TE Technology TC-24-12 User Manual
Page 9
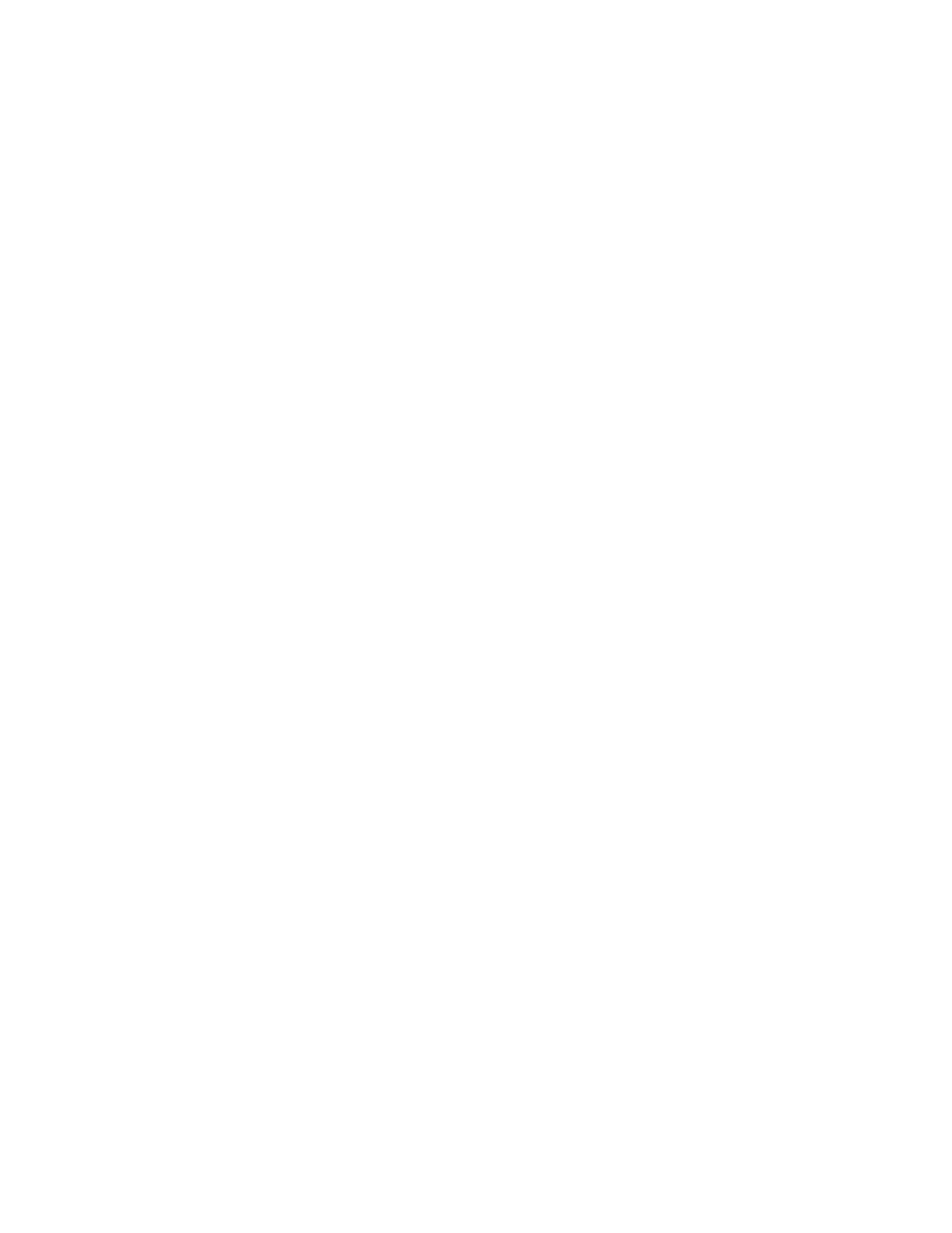
9
12.0 Control Function Description
12.1 Proportional control: This eliminates much of the temperature cycling inherent in on/off
control. Proportional control increases or decreases the output of the controller depending
on the difference between the set temperature and the actual temperature. The
proportioning bandwidth is the temperature span over which the power is proportioned
from -100% to +100% power, centered about the set temperature. That is, the controller
output decreases to 0% power as it reaches the set temperature and to ±100% power
(depending on whether the controller is in the heating or cooling mode) as it reaches either
end of the bandwidth.
For example, suppose the controller is being operated in the cooling mode, the set point is
10 °C, and the bandwidth is set to 5 °C. The controller power is at +100% and starts to
proportionally decrease as the sensor temperature cools below 12.5 °C. The power will be
reduced to 0% when the sensor is at 10 °C. The power will then proportionally increase at
negative power up to -100% when the sensor is at 7.5 °C. (Of course, this example
presumes that the cooler would have enough capacity to cool to 7.5 °C.)
If the bandwidth is set too narrow, the temperature will oscillate around the set point. If
the bandwidth is too wide, the controller will be slow to respond, or it may never reach the
set temperature.
12.2 Integral Control: This corrects for any offset between the set temperature and the sense
temperature by averaging the offset with respect to time. This essentially shifts the
proportioning bandwidth.
For example, suppose the set temperature is 10 °C, the bandwidth is set to 5 °C, and the
controller settled to a constant 11 °C (corresponding to 40% power). If the integral control
is set to 1 repeat per minute, the controller will increase the power to 80% in 1 minute. In
this example, after one minute of operation the controller calculated that the error from the
desired temperature to actual temperature was 1 °C above set temperature. With a
bandwidth of 5 °C, the controller then calculated that it needed an additional 40% output
(100% change in output per 2.5 °C of error * 1 °C error = 40%). This additional 40%
output was added to the existing 40% output to yield 80% output. The integral portion of
the output is recalculated at the frequency specified by the integral potentiometer. Thus, at
the next update period for the integral the controller will add or subtract as necessary from
the 80% output. Of course, the maximum output is limited to +100%, and the minimum is
limited to -100%.
If the integral control is set too high, the temperature will oscillate. If integral control is
set too low, it will take a long time for the temperature to settle to steady state.
13.0 Controller Tuning
Tuning of PI control requires knowing the time period of the natural temperature cycle of the
system and the bandwidth used to achieve this cycle. The following steps will tune the
controller:
13.1 Verify that the power supply on.