5 manual operation, 6 maintenance and troubleshooting, 1 general – Flowserve 75 Series DeviceNet Interface User Manual
Page 5: 2 isolate the problem, 3 switch/cam settings
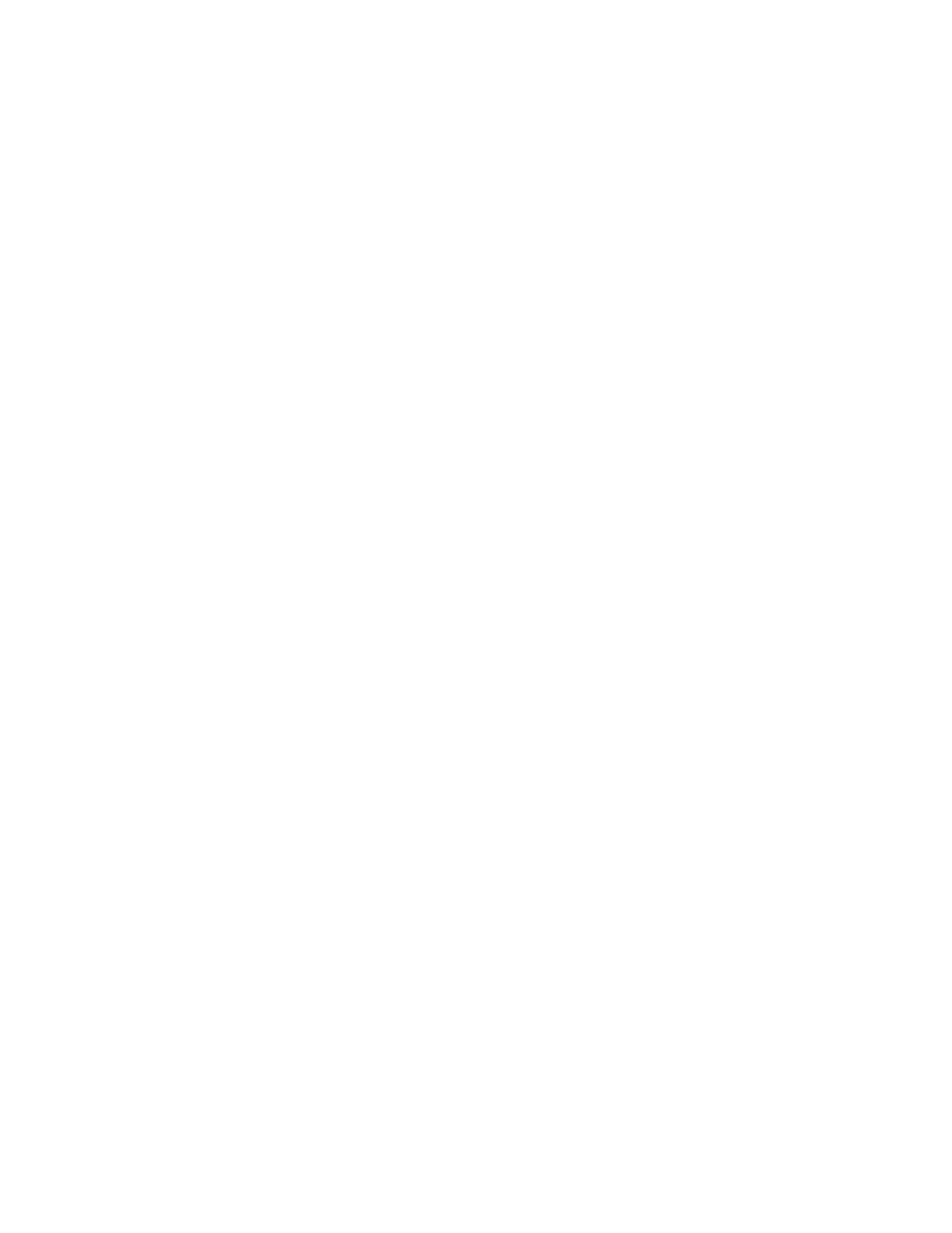
FCD WCAIM2068-00
DeviceNet Interface for Series 75 Electric Valve Actuator
5
d. All coil adjustment is done in small increments of .015"
or less.
e. Additional adjustment may be done by moving mount-
ing plate toward/away from actuator shaft.
B. Heater and Thermostat
NOTE: Heater and thermostat option requires no adjusting. If
defects are found, notify factory.
The thermostat will close its contacts at 80°F (power on) and
open its contacts at 95°F (power off).
C. Drain/Breather (V53) Option
If actuator is equipped with drain/breather at bottom of base,
actuator must be installed in an upright position for drain to
operate properly.
5 Manual Operation
a
CAUTION: Disconnect actuator from power supply. If power
is not off, motor may start when cam moves from limit
switch.
Pull the declutching knob all the way up and hold. Apply wrench to
exposed flats on actuator shaft and rotate to desired position. To
reengage, return shaft to original position of disengagement and
release declutch knob.
NOTE: Actuator should be manually operated only over the range for
which it is set up to operate electrically. Operation beyond this range
will totally disrupt indexing.
6 Maintenance and
Troubleshooting
a
CAUTION: The PLC/Process Controller logic should never
set bits 5 and 6 on (1) at the same time in output word 1.
These bits control actuator CCW and CW rotation, and dam-
age to the relay interface module and motors will result if
these bits are set on (1) simultaneously. The output word 1
corresponds to an actuator at Address 1.
The Series 75 DeviceNet electric valve actuator requires no regular
maintenance. Should the unit fail to operate, however, the following
are hints for troubleshooting. If the unit still fails to operate, consult
the factory.
6.1 General
If the actuator does not operate, check that:
1. The valve is free to move. This can be done as described in
Section 5.
2. The actuator is correct size.
3. Correct voltage is supplied to terminals 1 and 2.
4. Correct voltage is supplied to the DeviceNet bus (24 VDC).
5. The DeviceNet bus is properly terminated with a 120 ohm resis-
tor between CanL and CanH.
6. The proper communication baud rate and MACID (address) has
been selected.
7. LEDs D1 & D2 on the DeviceNet board are both on and green.
8. The actuator is wired correctly, per Figures 3, 4 and 5.
NOTE: If the above checklist is OK, proceed to Section 6.2.
6.2 Isolate the Problem
1. Determine if the problem is with the Switch/Cam settings
(Section 6.3).
2. Determine if the problem is with the Motor(s)/Cam Settings
(Section 6.4).
3. Determine if the problem is with the DeviceNet board
(Section 6.5).
The actuator, when received from factory, will be in the full CCW
(open) 90° position and should only respond to a CW (close)
DeviceNet command. If a new actuator does not respond to a CW
or CCW command, the problem could be with the cam adjustments,
defective motor(s) or defective DeviceNet board. Ensure that Switch
1 is not being tripped when a CW command is given and that Switch
2 is not tripped when a CCW command is given. If the actuator
does not rotate CW or CCW when a respective command is given,
proceed to Section 6.4.
6.3 Switch/Cam settings
Refer to Figures 1 and 2
Switch/cams 1 & 2 control the CW and CCW, respectively, end of
travel of the actuator.
The cams have been factory set for:
Switch/cam 1 CW: 0° (stops actuator CW rotation)
Switch/cam 2 CCW: 90° (stops actuator CCW rotation)
Switch/cam 3: 2-3° (CW indication to DeviceNet board)
Switch/cam 4: 87-88° (CCW indication to DeviceNet board)
The switches can only be adjusted by operating the actuator
motor(s) and setting the cams per above settings. If the switches
and cams require adjusting, go to Section 6.4.