The beckhoff bc2000 lightbus coupler, Introduction to the beckhoff lightbus system – BECKHOFF BC2000 User Manual
Page 16
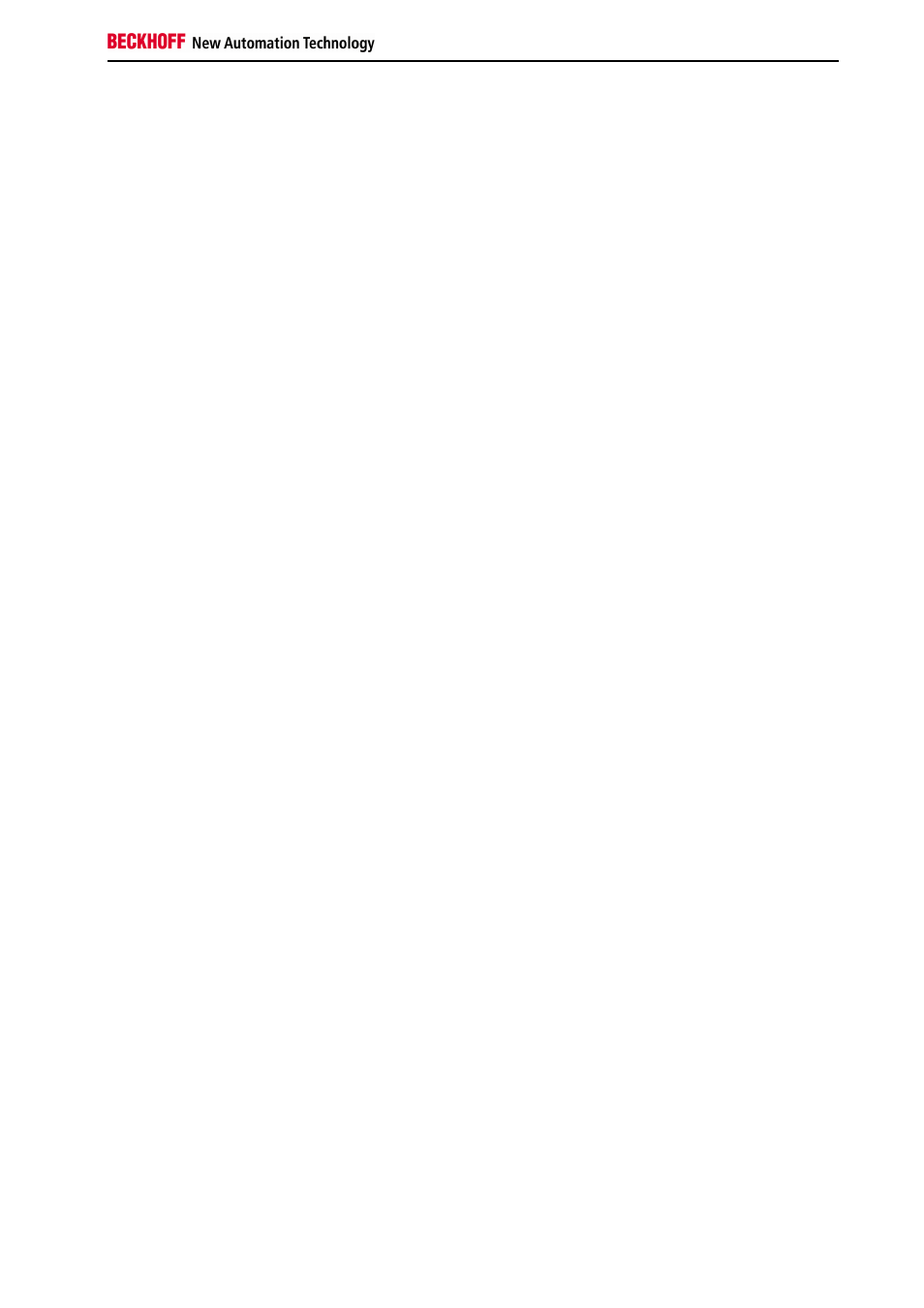
The Beckhoff BC2000 Lightbus Coupler
15
BC2000
The Beckhoff BC2000 Lightbus Coupler
Introduction to the Beckhoff Lightbus
System
The Beckhoff Lightbus has achieved wide acceptance in the world of
automation engineering through its speed and its compatibility across
manufacturers. The Beckhoff Lightbus was developed within a control
concept for the implementation of NC axes on the industry PC. The goal of
the project was to develop a fast, secure I/O level for the PC suitable for
industrial application. Nowadays a large number of various products are
available from independent manufacturers. The operation of different
Beckhoff Lightbus devices in one bus system is ensured by the
implementation support and the protocol ASICs from BECKHOFF.
The Beckhoff Lightbus is designed for fast data exchange on the sensor /
actuator level. Central control devices (such as, for example,
programmable logic controllers) communicate here over a fast serial
connection with distributed input and output devices. Data is exchanged
with these distributed devices cyclically, and, if necessary, with different
priorities. The central controller (master) reads the input information from
the slaves, and sends the output information to the slaves. The bus cycle
time must here be shorter than the central controller’s program cycle time,
which in many applications is less than 1 ms.
A high data throughput is not in itself sufficient for successful use of a bus
system. Ease of handling, good diagnostic facilities and secure
transmission technology are also of the utmost importance if the user’s
demands are to be satisfied. These properties are ideally combined in the
Beckhoff Lightbus.
For the transmission of 512 bits of input data and 512 bits of output data
distributed over 32 bus devices, the Beckhoff Lightbus needs approx.
0.8 ms at a transmission rate of 2.5 Mbit/s. The demand for a short system
reaction time is thus ideally satisfied.
System configurations and
device types
A single master system can be implemented with the Beckhoff Lightbus. A
maximum of 254 slaves can be connected to one bus. In the BC2000 bus
terminal controller, a station address between 1 and 254 is automatically
selected during the start-up phase. The specifications for the system
configuration contain the number of stations, the assignment of the station
addresses to the I/O addresses, data consistency of the I/O data and the
format of the diagnostics messages. Every Beckhoff Lightbus system
consists of different device types
A Beckhoff Lightbus slave is a peripheral device (sensor/actuator) that
reads input information and passes output information on to the
peripherals. It is also possible to have devices that only handle either input
or output information. Typical Beckhoff Lightbus slaves are devices with
binary inputs/outputs for 24 V or 230 V, analogue inputs, analogue outputs,
counters, incremental encoders etc.. The quantity of input and output
information is device-dependent, and is limited to 32 bits of input data and
32 bits of output data for each protocol ASIC. For slaves that handle more
than 32 bits of data, such as, for instance, the BC2000, an extended
procedure is utilised. Using an addressed access procedure, reading and
writing up to 256 x 16 bits is possible. This means that a system can
handle up to 254 stations x 508 bytes (not all of the 512 bytes are available
for user data) with only one Beckhoff Lightbus system. For reasons of
expense, and for technical reasons associated with implementation, the
masters that are available nowadays work with a max. user data length of
3 kbyte (24000 inputs and outputs).