Theory of operation – Daktronics M SERIES User Manual
Page 10
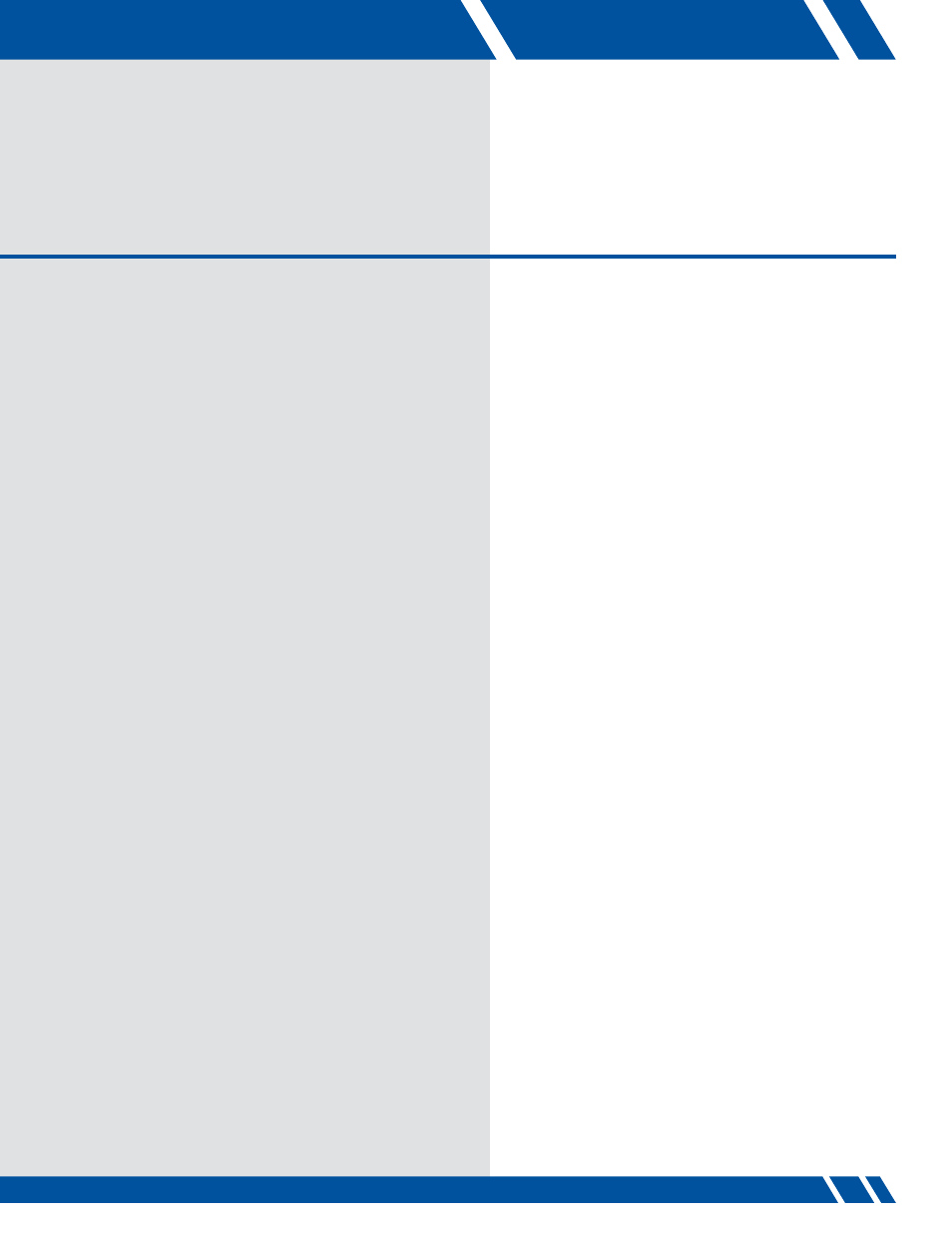
Each Vortek
®
hoist is connected to the main high voltage power buss through a safety twist-locking plug. This plug
brings in the main 3-phase power that is connected to the motor drive and motor brake located in each hoist
assembly. Connected to each Vortek M Series hoist assembly through safety locking connectors are 24 V DC
power, Emergency Stop (E-Stop) circuit and a network cable.
The motor drive controls all movements of the hoist. Each drive on each hoist contains programming to identify it
to the network. This programming also includes but is not limited to maximum speed and acceleration. Each motor
drive monitors an incremental encoder, limit switches, load and emergency stop status. The incremental encoder
is used for position control and motor operation feedback. The limit switches are used for maximum up and down
travel. Load sensing is used for the detection of an under load or overload condition. The emergency stop status is
used to detect the operation of the emergency stop system.
Monitoring of each hoist is done over a CC-Link high performance industrial network using a Programmable
Logic Controller (PLC). The PLC is located in the operator station along with the PLC power supply, a Network
communications card, an I/O module and an optional module for communications to a handheld pendant. A 24
VDC power supply for the system is also located in the operator station.
The Human Machine Interface (HMI) that is mounted on the operator station allows the operator to perform
hoist movement through a combination of touchscreen selection and pressing of the EXECUTE MOVE button.
No movement will occur until the EXECUTE MOVE button is pressed. All hoist information is entered on the HMI
screens and then stored in the PLC. The HMI communicates to the PLC which in turn communicates to the hoists
over Network.
03
THEORY OF OPERATION
THEORY OF OPERATION
7