Flowserve Guardian Sealless Metallic User Manual
Page 57
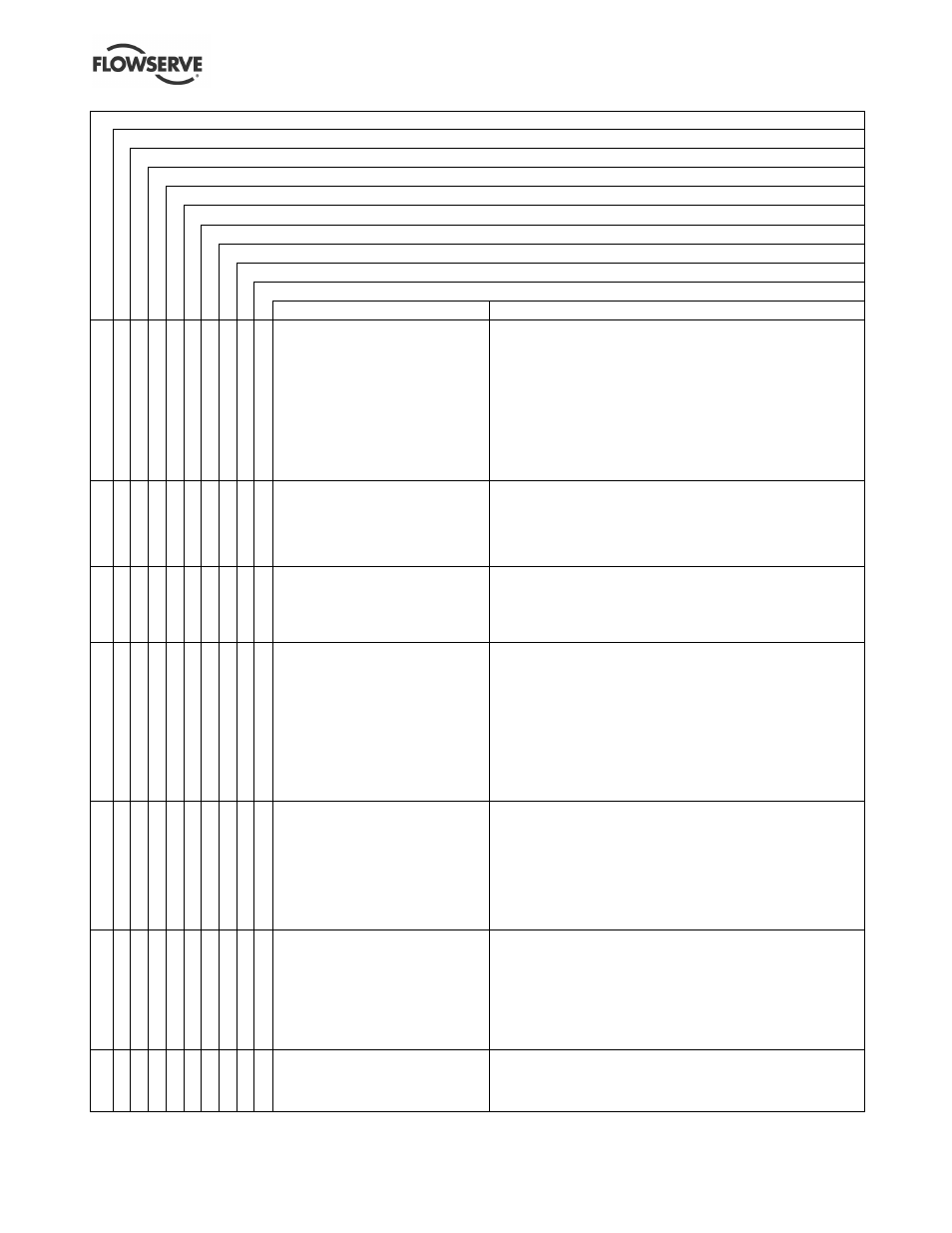
GUARDIAN USER INSTRUCTIONS ENGLISH 71569212 08-11
Page 57 of 68
flowserve.com
Pump not reaching design flow rate
⇓
⇓
⇓
⇓
⇓
⇓
⇓
⇓
Pump not reaching design head (TDH)
⇓
⇓
⇓
⇓
⇓
⇓
⇓
⇓
No discharge or flow with pump running
⇓
⇓
⇓
⇓
⇓
⇓
⇓
⇓
Pump operates for short period, then loses prime
⇓
⇓
⇓
⇓
⇓
⇓
⇓
⇓
Excessive noise from wet end
⇓
⇓
⇓
⇓
⇓
⇓
⇓
⇓
Excessive noise from power end
⇓
⇓
⇓
⇓
⇓
⇓
⇓
⇓
Pump exhibits increased or higher than anticipated power consumption
⇓
⇓
⇓
⇓
⇓
⇓
⇓
⇓
Pump exhibits decreased or lower than anticipated power consumption
⇓
⇓
⇓
⇓
⇓
⇓
⇓
⇓
⇓
⇓
⇓
⇓
⇓
⇓
⇓
⇓
⇓
⇓
⇓
⇓
⇓
⇓
⇓
⇓
POSSIBLE CAUSES
POSSIBLE REMEDIES
Bearing contamination appearing on
the raceways as scoring, pitting,
scratching or rusting caused by
adverse environment and entrance of
abrasive contaminants from
atmosphere.
1. Work with clean tools in clean surroundings.
2. Remove all outside dirt from housing before exposing bearings.
3. Handle with clean dry hands.
4. Treat a used bearing as carefully as a new one.
5. Use clean solvent and flushing oil.
6. Protect disassembled bearing from dirt and moisture.
7. Keep bearings wrapped in paper or clean cloth while not in use.
8. Clean inside of housing before replacing bearings.
9. Check oil seals and replace as required.
10. Check all plugs and tapped openings to make sure that they
are tight.
Brinelling of bearing identified by
indentation on the ball races, usually
caused by incorrectly applied forces
in assembling the bearing or by shock
loading such as hitting the bearing or
drive shaft with a hammer.
When mounting the bearing on the drive shaft use a proper size
ring and apply the pressure against the inner ring only. Be sure
when mounting a bearing to apply the mounting pressure slowly
and evenly.
False brinelling of bearing identified
again by either axial or circumferential
indentations usually caused by
vibration of the balls between the
races in a stationary bearing.
1. Correct the source of vibration.
2. Where bearings are oil lubricated and employed in units that
may be out of service for extended periods, the drive shaft should
be turned over periodically to relubricate all bearing surfaces at
intervals of one to three months.
Thrust overload on bearing identified
by flaking ball path on one side of the
outer race or in the case of maximum
capacity bearings, may appear as a
spalling of the races in the vicinity of
the loading slot. (Please note:
maximum capacity bearings are not
recommended in Mark 2I pumps.)
These thrust failures are caused by
improper mounting of the bearing or
excessive thrust loads.
Follow correct mounting procedures for bearings.
Misalignment identified by fracture of
ball retainer or a wide ball path on the
inner race and a narrower cocked ball
path on the outer race. Misalignment
is caused by poor mounting practices
or defective drive shaft. For example,
bearing not square with the centerline
or possibly a bent shaft due to
improper handling.
Handle parts carefully and follow recommended mounting
procedures. Check all parts for proper fit and alignment.
Bearing damaged by electric arcing
identified as electro- etching of both
inner and outer ring as a pitting or
cratering. Electrical arcing is caused
by a static electrical charge
emanating from belt drives, electrical
leakage or short circuiting.
1. Where current shunting through the bearing cannot be
corrected, a shunt in the form of a slip ring assembly should be
incorporated.
2. Check all wiring, insulation and rotor windings to be sure that
they are sound and all connections are properly made.
3. Where pumps are belt driven, consider the elimination of static
charges by proper grounding or consider belt material that is less
generative.
Bearing damage due to improper
lubrication, identified by one or more
of the following:
1. Abnormal bearing temperature
1. Be sure the lubricant is clean.
2. Be sure proper amount of lubricant is used. The constant level
oiler supplied with Durco pumps will maintain the proper oil level if
it is installed and operating properly. In the case of greased