Flowserve Guardian Sealless Metallic User Manual
Page 28
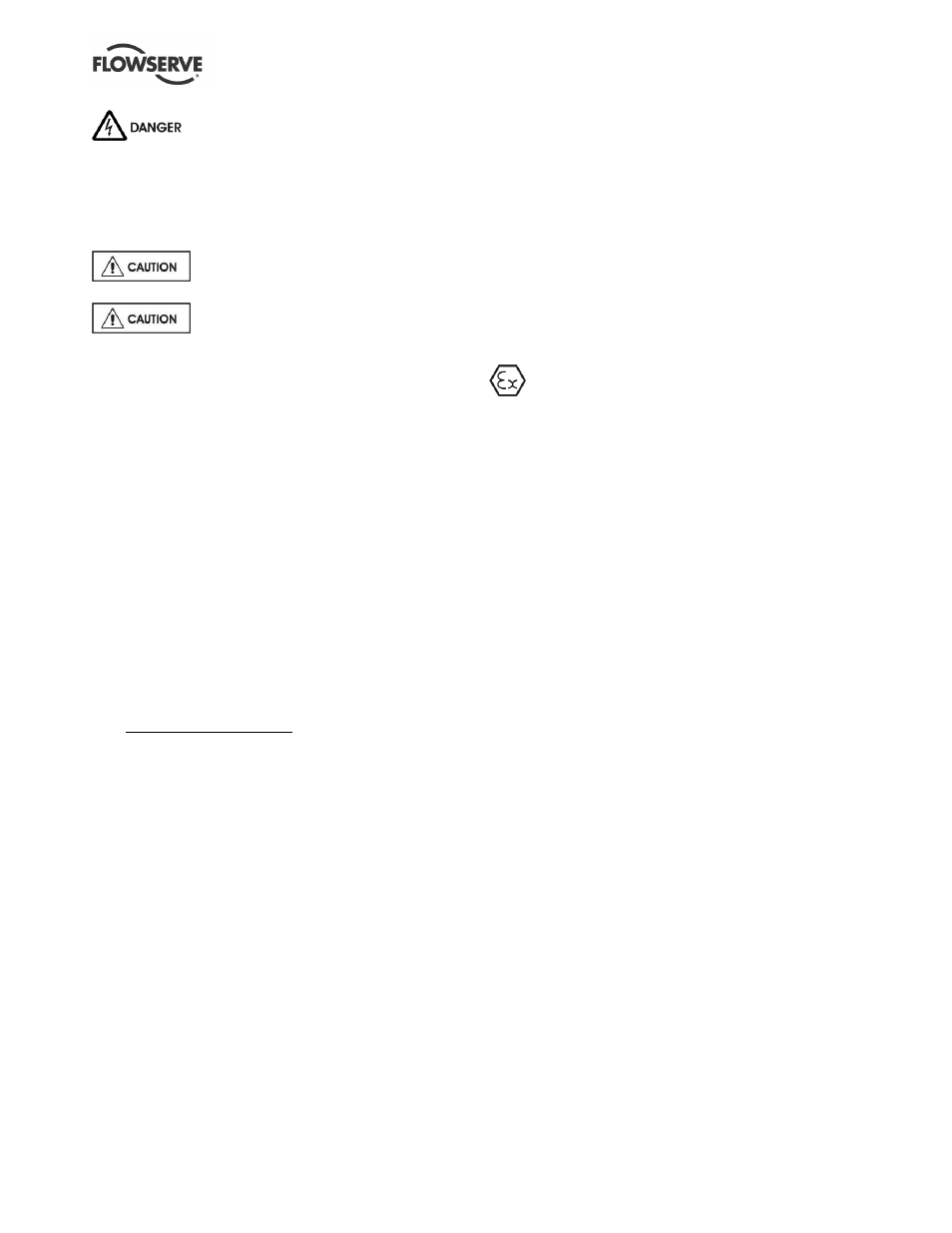
GUARDIAN USER INSTRUCTIONS ENGLISH 71569212 08-11
Page 28 of 68
flowserve.com
The motor must be wired up in
accordance with the motor manufacturer's
instructions (normally supplied within the terminal
box) including any temperature, earth leakage,
current and other protective devices as appropriate.
The identification nameplate should be checked to
ensure the power supply is appropriate.
See section 5.4,
Direction of rotation
before connecting the motor to the electrical supply.
For close coupled pumps it is necessary
to wire the motor with flexible conduit of sufficient length
to allow the motor/power end assembly to be moved
back from the casing for maintenance.
4.8 Final shaft alignment check
a)
Level baseplate if appropriate.
b)
Mount and level pump if appropriate. Level the
pump by putting a level on the discharge flange.
If not level, adjust the footpiece by adding or
deleting shims [3126.1] between the footpiece
and the bearing housing.
c)
Check initial alignment. If pump and driver have
been remounted or the specifications given below
are not met, perform an initial alignment as
described in Section 4.5. This ensures there will
be sufficient clearance between the motor hold
down bolts and motor foot holes to move the
motor into final alignment. The pump and driver
should be within 0.38 mm (0.015 in.) FIM (Full
Indicator Movement) parallel, and 0.0025 mm/mm
(0.0025 in./in.) FIM angular.
Stilt mounted baseplates: If initial alignment
cannot be achieved with the motor fasteners
centered, the baseplate may be twisted. Slightly
adjust (one turn of the adjusting nut) the stilts at
the driver end of the baseplate and check for
alignment to the above tolerances. Repeat as
necessary while maintaining a level condition as
measured from the pump discharge flange.
d)
Run piping to the suction and discharge to the
pump. There should be no piping loads
transmitted to the pump after connection is
made. Recheck the alignment to verify that
there are no significant changes.
e)
Perform final alignment. Check for soft-foot under
the driver. An indicator placed on the coupling,
reading in the vertical direction, should not indicate
more than 0.05 mm (0.002 in.) movement when
any driver fastener is loosened. Align the driver
first in the vertical direction by shimming
underneath its feet. When satisfactory alignment is
obtained the number of shims in the pack should
be minimized. It is recommended that no more
than five shims be used under any foot. Final
horizontal alignment is made by moving the driver.
Maximum pump reliability is obtained by having
near perfect alignment. Flowserve recommends
no more than 0.05 mm (0.002 in.) parallel, and
0.0005 mm/mm (0.0005 in./in.) angular
misalignment. (See Section 6.8.4.2.)
f)
Operate the pump for at least an hour or until it
reaches final operating temperature. Shut the
pump down and recheck alignment while the pump
is hot. Piping thermal expansion may change the
alignment. Realign pump as necessary.
4.9 Protection systems
The following protection systems are
recommended particularly if the pump is installed in a
potentially explosive area or is handling a hazardous
liquid. If in doubt consult Flowserve.
If there is any possibility of the system allowing the
pump to run against a closed valve or below
minimum continuous safe flow a protection device
should be installed to ensure the temperature of the
liquid does not rise to an unsafe level.
If there are any circumstances in which the system
can allow the pump to run dry, or start up empty, a
power monitor should be fitted to stop the pump or
prevent it from being started. This is particularly
relevant if the pump is handling a flammable liquid.
If leakage of product from the pump can cause a
hazard it is recommended that an appropriate
leakage detection system is installed.
To prevent excessive surface temperatures at
bearings it is recommended that temperature or
vibration monitoring are carried out.
Auxiliary equipment – instrumentation
4.9.1
Leak detection
An intrinsically-safe, optical leak detection system is
available for Guardian G & H series pumps. Contact
your local Flowserve Sales office or Distributor/
Representative for more details.
4.9.2
Temperature probes
Optional temperature probes are available to monitor
both the external shell surface and the internal fluid in
the containment shell (Figure 4-26). Refer to Figure 4-
27 to determine the instrument location for probe type.
Wiring diagrams: refer to Figure 4-26 for both Type J
and RTD designs.