2 lubrication, 3 adjusting the discharge air flow – AEC Colortronic MSH Series 2039 User Manual
Page 22
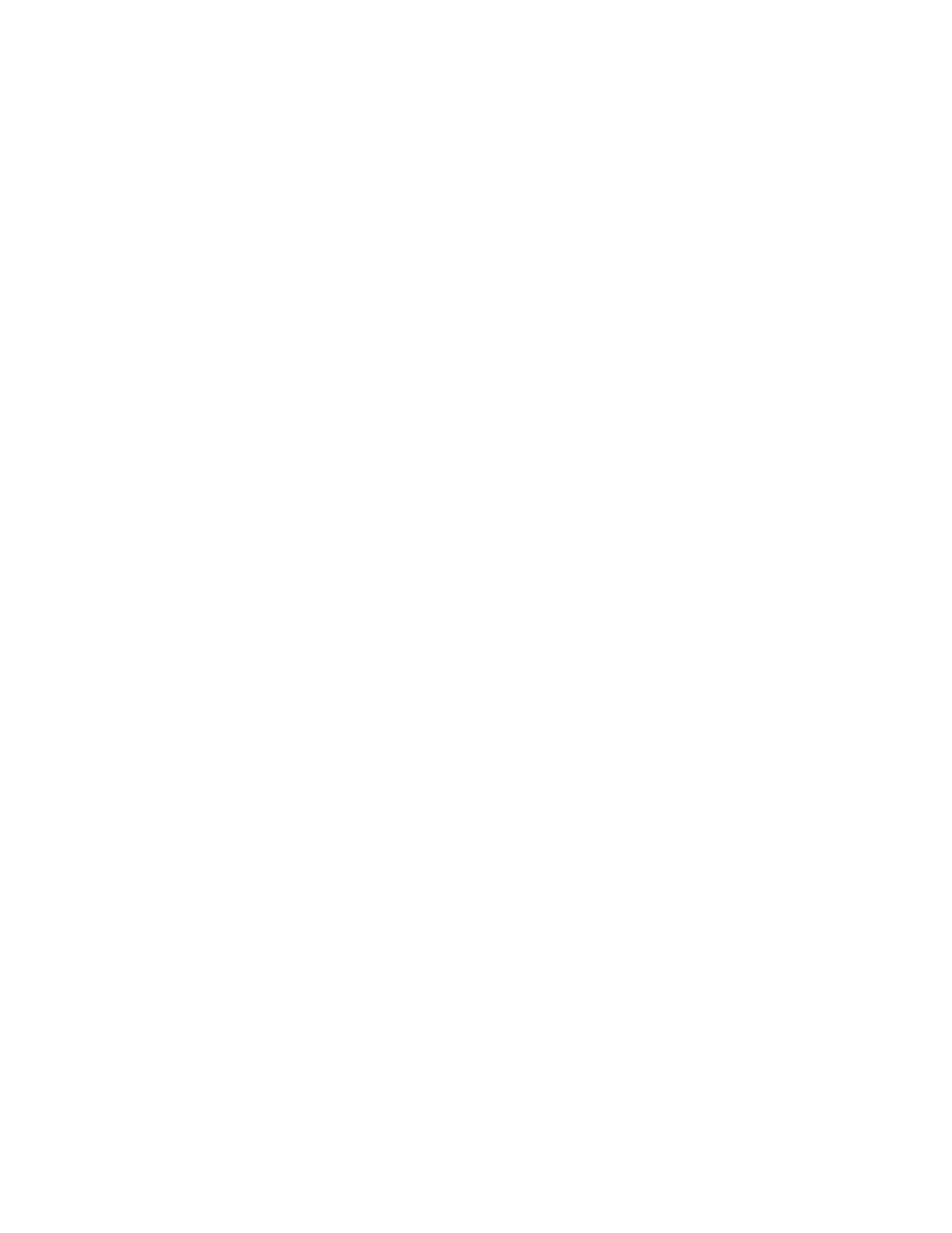
C Series Granulators
Maintenance
22 of 53
5-2 Lubrication
The machine is pre-lubricated except for the motor. For motor lubrication, check the tag
supplied by the motor manufacturer.
The main rotor bearings are lubricated at the factory but need re-lubrication periodically.
Grease fittings are provided for re-lubrication and are located on the right and left-hand
bearing housings. Lubricate every month or 750 hours while the machine is running with
about 112 grams (4 oz.) of grease. Use a lithium-based grease conforming to NLGI grade #1
or #2. More frequent lubrication may be required in severe applications.
The jackscrews are lubricated at the factory. For re-lubrication instructions, refer to the Duff-
Norton Manuals, which were included with the granulator.
5-3 Adjusting the Discharge Air Flow
If the discharge airflow is insufficient, the granulate can accumulate in the discharge
transition just below the screen cradle. The build-up eventually backs up into the cutting
chamber where continued agitation by the rotor can cause overheating and possibly stalling of
the motor.
The discharge damper is located on the end of the discharge transition on the opposite side
from the airveyor outlet. Adjust the damper by turning the counterweight clockwise or
counterclockwise to change the distance from the counterweight to the pivot. Set the
counterweight to obtain the conveying velocity required to move material across the bottom
of the discharge while maintaining maximum air flow through the cutting chamber.
Move the counterweight out, away from the pivot, to decrease the airflow. Move the
counterweight toward the pivot to increase the airflow.
The discharge transition can be cleaned via the discharge opening with a shop vacuum.