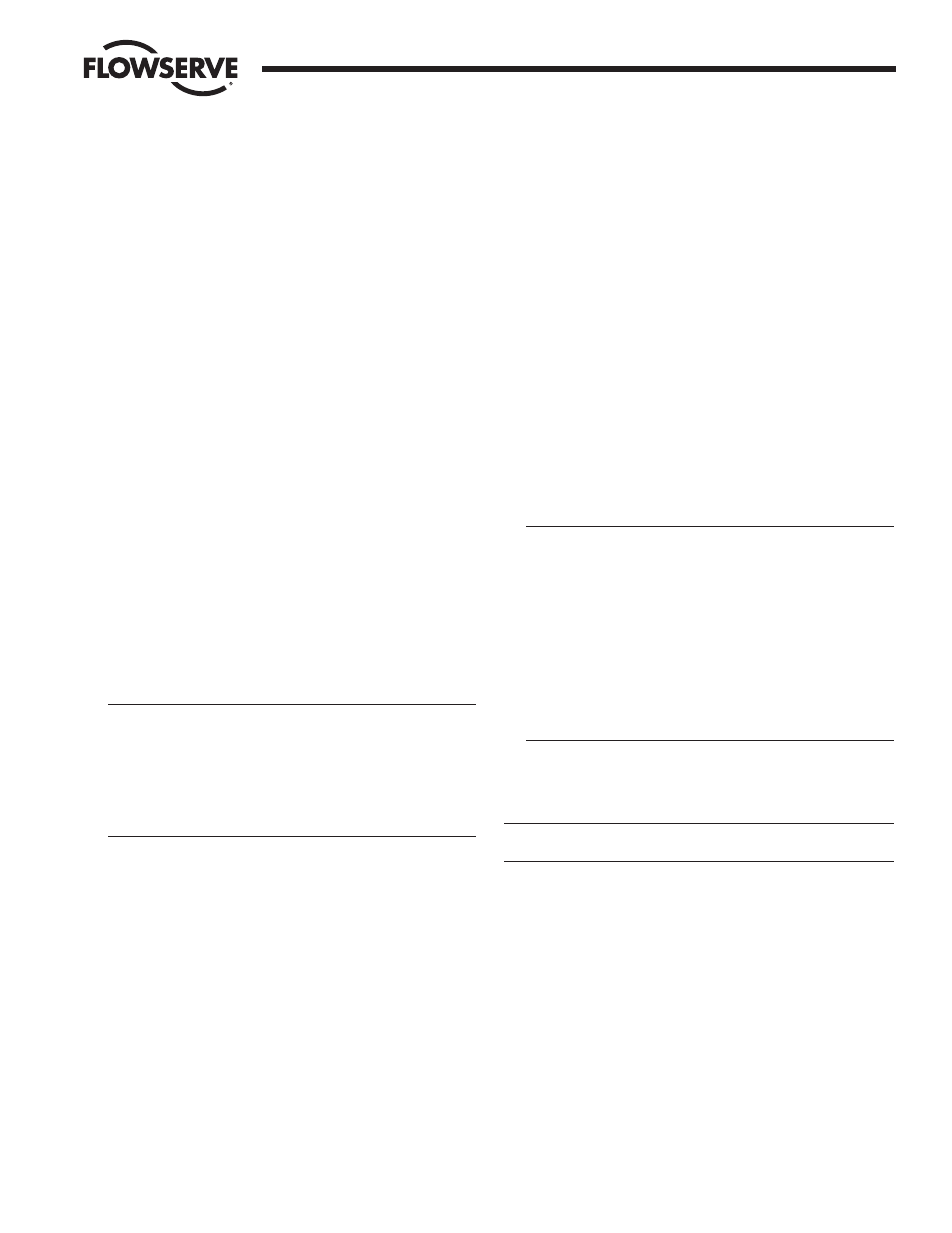
WCAIM2028
10, 15, 20 ACCESS I and 10-40 Access M 39 Actuators Intrinsically Safe
7
The unit has two independently adjustable speed control screws
which can be used to adjust the speed of operation for the
opening and/or closing stroke (see figure 4). If the speed control
screws are too tight, the unit will fail to operate.
NOTE: Speed control screws are shipped from the factory in the
full-open position.
B. Spring-Return with Control Block - Air is supplied to the
1
/
4
" NPT
port on the block. When the solenoid is energized, the spring-
loaded plunger is withdrawn, allowing the supply air to shift the
spring-loaded spool within the block, which opens the supply
path to the center chamber of the actuator. Air from the end
chambers of the actuator is allowed to pass through the block
and exhaust to atmosphere.
When the solenoid is de-energized, the spring-loaded plunger
blocks the flow of air to the spool within the block and the spring-
loaded spool returns to a position which allows air from the
center chamber of the actuator to pass through the block and
exhaust to atmosphere as the actuator is cycled by the springs in
the end chambers of the actuator. The end chambers are
exhausted to atmosphere at all times.
The actuator is fail-safe. That is, it will return to its de-energized
position upon electrical or pneumatic failure.
The unit has one speed control screw, which can be used to
adjust the speed of operation for the closing stroke (on a FAIL-
CLOSED unit) or opening stroke on a fail open unit, and one port
plugged with a red plastic plug (see figure 4). If the speed control
screw is too tight, the unit will fail to operate.
Note: Speed control screws are shipped from factory in the full-
open position.
CAUTIONS: If converting a double-acting actuator to a spring-
return actuator or vice-versa, be sure the correct control block
gasket is used and properly installed (see figure 5 and actuator
exploded view). Do not apply any grease to gasket, it must be
installed dry.
Be sure red plastic plug is installed in plugged port (see figure
4) for spring-return actuators.
C. Double-Acting with No Solenoid and No Control Block - Air is
supplied to the
1
/
4
" NPT port on the air connection block to the
center chamber of the actuator through a remotely mounted four-
way solenoid (or similar supply system). The other
1
/
4
" NPT port
on the air connection block to the end chambers is exhausted
through solenoid (or similar supply system). When solenoid is
de-energized (energized) supply air is now supplied to end
chambers and center chamber is simultaneously exhausted
through solenoid.
D. Spring-Return with No Solenoid and No Control Block - Air is
supplied to the
1
/
4
" NPT port on the air connection block to the
center chamber of the actuator through a remotely mounted
solenoid (or similar supply system). The other
1
/
4
" NPT port on
the air connection block is the exhaust port for the end
chambers and may be exhausted to atmosphere or through
customer’s system.
When the remotely-mounted solenoid (or similar supply system)
blocks the supply air to the center chamber of the actuator, a
means must be supplied to exhaust this chamber and the actuator
is cycled by the springs in the end chambers.
E. Stroke
Times
For stroke times of the ACCESS I and ACCESS M Series 39
actuators with solenoid and control block, consult factory. Times
will be measured in seconds and will represent average times
under 50% load conditions with an air supply pressure of 80
psig. Times will be per stroke for double-acting actuators. For
spring-return actuators, the opening stroke times may be slightly
longer; stroke times for the closing (spring) stroke will be
dependent upon the number of springs used.
Cycle times for customer air supply systems will be dependent
upon customer equipment.
F. Manual
Operation
In the event of air failure, the ACCESS I and ACCESS M Series 39
actuators can be cycled manually. This is accomplished by
applying a wrench to the exposed top shaft of the actuator and
turning it in the desired direction.
a WARNING: Care must be taken to ensure that the actuator is
not operated automatically while manual operation is being
performed.
If a routine cycle check is to be performed on an actuator with a
control block, the actuator can be cycled manually by shifting
the spool valve within the control block. This can be done by
pushing the override button in the control block (see figure 4 on
page 6 for location of button). Care must be taken to hold the
spool valve in the desired position until the actuator has
cycled. Provided the air supply is still on, the actuator will
cycle to its original position as soon as the manually applied
pressure on the override button is released.
MAINTENANCE
CAUTION: The actuator must be isolated both pneumatically and
electrically before any maintenance activity is begun.
Periodic checks should be performed to make certain that all
fasteners remain tight. Care should be taken when tightening the end
cap retaining bolts since these fasteners are METRIC. All other
fasteners are UNIFIED IMPERIAL.
All actuators are supplied with sufficient lubrication for their normal
working life. If required, recommended lubrication for all standard
actuators is a #1 grease.
Depending upon the conditions under which the actuator must work,
such as extended-duty, non-compatible operating media or abnormal
operating conditions, periodic replacement of internal seals is
recommended. Repair kits containing all necessary seals can be
obtained through any authorized Flowserve Worcester/McCANNA
Controls distributor.
Flow Control
Worcester Controls