Firing processes – Skutt GlassMaster Kiln User Manual
Page 28
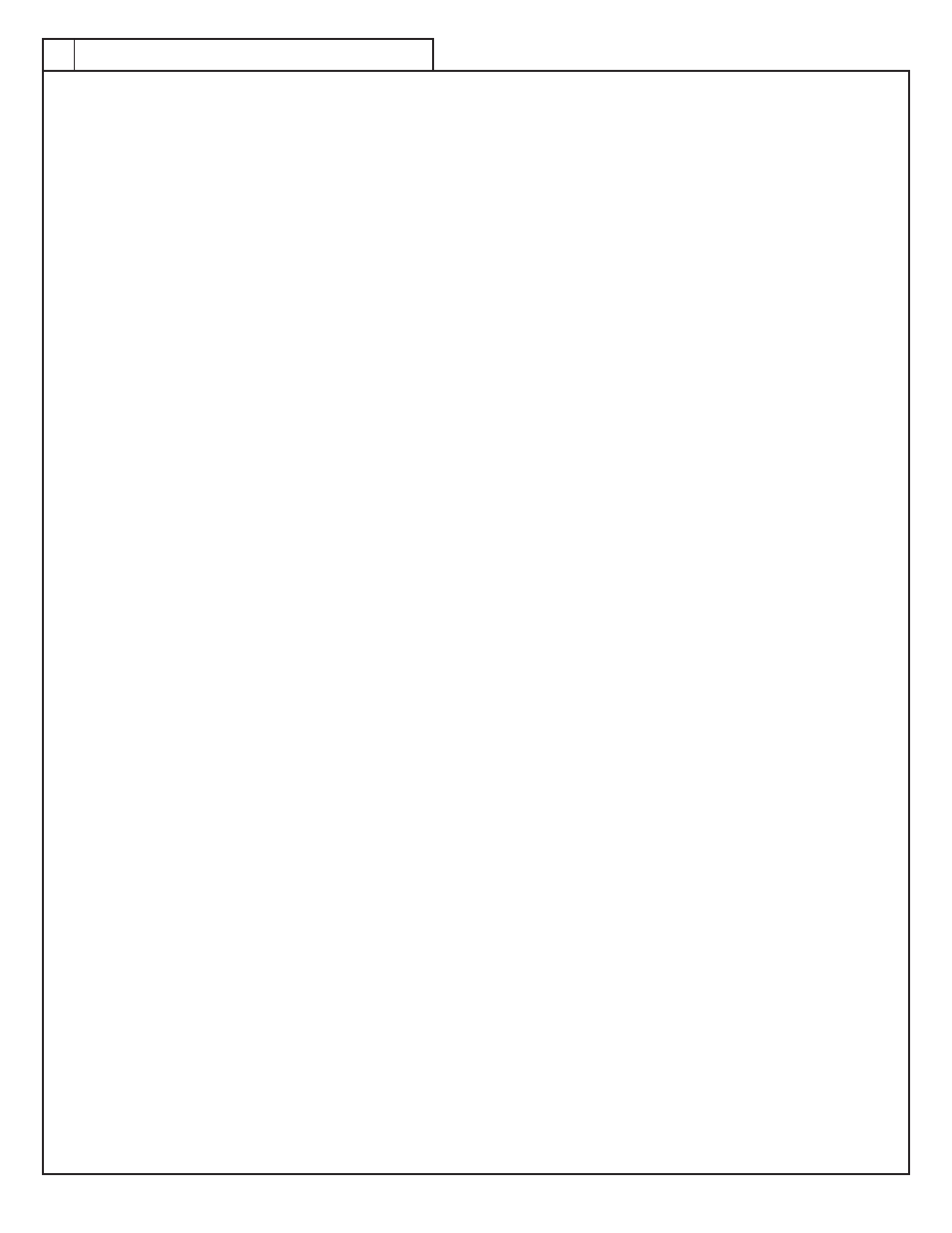
28
28
Firing Processes
There are many different processes or techniques used for manipulating glass with heat inside a kiln. In this
manual we will focus on two, Fusing and Slumping. Other techniques include but are not limited to Drop Molds,
Pate de Verre, Casting, Painting, and Combing. For more information on using your kiln with these techniques
please consult your glass supplier.
f
usinG
Fusing is the process of joining 2 or more pieces of glass together by the application of heat. This glass can
be in the form of sheets, stringers, frit or a host of other forms. There are different degrees of fusing. You may want
to fuse glass so it sticks to another piece of glass without deforming. This is known as a “Fuse to Stick”. If you were
to apply more heatwork to the piece the edges would round slightly. This is known as a “Tack Fuse”. A “Full Fuse”
is created when the pieces have melted completely together and are 1/4” thick. A “Texture Fuse” is any point in-
between a Fuse to Stick” and a “Full Fuse”.
There is a temperature range at which glass can be fused. The point at which it begins to fuse is influenced
by the rate at which the temperature is climbing when it reaches the fusing range. Most fusing glass will begin to
fuse between 1400 F and 1480 F. Remember that heatwork is a function of time and temperature.
Starting with glass that has been determined to be compatible is only the beginning to a successful fusing
or slumping project. The temperature and various temperature rates in a firing program must be designed to the
specific needs of the project you are creating. The size, thickness, shape, and type of glass all must be considered
when designing a firing program.
The Glass Fire programs take advantage of a preprocess cycle that allow the pieces to slowly enter the work-
ing temperature of the process phase. This helps the glass achieve greater heat uniformity and allows air bubbles
between layers a chance to escape before they are sealed between the layers. As a precaution you may want to
provide a dam or barrier around the glass when fusing more than 2 layers. With more than 2 layers, the glass will
spread until it finds a level of 1/4” and could possibly flow into another piece or off the shelf.
s
luMpinG
Slumping can be defined as the controlled bending of glass under the influence of heat and gravity within a
kiln. This is generally done over or into a mold. Molds can be made out of a variety of different materials and can
be found at art glass supply businesses.
When slumping, it is necessary to take into account the shape of the mold, the thickness of the piece, and the
degree of heatwork desired. The GlassFire mode may be used when the mold is simple and shallow, however,
deeper more complex molds may require a custom designed firing program and close supervision.
Gravity plays a very important role in slumping, especially slumping over a mold as opposed to into a mold.
If the shape of the mold dictates that the unbent glass is largely unsupported, the weight of the unsupported glass
will pull the glass over the mold quicker than if only a small portion is unsupported.
A thin piece of glass will bend quicker than a thick piece of glass. A thick piece of glass requires more Hold
time in the final segment of the process phase.
In some cases the artist may want to control the amount of bend by visually inspecting the kiln. Be sure to
follow the safety guidelines listed in this manual when using this technique. When the proper amount of heatwork
is reached the artist can press the ANNEAL NOW key to advance the kiln into the cooling cycle. Slumping projects
that receive too much heatwork can take on unwanted texture from the mold or in extreme cases fuse to a puddle.
G
eneral
f
irinG
G
uidelines