1 9 thr ead cy cles – HEIDENHAIN SW 54843x-02 DIN Programming User Manual
Page 293
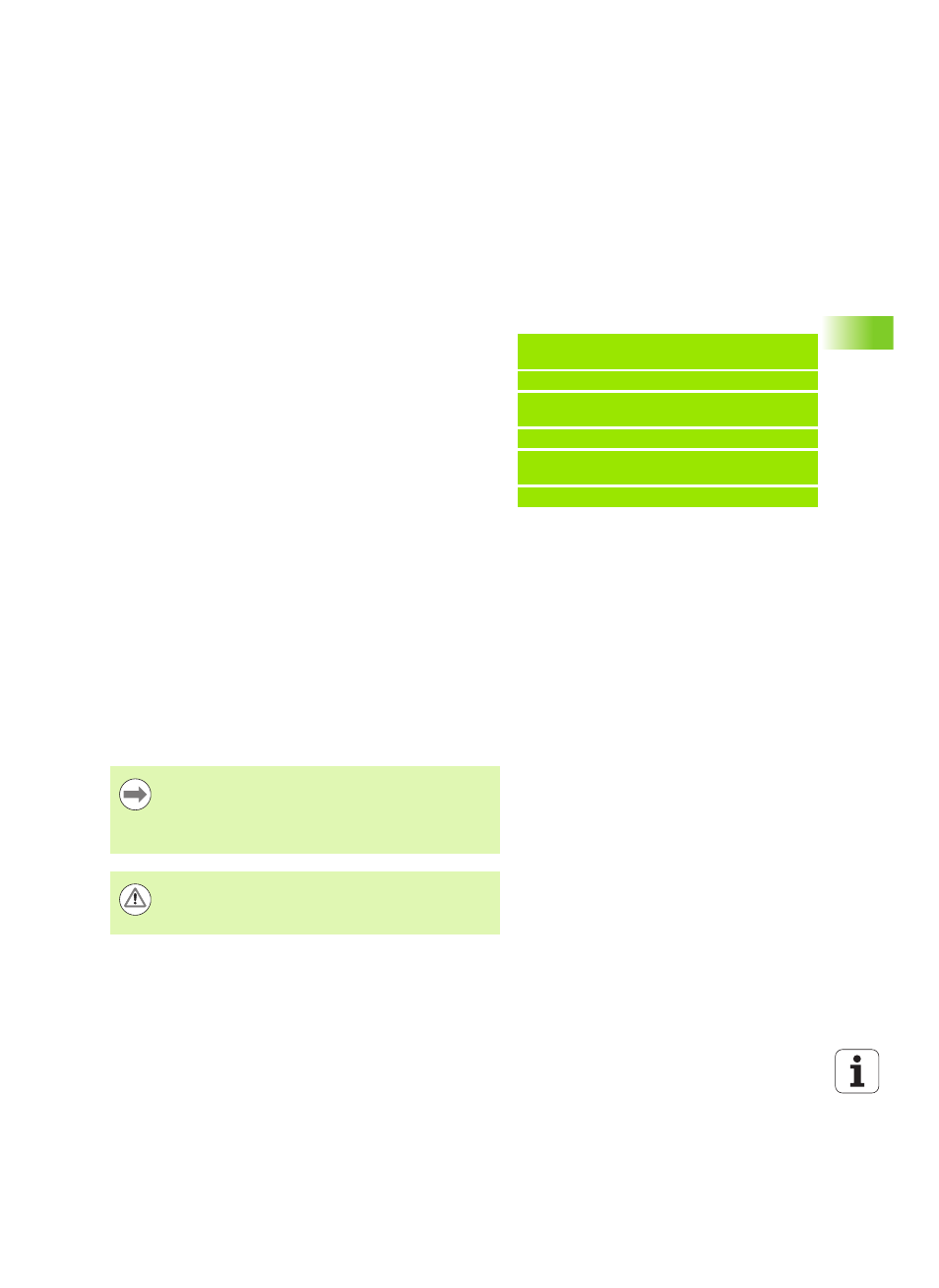
HEIDENHAIN MANUALplus 620, CNC PILOT 640
293
4.1
9
Thr
ead cy
cles
Run-in length B: The slide requires a run-in distance at the start of
thread in order to accelerate to the programmed contouring feed rate
before starting the actual thread.
Run-out length P: The slide needs an overtravel at the end of the
thread to decelerate again. Remember that the paraxial line P needs
overtravel even with an oblique thread run-out
You can calculate the minimum run-in and run-out length with the
following equation.
Determination of external/internal thread:
G31 with contour reference—closed contour: External or internal
thread is defined by the contour. BD has no meaning.
G31 with contour reference—open contour: External or internal
thread is defined by "BD". If "BD" is not programmed, the contour is
used to determine whether a thread is external or internal.
If the thread contour is programmed directly after the cycle, "BD"
determines whether the thread is an internal or external thread. If
"BD" is not programmed, the algebraic sign of "U" is evaluated (as in
the MANUALplus 4110).
U>0: Internal thread
U<0: External thread
Starting angle C: At the end of the "run-in path B" the spindle is at the
"starting angle C" position. Therefore, if the thread is to start exactly at
the starting angle, position the tool by the run-in length—or by the run-
in length plus a multiple of the thread pitch—in front of the beginning
of the thread.
The individual thread cuts are calculated from the thread depth,
maximum approach I and type of approach V.
Example: G31, continued
N 50 G31 NS16 NE17 O0 IC2 B4 P0 A30 V0
H1 C30 BD1 F2 U1 K10
N 51 G0 Z10 X50
[AUXILIARY CONTOURS can be inside or
outside if they are not closed contours]
N 52 G0 X50 Z-30
N 53 G31 ID"thread" O0 IC2 B4 P0 A30 V0
H1 C30 BD1 F2 U1 K10
N 60 G0 Z10 X50
Run-in length: B = 0.75 * (F*S)² / a * 0.66 + 0.15
Run-out length: P = 0.75 * (F*S)² / a * 0.66 + 0.15
F: Thread pitch in mm/revolution
S: Speed in revolutions/second
a: Acceleration in mm/s² (see axis data)
Cycle stop—the control retracts the tool from the thread
groove and then stops all tool movements. (Lift-off
distance: OEM configuration parameter:
cfgGlobalProperties-threadliftoff)
Feed rate override is not effective.
Danger of collision!
An excessive overrun length P might cause a collision. You
can check the overrun length during the simulation.