Flowserve MN User Manual
Page 18
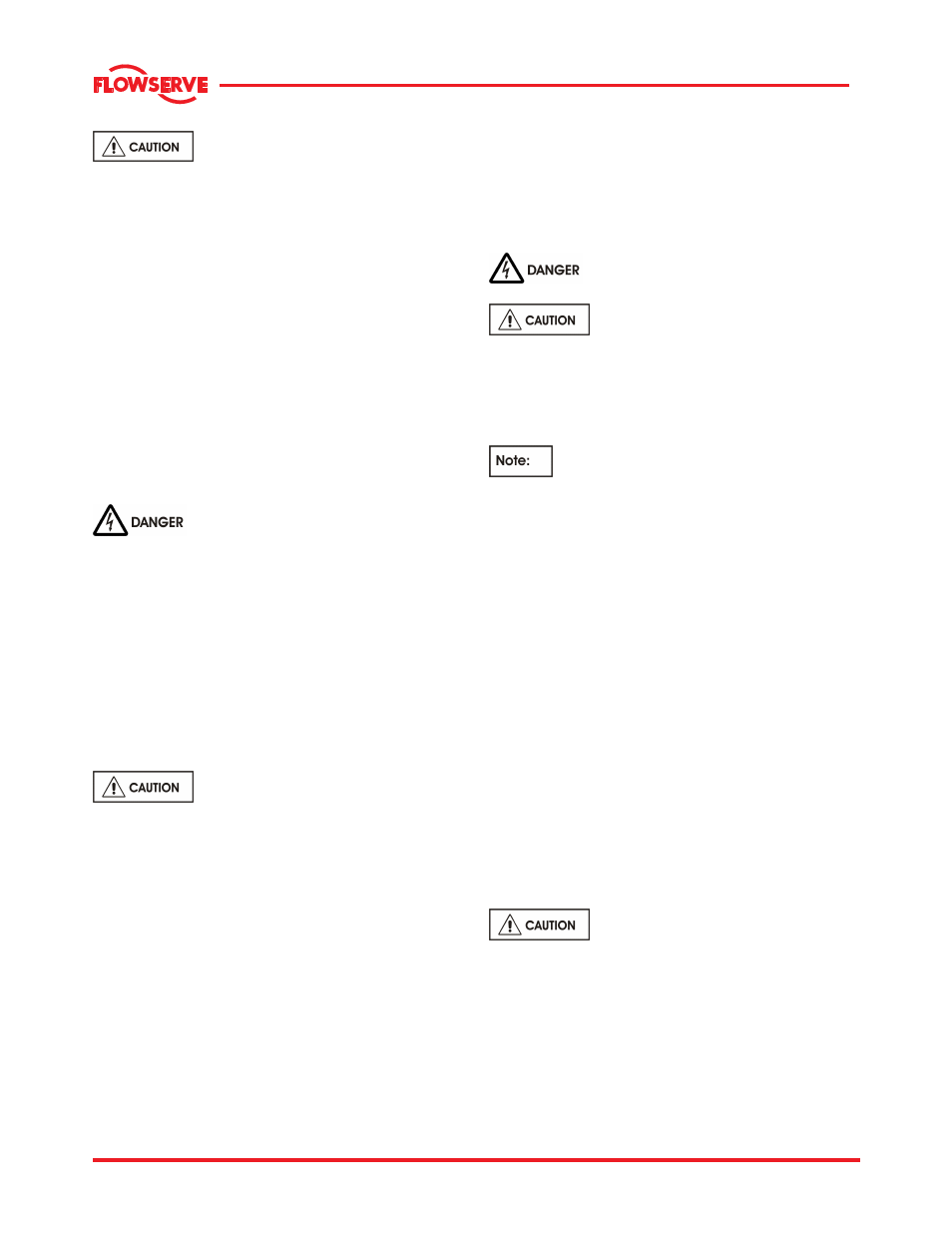
MN USER INSTRUCTIONS ENGLISH 71569189 11/04
Page 18 of 49
®
4.5 Initial alignment
The equipment is shipped from the
factory with the couplings pre-mounted. If they are to
be removed, do so by applying heat and using a
puller. Remount the couplings by heating them
evenly in an oven to approximately 135
o
C (275
o
F).
This is required as the coupling flanges are designed
for a specific interference fit. Upon removal from the
oven, position the hubs on the shafts as required.
DO NOT hammer on the flanges in an attempt to
remove them from the shaft. To do so will
permanently damage the bearings in the pump
and/or the motor.
Accurate alignment of pump and drive shafts is
essential for successful operation. Misalignment
values as near to zero tolerance as possible are
required for trouble free operation and long
equipment life.
It is a must to lock out electrical supply
to the pump and its accessories to prevent accidents
during alignment,
A flexible coupling is used to compensate for slight
changes in alignment that occur during normal
operation. It is not used to correct for initial
misalignment in excess of the values herein.
Although most couplings can withstand greater
misalignment, such can cause excessive vibration
and premature equipment failure.
4.5.1 Thermal expansion
The pump and motor will normally
have to be aligned at ambient temperature and
should be corrected to allow for thermal expansion at
operating temperature. For pump installations
involving high liquid temperatures, the unit should be
run at the actual operating temperature, shut down
and the alignment checked immediately.
4.5.2 Preparation before alignment
To ensure proper alignment the following items are
very important.
a) All machined mating surfaces (such as the
mating flanges of pump and motor) must be
clean and free of burrs and nicks.
b) Exterior strain must not be transmitted to the
pump. The most common cause of trouble in this
respect is forcing the piping to mate with the
pump. It is recommended that flexible connectors
be installed in the piping adjacent to the pump.
c) All threads should be checked for damage and
repaired if necessary. Lubricate all screwed
connections with a suitable thread lubricant (an
anti-galling compound).
4.5.3 Alignment Procedure
Ensure pump and driver are isolated
electrically and the half couplings are disconnected.
The alignment MUST be checked.
Although the pump will have been aligned at the
factory it is most likely that this alignment will have
been disturbed during transportation or handling.
If necessary, align the motor to the pump, not the
pump to the motor.
Alignment is achieved by adding or
removing shims under the motor feet and also
moving the motor horizontally as required. In some
cases where the alignment cannot be achieved, it will
be necessary to move the pump before
recommencing the above procedure.
a) Mount the pump and driver on the baseplate and
align to the pre-drilled hold-down holes. Partially
install the hold down screws and the bearing
frame support screws by engaging several
threads.
b) Use wedges and shims between the baseplate
and foundation to level the pump and driver
support pads. Ensure that the suction and
discharge flanges are level, plumb, and at the
proper elevation. Tighten down the anchor bolts
and then recheck for level and proper orientation.
c) Check the gap between the driver and driven
shafts against the dimensions shown on the
installation drawing; a 1.5 mm (0.06 in.) variation
is normally acceptable. For any necessary
adjustment, move the driver rather than the
pump.
The driver and pump were factory pre-
aligned and the baseplate mounting holes were
drilled and tapped based on that alignment. Failure
to level the base or shifting the equipment from their
natural hole centers may result in alignment difficulty
that is not covered under the warranty.