Overview – TE Technology TC-24-12 User Manual
Page 4
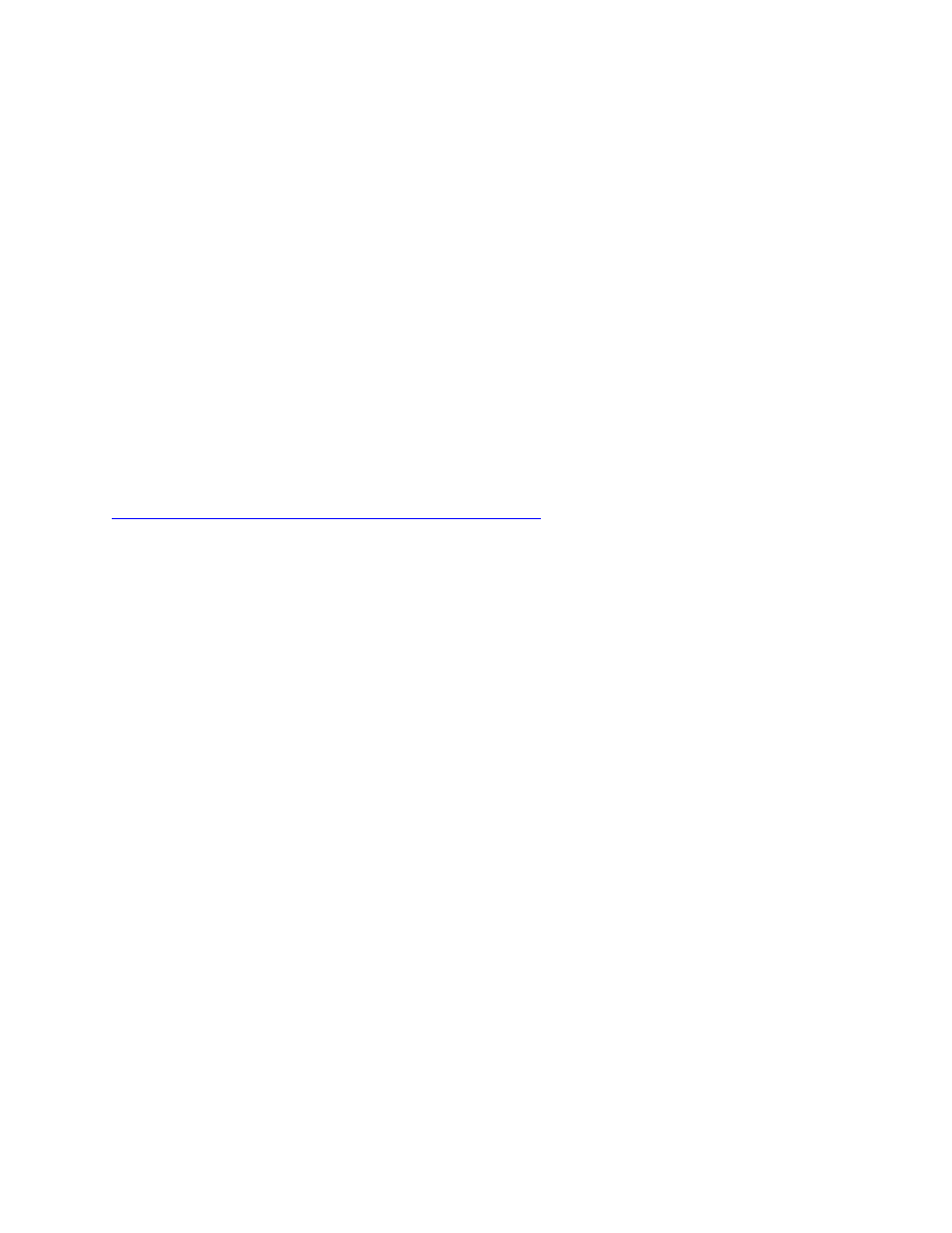
4
Overview
1.0 General Description
The TC-24-12 Temperature Controller is a pulse-width-modulated (PWM), bi-polar output
device capable of controlling a thermoelectric cooler in both the cooling and heating modes. The
controller uses a proportional and integral control mode, and consists of a microprocessor,
thermistor inputs, a power output stage, and set-temperature/tuning potentiometers. Temperature
status indicator LEDs, an alarm output transistor, and voltage test points are also included. The
potentiometers can be removed and set-point/tuning parameters can be preprogrammed from the
factory for high-volume applications if desired.
The TC-24-12 will operate with input voltages ranging from (10.8 to 26.4) volts DC (a minimum
of 10.8 V input is needed to operate the on-board microprocessor). It will control output currents
of up to 11.9 amps maximum (with no load on the alarm circuit). The H-bridge output stage
uses highly efficient N-channel MOSFET output devices, so no additional heat sinking is
needed. The TC-24-12 offers a low-cost means of temperature control, yet because of its PWM
methodology, when used properly, it will not reduce the cooler’s reliability as might otherwise
happen with on-off types of controllers. (Additional information on cooler reliability and the
affects of PWM control can be found at
http://www.tetech.com/publications/pubs/ICT99MJN.pdf
).
2.0 PWM Control Description
The TC-24-12 uses PWM at 1000 Hz, meaning that the power is switched between fully "ON"
and fully "OFF" one thousand times per second. Varying the ratio of "ON" time to "OFF" time
regulates the amount of cooling. The output of the controller is a square wave with the duty
cycle (the ratio of the "ON" portion of the cycle versus the total cycle) being varied as necessary
to achieve the desired cooling or heating. Essentially, the input voltage to the controller is
switched ON or OFF to the thermoelectric module(s). Thus, the input voltage to the temperature
controller will define the output voltage to the cooler when the power is switched "ON"—there
is not a linear output voltage to the thermoelectric module(s) that increases as more cooling is
required. One should therefore choose an input voltage that is no greater than the Vmax of the
cooling assembly or thermoelectric module(s). When making a cooling system from
thermoelectric modules, the maximum operating voltage (the controller's input voltage) is
typically no more than 75% of module's Vmax. Of course, multiple modules can be used in a
series or series-parallel combination, and the Vmax of the module system will be the total Vmax
of the modules in series. In this case, the input voltage is generally no more that 75% of the
Vmax of the module system.
3.0 Control Thermistor Input
The TC-24-12 uses a negative temperature coefficient thermistor to give feedback to the control
circuitry. The sensor’s nominal resistance is 15,000 ohms at 25 °C. The same type of
thermistors can also be used for sensing over-temperature conditions. (See section 4.0 below.)
The standard thermistor-head styles and resistance-verses-temperature curves are shown in
“Thermistor Styles for TC-24-12” (The MP-2379 thermistor is provided with the controller).
If you want to use thermistors that have different resistance-versus-temperature curves than the
standard thermistor, it can be done as long as the operating resistance range is within that of the