6 stopping and shutdown – Flowserve MENBLOC 60Hz User Manual
Page 25
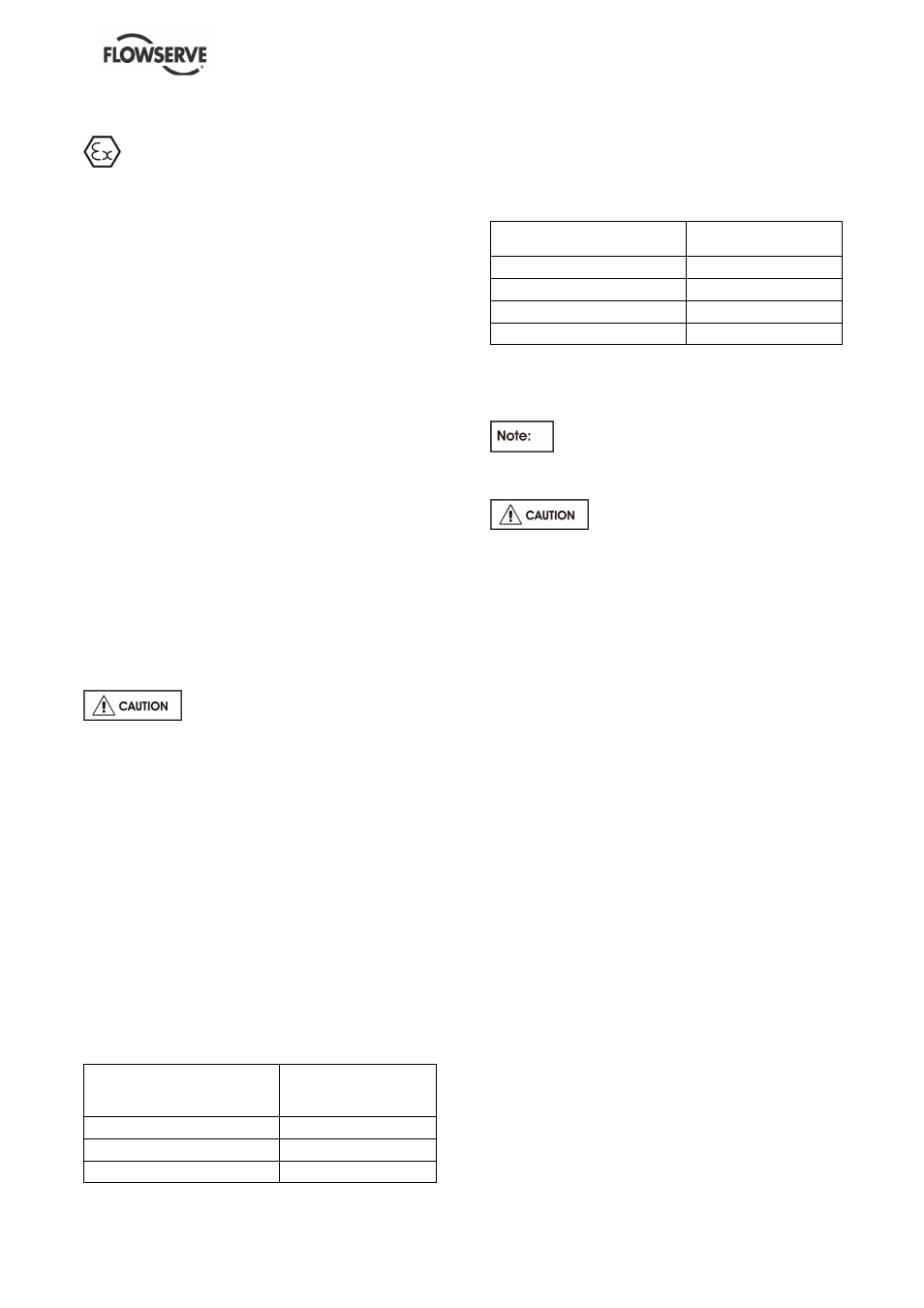
MENBLOC 60Hz USER INSTRUCTIONS ENGLISH 71559945 - 02/13
Page 25 of 36
flowserve.com
5.5.3 Bearings
If the pumps are working in a potentially
explosive atmosphere, temperature or vibration
monitoring at the bearings is recommended.
If bearing temperatures are to be monitored it is
essential that a benchmark temperature is
recorded at the commissioning stage and after the
bearing temperature has stabilized.
•
Record the bearing temperature (t) and the
ambient temperature (ta)
•
Estimate the likely maximum ambient
temperature (tb)
•
Set the alarm at (t+tb-ta+5)
°
C [(t+tb-ta+10)
°
F]
and the trip at 100
°
C (212
°
F) for oil
lubrication and 105
°
C (220
°
F) for grease
lubrication
It is important, particularly with grease lubrication,
to keep a check on bearing temperatures. After
start up the temperature rise should be gradual,
reaching a maximum after approximately 1.5 to 2
hours. This temperature rise should then remain
constant or marginally reduce with time.
5.5.4 Normal vibration levels, alarm and trip
For guidance, pumps generally fall under a
classification for rigid support machines within the
International rotating machinery standards and the
recommended maximum levels below are based
on those standards.
Alarm and trip values for installed
pumps should be based on the actual
measurements (N) taken on site on the bearing
housings of the pump in the fully commissioned as
new condition.
The example (N) value is given for the preferred
operating flow region (typically this may extend to
70 to 120 % of the pump best efficiency point);
outside the preferred flow region the actual
vibration experienced may be multiplied by up to 2.
These standard values can vary with the rotational
speed and the power absorbed by the pump. For
any special case, do not hesitate to consult us.
Measuring vibration at regular intervals will then
show any deterioration in pump or system
operating conditions.
Vibration Velocity - unfiltered
Horizontal
Configuration
mm/s (in./s) r.m.s.
Normal N
≤
5.6 (0.22)
Alarm N x 1.25
≤
7.1 (0.28)
Shutdown Trip N x 2.0
≤
11.2 (0.44)
5.5.5 Stop/start frequency with IEC motors
Pump sets are normally suitable for the number of
equally spaced stop/starts per hour shown in the
table below. Check actual capability of the driver
and control/starting system before commissioning.
Motor rating kW (hp)
Maximum stop/starts
per hour
Up to 15 (20)
15
Between 15 (20) and 90 (120)
10
90 (120) to 150 (200)
6
Above 150 (200)
Refer
Where duty and standby pumps are installed it is
recommended that they are run alternately every
week.
For NEMA motors, contact the vendor.
5.6 Stopping and shutdown
According to hydraulic conditions of
the installation and its automation degree, stop
and restart procedures can have different forms.
Nevertheless all of them must respect imperatively
the following rules:
5.6.1 Stopping < 1 hour
a) Isolate motor.
b) Avoid reverse rotation of the pump.
c) Make sure that the discharge line pressure
does not reach the foot valve.
5.6.2 Stopping < 1 month
a) Isolate motor.
b) Avoid reverse rotation of the pump.
c) Make sure that the discharge line pressure
does not reach the foot valve.
d) Close the outlet valve. Eventually close the
inlet valve.
e) Switch off external power supply,
flushing/quench, cooling liquid.
5.6.3 Shutdown > 1 month
a) Isolate motor.
b) Avoid reverse rotation of the pump.
c) Make sure that the discharge line pressure
does not reach the foot valve.
d) Close the outlet valve. Eventually close the
inlet valve.
e) Switch off external power supply,
flushing/quench, cooling liquid.
f) Keep the pump fully filled with water. In case
of pumped liquid other than water, drain the
pump entirely.
g) Turn once per week the pump shaft of one or
two turns.
h) Never restart the pump without carrying out
the verifications recommended before starting
(see § 5.4.1).