Operating instructions -2, Applications data -2, Thickness range: .035 in. to 3 in -2 – Hypertherm PAC500 Water Injection Plasma Cutting System User Manual
Page 33: Operating instructions -2 applications data -2, Operating instructions, Applications data
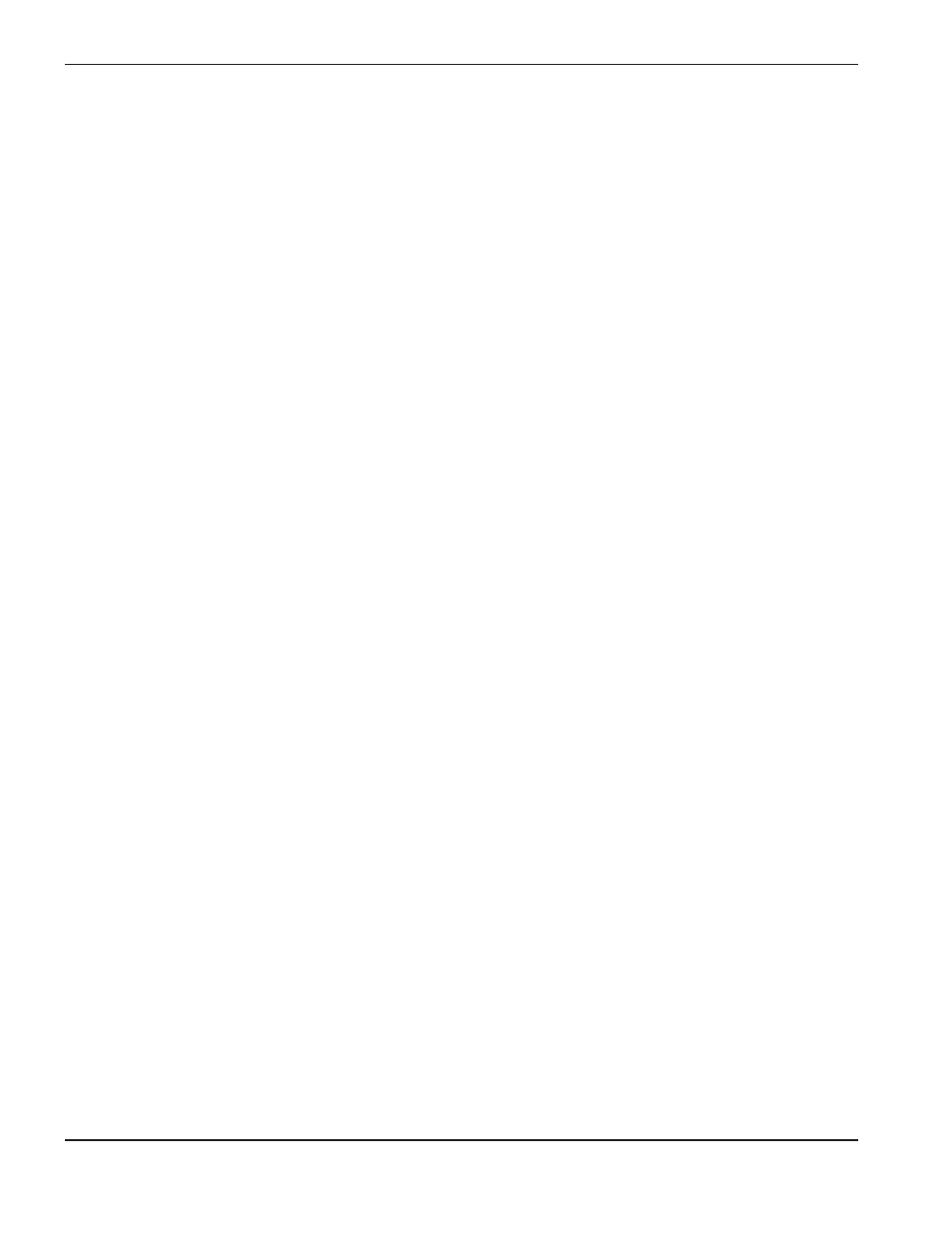
4-2
PAC500
Instruction Manual
4
OPERATION
Operating Instructions
The control circuit is turned on by means of the ON/OFF switch on the operator’s panel. A WHITE light indicates
that the control is ON.
The TEST/RUN switch is turned to TEST. This allows the control circuit to be actuated without starting the arc.
With the switch in the TEST position, depress the start button. Gas and water will start to flow immediately. Adjust
the gas and water flowmeters to the settings recommended in Cut Charts, pages 4-6 through 4-10. The water spray
pattern exiting from the nozzle should have a uniform conical shape. If there is a non-uniformity in the pattern, the
nozzle should be inspected as discussed in Section 5 Routine Maintenance. The STOP button is depressed to
deactivate the gas and water flow.
The TEST/RUN switch is turned to RUN and the system is ready for cutting. The torch height is adjusted as
specified in Cut Charts. Control sequence is initiated by depressing the START button. There is a five second
preflow interval to allow the gas and water flows to be established. During this interval the GREEN light on the
operator panel will come on indicating adequate gas and water flows and that the power supply contactor is
energized. At the end of this preflow cycle, a high frequency, high voltage discharge establishes an ionized path
between the electrode and nozzle. The power supply, because of its high open circuit voltage (400 volts), will
conduct through this discharge and rapidly increase the current to form an arc between the electrode and nozzle.
This pilot arc, transfers immediately to the workpiece, thereby establishing the cutting arc between the electrode
and workpiece. Once the cutting arc is established, torch travel is initiated automatically by the control or manually
by the operator. If heavy plate is cut, a torch travel delay will be necessary. One second torch travel delay per inch
of plate thickness is a good rule of thumb.
The arc is switched off at the end of the cut by means of the STOP switch or by letting the torch run off the
workpiece.
If the PAC500 is operated in the conventional mode rather than the Water-injection mode, a special premixed gas,
65% argon-35% hydrogen, must be used. DO NOT connect this gas mixture to the control console because this
enclosure is not properly vented for hydrogen bearing gases (Refer to Section 1 Safety). The Argon-Hydrogen
Manifold, Part No. 028057, must always be used in conjunction with this gas mixture.
The operating procedure for the conventional mode is exactly the same as outlined above except that the gas flow
is set at the Argon-Hydrogen Manifold. The Torch gas hose must be removed from the console fitting and re-
connected to the fitting on the Argon-Hydrogen Manifold. The GAS flowmeter on the operator panel is shut off to
prevent the flow of nitrogen.
Applications Data
Thickness Range: .035 in. to 3 in.
Water-Injection plasma cutting should be used in this thickness range. Optimum cut quality is obtained by careful
control of the major cutting parameters: Nozzle size, Arc current, Cutting speed, Torch-to-work distance (arc
voltage), Gas and Water flowrate. These parameters are specified in Cut Charts. For applications beyond the
scope of this manual, contact your field representative.
Four nozzle sizes are available for Water-Injection cutting. Proper nozzle selection is extremely important to
obtaining optimum cut quality. The thickness ranges of these nozzles are tabulated in Table I, page 4-3. Generally,
when the operating range of two nozzles overlap, the larger nozzle will produce the best cut quality. This is
especially true for mild steel cutting because the larger nozzle produces a wider dross-free speed range.