Flowserve MN User Manual
Page 34
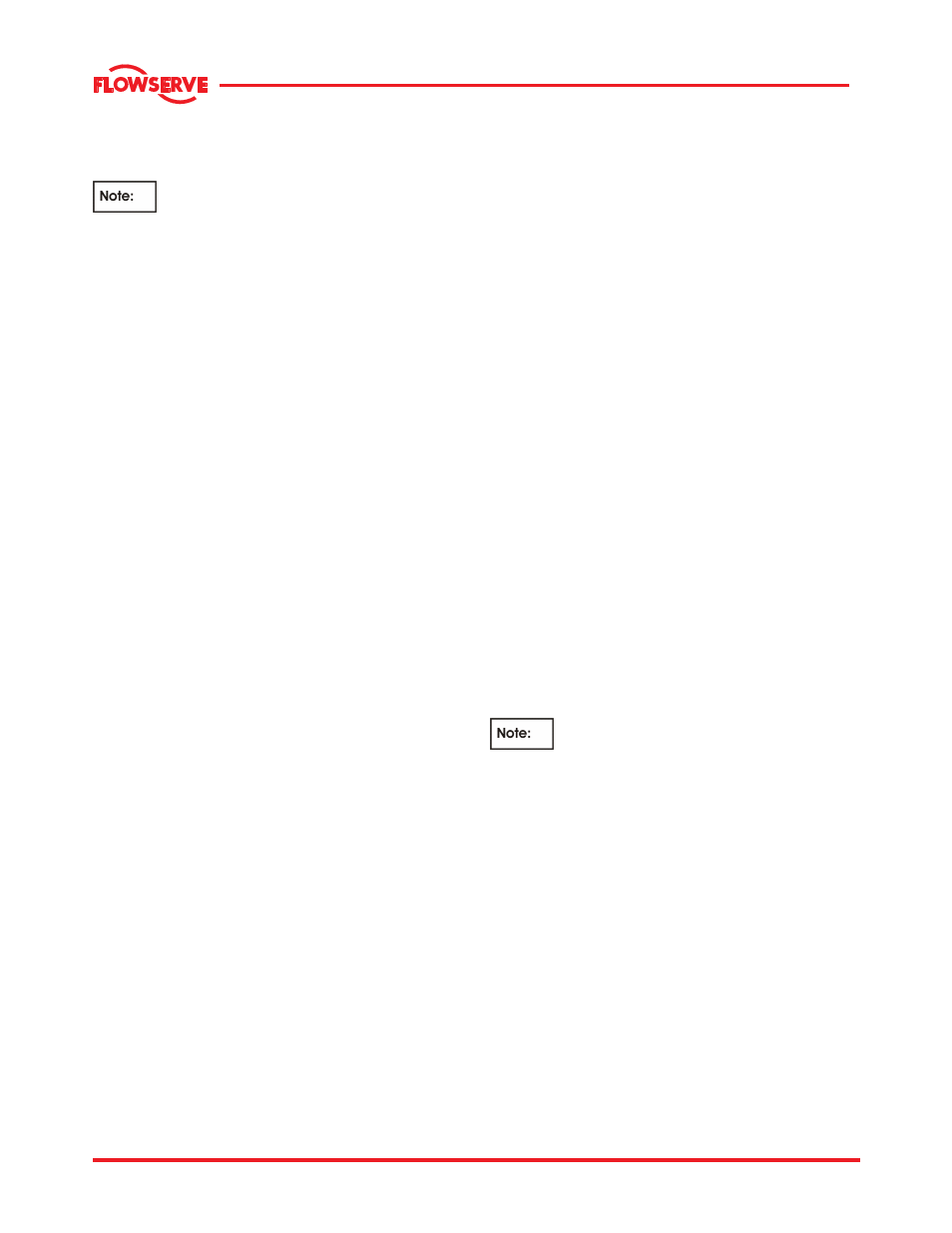
MN USER INSTRUCTIONS ENGLISH 71569189 11/04
Page 34 of 49
®
Any sleeve grooved more than 3.0 mm (0.12 in.)
deep should immediately be replaced to avoid
damage to other components.
The shaft sleeve was mounted on the shaft
using Loctite RC/680 or equivalent and may require
heating to approximately 230
o
C (450
o
F) for removal.
6.1.7.1 Shaft sleeve removal
Uniformly heat the shaft sleeve to 230
o
C (450
o
F)
and remove the sleeve while the part is hot. If this
does not work, uniformly heat the sleeve to 260
o
C
(500
o
F) and douse with cold water. This will crack
the sleeve and allow mechanical removal of the
sleeve. If heating is not practicable, it will be
necessary to cut the sleeve off.
6.1.7.2 Mounting of shaft sleeve
Clean the shaft and shaft sleeve thoroughly and
remove any oil or grease from the mating surfaces
with a non-toxic solvent. Allow the solvent to dry and
apply Loctite type RC/680 or equivalent to the sleeve
inside diameter and shaft O.D. Install the sleeve by
continuously rotating it to ensure a full and even
coating of the mating surfaces. Avoid holding the
sleeve in one position until the sleeve keyway is in
line with the shaft keyway. Immediately install the
key. This prevents "freezing" of the shaft sleeve to
the shaft. Apply adequate force to the shaft sleeve
face to ensure proper seating of the sleeve against
the shaft shoulder. This can be done by mounting
the impeller on the shaft and tightening the impeller
nut. Remove excess Loctite from the parting lines.
Loctite sealant will be fully cured in six hours.
6.1.8 Maintenance of packing
Pumps equipped with mechanical seals may have
altered stuffing box dimensions. Refer to the seal
manufacturer's installation drawing for actual box
dimensions.
Use a good grade of non-asbestos packing with a
high temperature surface lubricant for packing the
stuffing box. Do not under any circumstances use
flax packing as rapid wear of the shaft sleeve may
result. The procedure for repacking the stuffing box
follows:
a) Remove the split gland.
b) Remove the old packing and seal cage halves
and clean the stuffing box.
c) Make sure the packing to be used is of the
correct type and size. Measure the stuffing box
to determine the proper length of packing.
Packing should be cut slightly shorter than
measured to prevent butting of the ends and
buckling.
d) Insert each ring of packing separately, pushing it
as far as possible into the stuffing box and
seating it firmly. Stagger the rings so that
successive joints are 90
o
to 180
o
angles apart.
e) After installing two packing rings, insert the seal
cage. It is important to make sure the seal cage
is located directly under the seal water
connection and that the installation of successive
rings does not displace it.
f) Continue adding more rings of packing. When
the required number of packing rings have been
added, install the gland and tighten the gland
nuts by hand, then back off the nuts until the
gland is loose. In tightening the gland, the nuts
must be brought up uniformly so that the gland is
not cocked and so that the packing is subjected
to a uniform pressure.
g) New packing has to be "run in". It is a good
practice to start the pump with the stuffing box
gland quite loose. After the pump has been
running for approximately 10 to 15 minutes,
gradually tighten the stuffing box gland nuts until
leakage is reduced to a steady supply or trickle.
Packing that is too tight in the box will cause
undue friction and create heat that will glaze the
packing and possibly score the shaft sleeve.
Packing must remain soft and pliable.
It may be impossible to add the last ring of
packing to the stuffing box and still insert the gland.
When this occasion arises, omit the last ring of
packing and adjust the gland. Continue to tighten the
gland as required, allowing for proper leakage, until
the packing has seated itself well enough to allow the
final ring to be inserted. Approximately 0.113 to
0.227 m
3
/h (0.5 to 1.0 gpm) at 0.34 to 0.69 bar (5 to
10 psi) above the maximum pump discharge
pressure is recommended for sealing water. When
grease sealing is used, a similar grease pressure
should be maintained.