Appendix “b, Caution – Pinnacle Systems NSD User Manual
Page 21
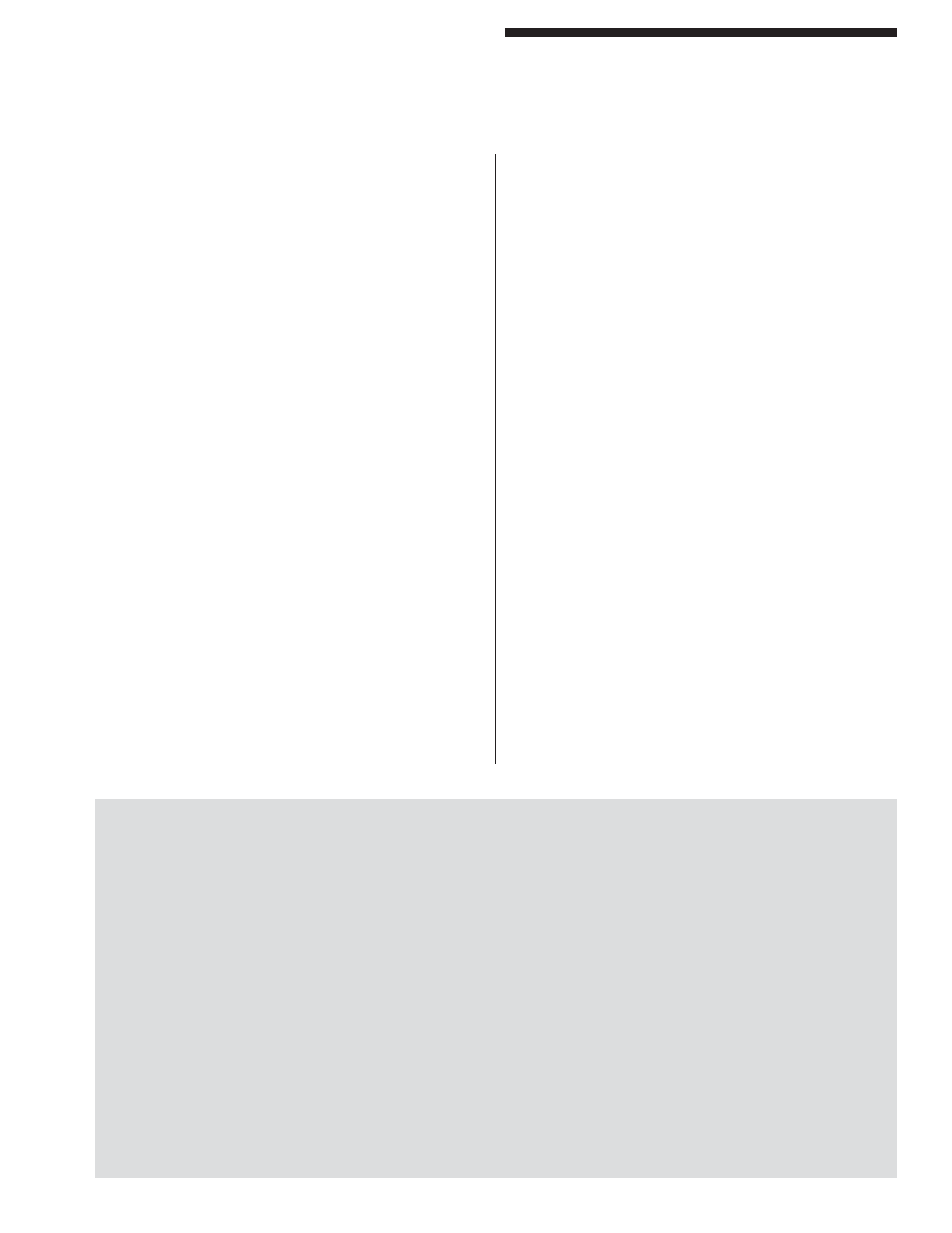
AB - 1
Appendix “B”
Safety Guidelines for Management
Safety Guidelines for Management
Operational Safety
1. Appoint a Safety Coordinator to be responsible
for safety regulations, requirements, and
suggestions. He must review and investigate
all accidents and “close calls.”
2. Establish and issue safety rules. Inform each
employee of his responsibilities. Make sure he
understands them and knows what is expected
of him.
3. A thorough review and an early inspection must
be made of existing presses, dies, and point
of operation guarding to attain the degree of
responsibility required by ANSI B11.1-2001
Safety Standards and Federal State laws.
Review what mandatory modifications are
necessary.
4. Equipment that is no longer safe and that cannot
be economically upgraded should be destroyed.
5. Never allow persons legally under age to
operate or assist in the operation of machinery.
6. All personnel must be properly trained to
eliminate accidents and injuries.
7. Regardless of the operator’s experience,
education, or language barrier, it is the
responsibility of the supervisor to give him
a thorough explanation with each new job
assignment.
! ! ! CAUTION ! ! !
When a mat system is used to protect the operator or passerby from penetration, it must be mounted and
properly sized so it is impossible to reach under, around, or over into the hazardous point of operation zone.
Safety mat systems normally guard the front or feed area of a machine. The sides of the areas where the
safety mat does not guard must be guarded by some other means or by additional safety mats.
If the position of the safety mat(s) will allow the operator or others to place themselves between the sensing
fi eld and the hazardous area, auxiliary guards or devices such as safety light curtains, barrier guards or
devices should be used in conjunction with the safety mat(s) to prevent the operator or others from exposure
to the hazardous area.
If mechanical guards such as: polyurethane, expanded or perforated metal, hairpins, etc., are used to guard
these areas, the opening must comply with the OSHA safety distance in relationship to the openings.
After installation of point of operation guards and before a job is released for operation, a check should be
made to verify that the guard will prevent the operators hands from reaching into the point of operation or any
hazard zone. Always refer to the applicable OSHA & ANSI standard in order to assure proper compliance to
the subject machine.
8. No employee should be given a work assignment
that he does not fully understand. Only properly
instructed and thoroughly trained personnel
should be assigned to work on or with any
machine.
9. It shall be the responsibility of the employer
to provide an adequate, clean, safe, and
uncluttered work area around each machine.
10. If a malfunction is reported, stop the machine
immediately, correct the problem, then resume
production.
11. Investigate all accidents and close calls.
Analyze the reason for occurrence. Take action
to prevent recurrence. Keep records of the
investigation and preventative steps that were
taken.
12.
Only
employees who understand the machines,
operation and safety requirements, and who are
able to communicate this knowledge should
be given the responsibility of instructing and
training others to perform as operators.
13.
Management must decide that personnel
protective safety equipment is required to
perform each job safely. Items such as safety
glasses, shoes, gloves, helmets, hand pads,
spats, protective sleeves and material handling
equipment are common in the metal working
industry. If noise levels are excessive, protective
headsets and earmuffs are recommended.