English, 5 cable for mma welding and return current cable, 6 the welding torch – Kemppi DC 3500W User Manual
Page 8: 7 electrodes to be welded, 8 tig dc welding, 9 tig ac welding
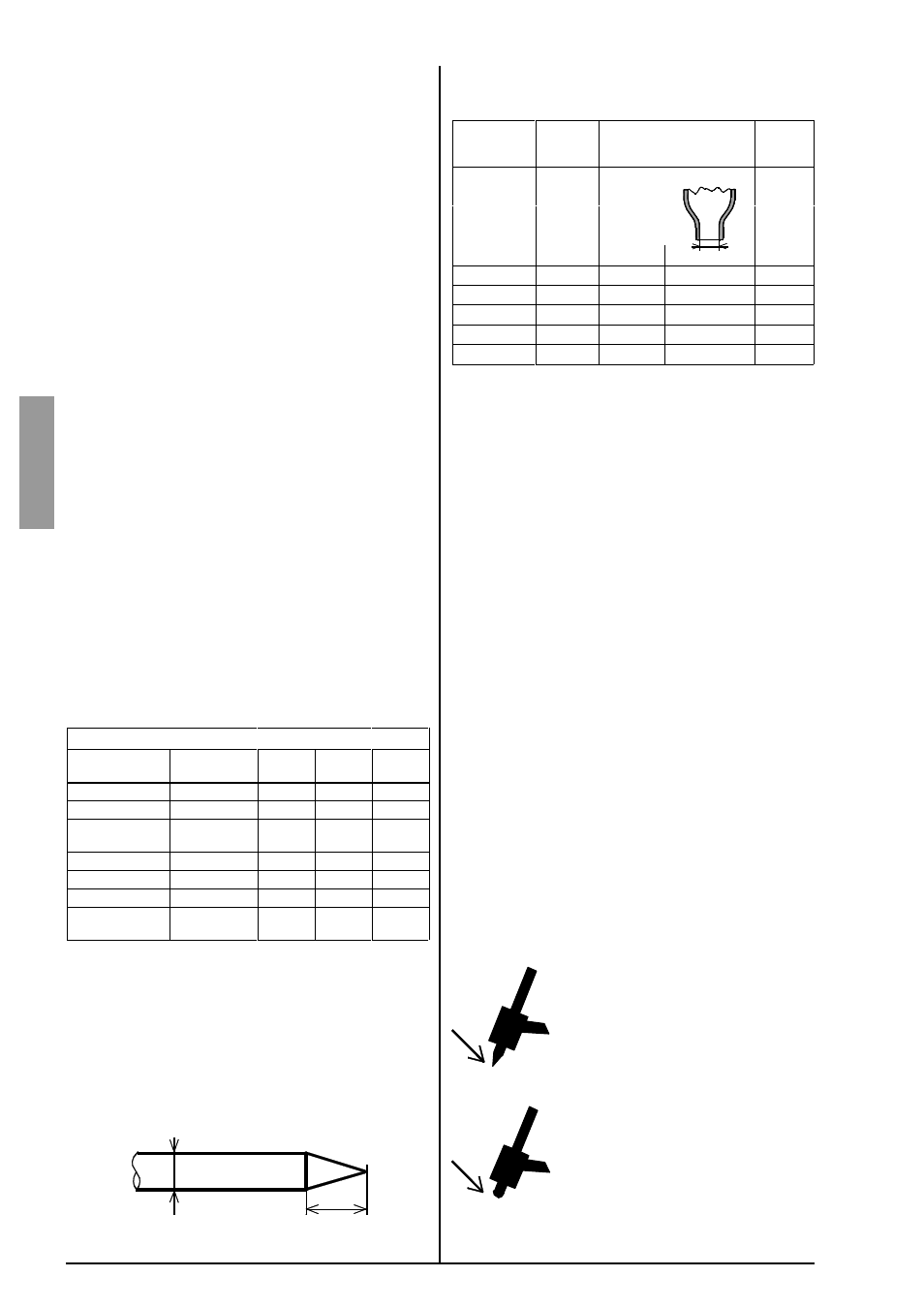
8 / 1916110E / 9901
English
Welding
current
range
Elec-
trode
Gas nozzle
Gas
flow
rate
DC–
WC20
Argon
A
ø mm
number
ø mm
l / min
5...80
1,0
4/5
6,5/8,0
5...6
70...140
1,6
4/5/6
6,5/8,0/9,5
6...7
140...230
2,4
6/7
9,5/11,0
7...8
225...350
3,2
7/8
11,0/12,5
8...10
330...350
4,0
10
16
10...12
2.5 Cable for MMA welding and return
current cable
The welding cables have to be at least 16 mm
2
copper
cables for Mastertig AC/DC 1600 and 25 mm
2
copper
cables for Mastertig AC/DC 2500, Mastertig AC/DC
2500W and 50 mm
2
copper cables for Mastertig AC/
DC 3500W. Thinner cables will cause voltage losses
and heating.
Connect the grounding clight of the return cable care-
fully, preferably directly to the piece to be welded. Use
as short welding cables as possible. Unnecessarily long
cables will lower the maximum output voltage of the
machine. Coiling of the excess cable lowers the out-
put voltage of the machine especially in AC welding
and decreases the ignition spark.
Clean the fastening surface of any paint and rust!
2.6 The welding torch
In Mastertig AC/DC 1600 and Masterig AC/DC 2500,
only an gas-cooled torch can be used. In Mastertig AC/
DC 2500 W and -3500W, you can use either an gas-
cooled or a water-cooled torch. Make sure that the torch
you are using is designed for the maximum welding
current that you need.
Never use a damaged torch !
2.7 Electrodes to be welded
By the Mastertig AC/DC power sources you can use
all electrodes designed for DC or AC welding within
the current limits of the machine in question.
Mastertig AC/DC 2500, -2500W and -3500W power
sources is suitable for carbon arc gouging and cutting
according to its maximum power.
2.8 TIG DC welding
DC current is used typically when welding different
kind of steel. We rekommend for DC welding a WC20
(grey) elctrode.
Sharpening of the electrode
The tip of the electrode is sharpened into a cone, so
that the arc becomes steady and the thermal energy is
concentrated on the spot being welded. The length of
the sharpening to the diameter of the electrode:
with small current sharp l = 3 x d
with large current blunt l = 1 x d
Choice of the electrode for DC welding. The table is
only given as a guide.
2.9 TIG AC welding
AC-current is typically used when welding aluminium.
We recommend for AC-welding a WC20 (grey) or a
clean wolfram electrode (green).
Balance
In AC-welding the ratio between the positive and neg-
ative half-cycle is called balance. With the balance you
can control heat between the electrode and work piece.
When balance is positive, it means that the positive
half-cycle is longer than the negative, more heat is
coming to the electrode than to the work piece. Corre-
spondingly when balance is negative, negative half-
cycles are longer, the work piece is hotter and the elec-
trode is colder. Mastertig AC/DC-machines have build-
in BALANCE-automatism, which chooses automatically
right balance value. User adjusts the BALANCE-knob
according to the electrode, and the machine takes care
of the balance control in different currents.
BALANCE automatics offers two benefits as com-
pared to a constant balance:
In AC welding, you can use both a sharpened and
a rounded (cut) electrode. When welding starts,
the machine will round the cut tip so that its is suit-
able.
The current-range of the electrode is extended: the
current of the lower end is lowered and the current
of the maximum end is increased.
With BALANCE automatics, you can use the position
for a sharpened electrode with a
narrower arc to obtain a narrower
seam and to a deeper penetration
than with a rounded electrode. A nar-
row seam is useful especially in fillet
welding.
When using a rounded electrode, the arc is broad and
the cleaning area of the arc is also
wider, so it can be used for end-to-
end seams and outer corners.
Reference max elecctrode diameters and yield
electrode type
yield
1600
2500,
2500W
3500W
Fe-rutile
95 %
ø 4
ø 5
ø 6
Fe-base
100 %
ø 4
ø 5
ø 6
Fe-high-yield
180 %
250-270 %
ø 2,5
- - -
ø 4
ø 4
ø 5
ø 5
Ss-rutile
- - -
ø 4
ø 6
ø 6
Ss-base
- - -
ø 4
ø 6
ø 6
Ss-high-yield
150 %
ø 3,25
ø 5
ø 6
Hard facing by
welding
100 %
ø 3,25
ø 5
ø 6
d
l